-
Hintergrund
der Erfindung
-
Druckempfindliche
Klebstoffe bzw. Haftklebemittel (gelegentlich als PSA bezeichnet),
die bei Raumtemperatur in trockener Form dauerhaft klebrig sind,
werden in großem
Umfang für
die Herstellung von Etiketten und Bändern verwendet, die auf eine
Vielzahl von Substraten aufgebracht werden können und bei der Anwendung
von geringem Druck haften. Sie werden auch für das Laminieren von Polymerfilmen
bzw. -folien, wie Poly(vinylchlorid) und Polyester Mylar, mit Silicon
beschichtetes Papier und Folientrennschichten für die Herstellung von Abziehbildern
und anderen verwandten Produkten verwendet.
-
Wäßrige Haftklebemittel
sind aufgrund ihrer geringen VOC-Emissionen von Interesse. Obwohl
die Lösung
der von auf Lösungsmittel
basierenden Haftklebemitteln nicht äquivalent ist, erfüllen sie
die Emissionsstandards und lassen sich leicht verarbeiten. Übliche Arten
von Haftklebemitteln, sowohl auf Wasser als auch auf Lösungsmittel
basierende, stammen von auf Acrylester basierenden Copolymeren,
wie Alkylacrylat- und Acrylmethacrylat-Copolymeren.
-
Die
folgenden Patente und Artikel sind repräsentative Beispiele von auf
Acryl basierenden Haftklebemitteln:
Hidalgo, et al. "Polystyrene(1)poly(butyl
acrylate-methacrylic acid)(2) core-shell emulsion polymers. Part
II: Thermomechanical properties of latex films," Colloid and Polymer Science, 1992,
Bd. 270, S. 1208-1221
offenbaren die Erzeugung von Polystyrol/Poly(butylacrylat-methacrylsäure)-Latices
durch ein zweistufiges Verfahren. Zuerst wird ein Impfmaterial aus
Polystyrol hergestellt, und danach werden Butylacrylat und Methacrylsäure in Gegenwart
des Impfmaterials polymerisiert, wodurch ein Kern/Hüllen-Polymer
in einem Verhältnis
von 2/3 erzeugt wird.
-
EP 0 593231 A1 offenbart
die Herstellung von Acrylhaftklebemitteln, indem oberflächenaktive
Mittel aus einem Ethylenoxid-Propylenoxid-Blockcopolymer mit einem geringen Molekulargewicht
(< 7000) zu Acrylhaftklebemitteln
gegeben wird, um die Adhäsion
bei geringen Temperaturen zu verbessern. Diese Haftklebemittel basieren
auf 2-Ethylhexylacrylat
und Acryl- und Methacrylestern von C
4-12-Alkanolen,
wie Butylacrylat.
-
US 6,225,401 offenbart filtrierbare
wäßrige Dispersionen
eines Haftklebemittels, das für
Etiketten geeignet ist und durch Copolymerisieren von Acryl- oder
Methacrylestern in Gegenwart eines Inhibitors erzeugt wird. Im Emulsionspolymerisationsverfahren
kann eine große
Vielzahl von härtenden
Comonomeren enthalten sein, und dazu gehören Styrole, Acrylnitril, Vinylester
usw.
-
US 6,254,985 offenbart wäßrige Emulsionen
von Haftklebemitteln, die auf Estern von Acryl- und Methacrylsäure basieren.
Die Patentinhaber offenbaren die Verwendung eines Emulgators, der
aus mindestens 5 Gew.-% aromatischer Kohlenstoffatome besteht, wobei
er typischerweise mindestens zwei Sulfonatgruppen einschließt, um die
Adhäsion
und Kohäsion
zu verbessern.
-
M.
Hidalgo et al. offenbaren in Colloid % Polymer Science, Darmstadt,
DE (1992), 270, 1208-1221 strukturierte Latexpartikel aus Polystyrol/Poly(n-butylacrylatmethacrylsäure), die
durch ein zweistufiges Emulsionspolymerisationsverfahren hergestellt
werden, wobei ein Impfmaterial aus Polystyrollatex und unterschiedliche
Verhältnisse
zwischen n-Butylacrylat und Methacrylsäure verwendet werden.
-
EP 0 554 832 betrifft einen
wäßrigen,
feuchtigkeitsbeständigen
Haftklebemittellatex mit hohem Feststoffbehalt, der eine geringe
Beschichtungsviskosität
und eine starke Scherung, eine hohe Komplianz und einen geregelten
Adhäsionsaufbau
aufweist.
