Abstract
The peristaltic flow of an incompressible viscous fluid in a curved channel is investigated. The flow analysis is conducted in the presence of an induced magnetic field. A long-wavelength and low-Reynolds number approach is followed. The stream function, pressure gradient, magnetic force function, induced magnetic field, and current density are constructed. We observed that symmetry in the profiles of u and ϕ is disturbed because of curvature effects. For larger values of curvature k, results of planar channel are deduced. The effects of significant parameters have been portrayed and discussed.
1 Introduction
The interest of researchers in peristaltic flows has increased substantially during the last few decades. This is due to their obvious importance not only in physiology but also in industry. Latham [1] and Shapiro et al. [2] have presented a seminal research on peristaltic flows. They studied the peristaltic flow of viscous fluid theoretically and experimentally. Hayat and Ali [3] have discussed the mechanism of peristaltic flows of power law fluids. The peristaltic motion of micropolar fluid in circular cylindrical tubes has been discussed by Muthu et al. [4]. Wang et al. [5] analyzed the slip effects on the peristaltic flow of a third-grade fluid in a circular cylinder. Currently, a large body of literature is available on peristaltic mechanism, of which some of the studies are mentioned in Refs. [6–16]. Progress is also made to such flows in the presence of uniform applied magnetic field using viscous and non-Newtonian fluids. Kothandapani and Srinivas [17] studied the peristaltic transport of a Jeffrey fluid under the effect of magnetic field in an asymmetric channel. Hakeem et al. [18] reported the effects of magnetic field on trapping through peristaltic motion for generalised Newtonian fluid in a channel. In another article, Hakeem et al. [19] have studied the hydromagnetic flow of generalised Newtonian fluid through a uniform tube with peristalsis. Hayat et al. [20–23] analyzed the MHD effects on the flows of viscous, Jeffrey, and third-order fluid models. Few more attempts regarding the peristaltic flows in the presence of an applied magnetic field have been presented in Refs. [24–26].
None of the above-mentioned articles examined the induced magnetic field effects on peristaltic flows. The first investigation on induced magnetic field was presented by Vishnyakov and Pavlov [27]. Here viscous fluids have been taken into account. Later, Mekheimer [28] has analyzed the induced magnetic field effects on the peristaltic flow of a couple stress fluid in a symmetric channel. Nadeem and Akram [29] have extended the flow analysis of [28] to an asymmetric channel. Some recent studies [29–32] are also conducted in the presence of an induced magnetic field.
Peristalsis is mostly studied in straight channels and tubes. However, the geometry of most physiological conduits and glandular ducts is curved. Modelling of microwrinkles on human skin also requires a curved geometry. The geometry of the airways and the arterial network produces swirling flows, similar to the flows found in curved or twisted pipes. In all the above-mentioned attempts, peristaltic flows have been discussed in two-dimensional channels or axisymmetric tubes. The effect of curvature seems meaningful in this context. To the best of our information, Sato et al. [33] studied the peristaltic flow in a curved channel in a laboratory frame. Ali et al. [34] studied flow analysis in a curved channel. In another article, Ali et al. [35] have discussed the heat transfer characteristics on the peristaltic flow of viscous fluid in a curved channel. Recently, the peristaltic flow of a third-order fluid in a curved channel is discussed by Ali et al. [36].
The main purpose of this current investigation is to discuss the induced magnetic field effects on the peristaltic flow of viscous fluid in a curved channel. Hence, the layout of this paper is as follows. Section 2 deals with the modelling of governing equations. Sections 3 and 4 contain the solution to the problem and graphical discussion. The last section synthesises the concluding remarks.
2 Mathematical Formulation
Let us consider a curved channel with half width a. The channel is coiled just like a circle having radius R* and centre O. An incompressible viscous fluid fills the space in a curved channel. A sinusoidal wave of velocity c propagates on the channel walls. We choose coordinates
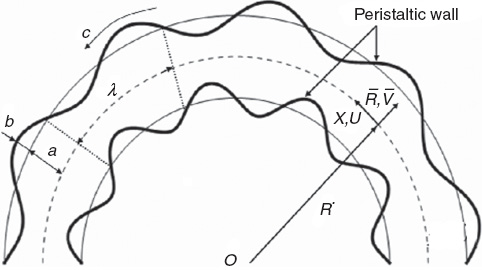
Geometry of flow problem.
An external magnetic field of strength

in which λ is the wavelength, a is the channel half width,

The governing equations are

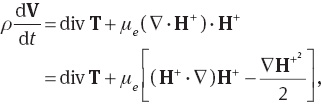


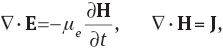

In the above equations, ς= σμe denotes the magnetic diffusivity, σ is the electrical conductivity, μe is the magnetic permeability, ρ is the density, d/dt the material derivative, T the Cauchy stress tensor, and J, E, and H the current density, the electric field, and the magnetic field respectively. The expression for

in which
Here the coordinates and velocities in the fixed

Employing the computations of (3)–(5) through (10), we approach at


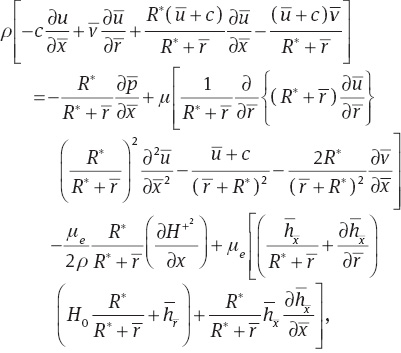
where

where δ, Re, Rm, S, and M are the wave, Reynolds, magnetic Reynolds, Stommer’s, and Hartman numbers, respectively. The total pressure pm is the sum of ordinary and magnetic pressures, E is the electric field strength, ψ is the stream function, and ϕ is the magnetic force function.
We finally obtain
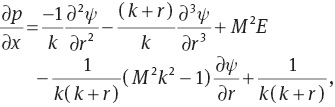

Note that a long-wavelength approximation at a low Reynolds number has been used in obtaining (15) and (16). These further give

The boundary conditions are

where the dimensionless time mean flow rate F in the wave frame is related to the dimensionless time mean flow rate θ in the laboratory frame as
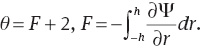
3 Solution of Problem
Solving (15)–(18), we have
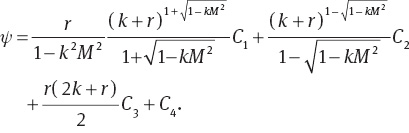


The involved Ci(i= 1–4), Bj(j= 1, 2), and bk (k= 1, 2) are constants. The dimensionless expressions of axial induced magnetic field hx, current density Jz, and pressure rise ΔPλ are

4 Discussion
In this section, we discuss the effects of curvature k, Hartmann number M, and magnetic Reynolds number Rm appearing in the various flow quantities such as axial pressure gradient (dp/dx), pressure rise per wavelength ΔPλ, longitudinal velocity u, axial induced magnetic field hx, and current density Jz. We have plotted Figures 2–7 to serve the purpose.
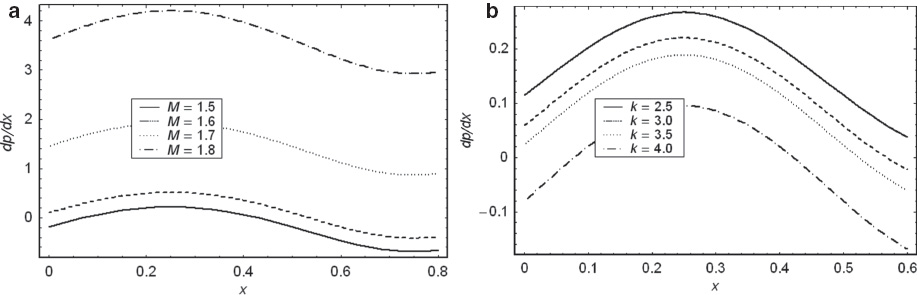
(a) The pressure gradient dp/dx versus x for α= 0.1, E= 1, k= 10 and θ= 1.5. (b) The pressure gradient dp/dx versus x for α= 0.1, E= 1, k= 1.5, and θ= 0.6.
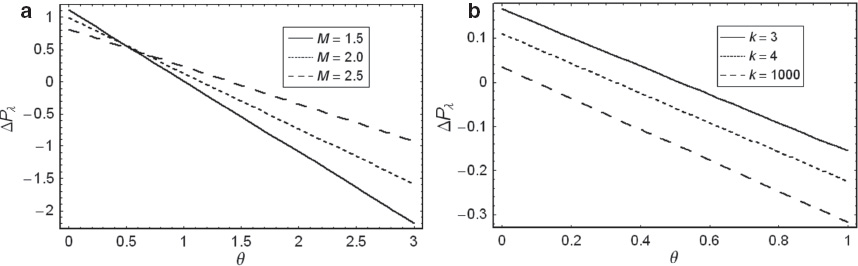
(a) The pressure rise ΔPλ versus flow rate θ for α= 0.4, k= 2, and E= 1. (b) The pressure rise ΔPλ versus flow rate θ for α= 0.1, M= 1.4, and E= –1.
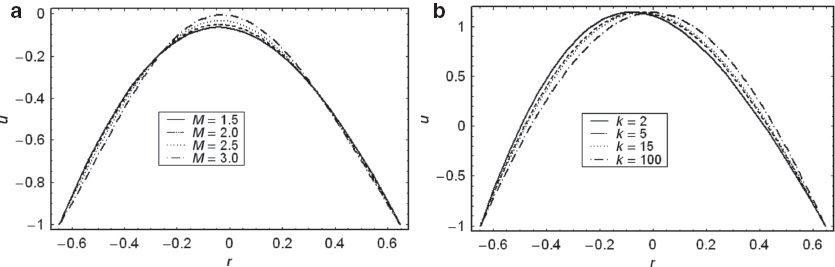
(a) The axial velocity u versus r for α= 0.6, k= 3, x= 0.6, and θ= 1.5. (b) The axial velocity u versus r for α= 0.6, M= 1.9, x= 0.6, and θ= 2.5.
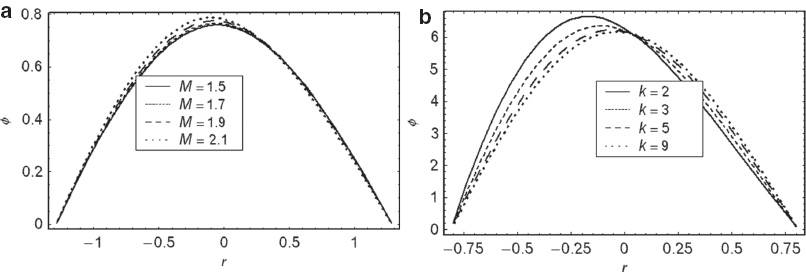
(a) The magnetic force function ϕ versus r for α= 0.3, k= 20, E= 0.8, x= 0.2, Rm= 1, and θ= –2. (b) The magnetic force function ϕ versus r for α= 0.3, k= 20, E= 0.8, x= 0.2, Rm= 1, and θ= –2.
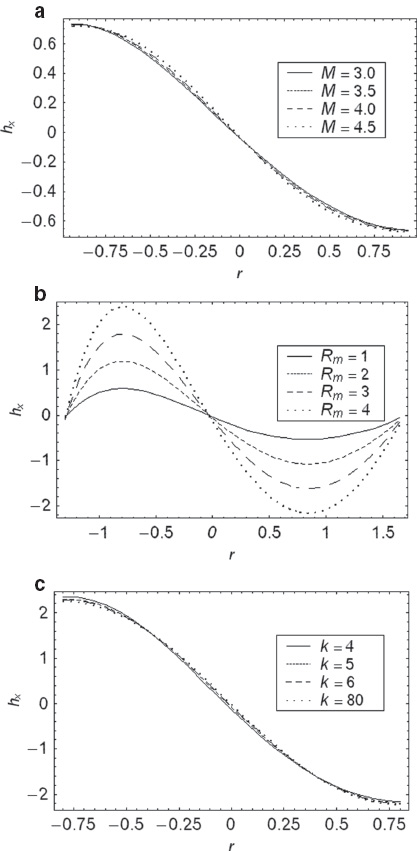
(a) The axial induced magnetic field hx versus r for α= 0.1, M= 2.5, L= 1, Rm= 4, x= –0.2, and θ= 1. (b) The axial induced magnetic field hx versus r for α= 0.2, M= 2.5, L= 1, k= 4, x= –0.2, and θ= 1. (c) The axial induced magnetic field hx versus r for α= 0.1, M= 2.5, L= 1, Rm= 4, x= –0.2, and θ= 1.5.
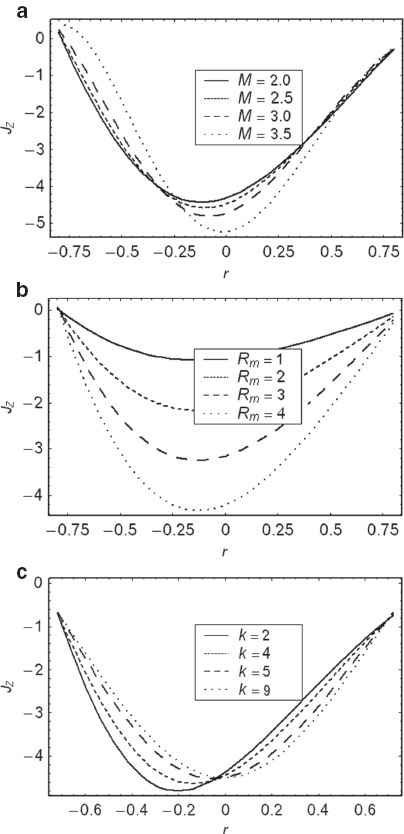
(a) Current density Jz versus r for α= 0.2, Rm= 4, k= 4, x= –0.2, E= 1, and θ= 1.5. (b) Current density Jz versus r for α= 0.2, M= 1.5, k= 4, x= –0.2, E= 1, and θ= 1.5. (c) Current density Jz versus r for α= 0.2, Rm= 4, M= 2.5, x= –0.2, E= 1, and θ= 1.5.
4.1 Pumping Characteristics
Figure 2a discusses the impact of M on an axial pressure gradient. The magnitude of dp/dx is directly proportional with M for the fixed values of other parameters. Figure 2b discusses the curvature effects on pressure gradient. We observe that with the decrease in k i.e., an increase in the curvature of channel, dp/dx decreases.
Figure 3a is plotted to show the variation of pressure rise ΔPλ against mean flow rate θ for different values of M. The pumping action is due to the dynamic pressure exerted by the walls on the fluid trapped between the contraction regions. Figure 3a shows that an increase in M causes a we observe that ΔPλ in the pumping region (Δpλ> 0, θ> 0) decreases by increasing M for the fixed values of flow rate θ. However, for the case of copumping (Δpλ< 0) and free pumping (Δpλ= 0), the flow rate θ is an increasing function of M. Deviation in behaviour of Hartmann number M on ΔPλ is because of the incorporation of curvature effects. For a large value of k, the results of planar channel are deduced [28].
The effect of curvature parameter k on pressure rise is discussed in Figure 3b. We observe that the value of ΔPλ decreases as one moves from a curved to a straight channel, i.e., peristalsis has to work against greater pressure rise in curved channel than in straight channel. Also, the free pumping flux increases when going from a curved to a straight channel. In the copumping region, where the pressure assists the flow, the pumping rate for the straight channel is greater in magnitude as compared with the curved channel.
4.2 Flow Characteristics
Figure 4a illustrates the axial velocity distribution u for different values of Hartman number M. We notice that the velocity profile is not symmetric about the central line of the channel due to channel curvature. The behaviour of M near the walls of the channel is quite opposite to that of the centre of channel. The magnitude of velocity decreases as M increases at r= 0.
In Figure 4b, the axial velocity u is plotted for various values of curvature parameter k. The maxima in profile is an increasing function of k. It is also inferred that profiles are not symmetric about r= 0. However, symmetry can be achieved as k→ ∞.
4.3 Magnetic Field Characteristics
Figure 5a and b shows the magnetic field characteristics under the influence of Hartmann number M and curvature parameter k. The profiles for magnetic force function are parabolic in nature. A left shift in the profiles is observed at r= 0. Magnetic force function is zero at the walls, which is in accordance with the boundary condition imposed on it. Profiles are an increasing function of k and decreasing function of M near the upper wall of channel. Figure 6a and c shows the variation of axial induced magnetic field hx against r for different values of M, Rm, and k. In the half region, induced magnetic field is in one direction, whereas in the other half, it is in the opposite direction. The magnitude of hx increases with M and Rm increment. While curvature parameter k shows a mixed effect on the magnitude of induced magnetic field. The current density distribution Jz for different values of M, Rm and k is plotted in Figure 7a and c. We observe that the curves of Jz are parabolic in nature, and the magnitude of current density Jz increases at the centre of the channel, and decreases near the walls with increasing M. A shift in the profiles is observed toward the lower wall. Figure 7b eulicidates that Jz is an increasing function of Rm.
Figure 7c is plotted in order to discuss the behaviour of curvature parameter k on current density. It is found that an increase in k causes an increase in magnitude of Jz at the upper half of the channel. For large values of k, symmetry in the profiles is achieved.
5 Concluding Remarks
The aim of study is to obtain an analytical solution for the effects of induced magnetic field on the peristaltic transport of viscous fluid in a curved channel. The following observations have been found
Symmetry in the profiles of u and ϕ is disturbed because of curvature effects.
The qualitative behaviour of k and M on dp/dx is the opposite.
ΔPλ is a decreasing function of k and M in a curved channel.
The magnitude of velocity u is an increasing function of k while it decreases at the centre line of the channel when M increases.
ϕ is an increasing function of k and a decreasing function of M near the upper wall of the channel.
Magnitude hx increases with Rm and decreases with k and M.
The magnitude of Jz has an increasing effect for Rm, k, and M about r= 0.
References
[1] T. W. Latham, MIT Cambridge, MA 1966.Search in Google Scholar
[2] A. H. Shapiro, M. Y. Jaffrin, and S. L. Weinberg, J. Fluid Mech. 37, 799 (1969).Search in Google Scholar
[3] T. Hayat and N. Ali, Physica A: Statistical and Theoretical Physics 371, 188 (2006).10.1016/j.physa.2006.03.059Search in Google Scholar
[4] P. Muthu, B. V. R. Kumar, and P. Chandra, Appl. Math. Model. 32, 2019 (2008).Search in Google Scholar
[5] Y. Wang, N. Ali, T. Hayat, and M. Oberlack, ASME J. Appl. Mech. 76, 011006100 (2009).Search in Google Scholar
[6] S. Srinivas and M. Kothandapani, Int. Comm. Heat Mass Transfer 35, 514 (2008).10.1016/j.icheatmasstransfer.2007.08.011Search in Google Scholar
[7] K. Vajravelu, G. Radhakrishnamacharya, and V. R. Murty, Int. J. Nonlinear Mech. 42, 754 (2007).Search in Google Scholar
[8] S. Nadeem and S. Akram, Comm. Nonlinear Sci. Numer. Simul. 15, 1705 (2010).Search in Google Scholar
[9] Abd El Hakeem Abd El Naby, J. Appl. Mech. 76, 064504 (2009).Search in Google Scholar
[10] M. H. Haroun, Comm Nonlinear Sci. Numer. Simul. 12, 1464 (2007).Search in Google Scholar
[11] D. Tripathi, Appl. Math. Comput. 215, 3645 (2010).Search in Google Scholar
[12] T. Hayat, Q. Hussain, and N. Ali, Phys. Lett. A 387, 3399 (2008).10.1016/j.physa.2008.02.040Search in Google Scholar
[13] T. Hayat, M. U. Qureshi, and N. Ali, Phys. Lett. A 372, 2653 (2008).10.1016/j.physleta.2007.12.049Search in Google Scholar
[14] T. Hayat, A. Afsar, and N. Ali, Math. Computer Modelling 47, 380 (2008).10.1016/j.mcm.2007.04.012Search in Google Scholar
[15] M. A. Abd Elnaby and M.H. Haroun, Comm. Nonlinear Sci. Numer. Simul. 13, 752 (2008).Search in Google Scholar
[16] S. Srinivas and M. Kothandapani, Appl. Math. Comput. 213, 197 (2009).Search in Google Scholar
[17? M. Kothandapani and S. Srinivas, Int. J. Non-Linear Mech. 43, 915 (2008).Search in Google Scholar
[18] Abd El Hakeem Abd El Naby, A. E. M. El Misery, and M. F. Abd El Kareem, Physica A 367, 79 (2006).10.1016/j.physa.2005.10.045Search in Google Scholar
[19] Abd El Hakeem Abd El Naby, A.E.M. El Misiery, and I. El Shamy, Appl. Math. Comput. 173, 856 (2006).Search in Google Scholar
[20] T. Hayat and N. Ali, Appl. Math. Comput. 188, 1491 (2007).Search in Google Scholar
[21] T. Hayat, N. Ahmad and N. Ali, Comm. Nonlinear Sci. Numer. Simul. 13, 1581 (2008).Search in Google Scholar
[22] T. Hayat, A. Afsar, M. Khan, and S. Asghar, Comp. Math. Applications 53, 1074 (2007).10.1016/j.camwa.2006.12.014Search in Google Scholar
[23] T. Hayat, M. Khan, A. M. Siddiqui, and S. Asghar, Comm. Nonlinear Sci. Numer. Simul. 12, 910 (2007).Search in Google Scholar
[24] T. Hayat and N. Ali, Comm. Nonlinear Sci. Numer. Simul. 13, 1343 (2008).Search in Google Scholar
[25] Kh. S. Mekheimer, Appl. Math. Comput. 153, 763 (2004).Search in Google Scholar
[26] N. T. M. Eldabe, M. F. Al-Sayad, A. Y. Galy, and H.M. Sayed, Physica A 383, 253 (2007).10.1016/j.physa.2007.05.027Search in Google Scholar
[27] V. I. Vishnyakov and K. B. Pavlov, Translated from Magnitnaya Gidrodinamika 8, 174 (1972).Search in Google Scholar
[28] Kh. S. Mekheimer, Phys. Lett. A 372, 4271 (2008).10.1016/j.physleta.2008.03.059Search in Google Scholar
[29] T. Hayat, S. Noreen, and A. Alsaedi, App. Math. Mech. 33, 1035 (2012).Search in Google Scholar
[30] T. Hayat, S. Noreen, and A. Alsaedi, J. Mech. in Med. Bio. 12, 1250058 (2012).Search in Google Scholar
[31] S. Noreen and M. Qasim, The European Physical Journal – Plus 128, 1 (2013).10.1140/epjp/i2013-13091-3Search in Google Scholar
[32] S Noreen, The European Physical Journal Plus 129, 1 (2014).10.1140/epjp/i2014-14033-3Search in Google Scholar
[33] H. Sato, T. Kawai, T. Fujita, and M. Okabe, The Japan Soc. Mech. Eng. B 66, 679 (2000).10.1299/kikaib.66.679Search in Google Scholar
[34] N. Ali, M. Sajid, and T. Hayat, Zeitschrift Fur Naturforschung A 65, 191 (2010).10.1515/zna-2010-0306Search in Google Scholar
[35] N. Ali, M. Sajid, T. Javed, and Z. Abbas, Int. J. Heat Mass Transfer 53, 3319 (2010).10.1016/j.ijheatmasstransfer.2010.02.036Search in Google Scholar
[36] N. Ali, M. Sajid, T. Javed, and Z. Abbas, Eurp. J. Mech. B/Fluids 29, 387 (2010).10.1016/j.euromechflu.2010.04.002Search in Google Scholar
©2015 by De Gruyter