-
Kurze Beschreibung
der Erfindung
-
Die
vorliegende Erfindung betrifft eine Verbesserung bei einem Verfahren
zur Herstellung einer wäßrigen Emulsion
eines Haftklebemittels, das auf Acrylestern basiert, bei dem die
Adhäsions-
und Kohäsionseigenschaften
gut ausgeglichen sind, und die entstehende Emulsion. Bei diesem
grundsätzlichen
Verfahren wird eine Haftklebemittelformulierung, die aus zumindest
einem Ester von Acryl- oder Methacrylsäure besteht, in Gegenwart von
Wasser und eines Emulgators polymerisiert, wodurch ein emulsionspolymerisiertes
Haftklebemittelpolymer erzeugt wird. Die Verbesserung besteht in
der Durchführung
der Polymerisation der Haftklebemittelformulierung, die aus einem
Ester von Acryl- oder Methacrylsäure
und einem styrolhaltigen Polymer, Impflatex, das mindestens 80 Gew.-%
Styrol enthält,
besteht, wobei das styrolhaltige Polymer durch Emulsionspolymerisation
hergestellt ist und in einer Menge von 5 bis 30 Gew.-% der Haftklebemittelformulierung
vorliegt.
-
Es
können
deutliche Vorteile des Verfahrens und des Produktes erreicht werden,
und dazu gehören:
die
Möglichkeit,
einen geringen Anteil, auf Acryl- und Methacrylester bezogen, eines
kostengünstigen
Füllstoffpolymers
in ein wäßriges Haftklebemittel
einzuführen,
ohne daß die
Klebeeigenschaften nachteilig beeinflußt werden;
die Möglichkeit,
Mängel
bei der Filmbildung von Gemischen von Polymeren, z.B. Gemischen
von Polystyrol und Acryl- und Methacryl-Copolymeren, zu beseitigen;
die
Möglichkeit,
einen kostengünstigen "Füllstoff" nach einem einfachen Verfahren in einem
Haftklebemittel aufzunehmen, ohne daß eine spezielle Vorrichtung
erforderlich ist;
die Möglichkeit,
ein Haftklebemittel mit einem Polystyrolfüllstoff mit einem hohen Tg-Wert
in einer Reaktion und in einem einzigen Reaktor herzustellen, wobei
die Leistungsvorteile des Haftklebemittels, einschließlich der durch
das Mischverfahren erzeugten, erhalten bleiben; und
die Notwendigkeit,
daß der
Polystyrollatex mit hohem Tg-Wert eine bestimmte Partikelgröße haben
muß, der Bedarf
an teuren Macromeren und Mindestmengen an oberflächenaktiven Mitteln können entfallen.
-
Ausführliche
Beschreibung der Erfindung
-
Die
Emulsionspolymerisation einer Haftklebemittelformulierung, die aus
Estern von Acryl- und Methacrylsäure,
einschließlich
ethylenisch ungesättigter
Monomere, besteht, zur Herstellung von wäßrigen Emulsionen eines Haftklebemittelpolymers
ist allgemein bekannt. Eine repräsentative
Haftklebemittelformulierung besteht aus einer wäßrigen Polymerdispersion, wobei
das Polymer aus polymerisierten Einheiten, bezogen auf das Gesamtgewicht
der Einheiten, von (a) 60 bis 95 Gew.-% von zumindest einem C6-12-Alkylacrylat,
(b) 0 bis 10 Gew.-% einer ethylenisch ungesättigten Verbindung mit einem
Umwandlungspunkt zweiter Ordnung von mehr als 0°C und ohne funktionelle Gruppen,
abgesehen von einer ethylenisch ungesättigten Gruppe, (c) 0 bis 10
Gew.-% einer ethylenisch
ungesättigten
Verbindung mit mindestens einer Säure- oder Säureanhydridgruppe und (d) 0
bis 20 Gew.-% einer weiteren ethylenisch ungesättigten Verbindung besteht,
wobei die Gewichtsprozentsätze
auf dem Gesamtgewicht des Polymers basieren. Typischerweise sind
die ungesättigten
Verbindungen in der Gruppe (c) und (d) jeweils mit weniger als 5
% enthalten, falls sie verwendet werden. Somit bilden die Verbindungen
in der Gruppe (c) und (d) einen geringen Anteil des Haftklebemittels.
-
Besonders
geeignete Alkylacrylate in der Gruppe (a) sind 2-Ethylhexylacrylat,
Octylacrylat, Decylacrylat oder Dodecylacrylat.
-
Die
Monomere in der Gruppe (b) können
einschließen:
Methylmethacrlyat, Methylacrylat, n-Butylacrylat und ter.-Butylacrylat;
Vinylester von C1-20-Carbonsäuren, wie
Vinyllaurat, -stearat, -propionat, die Vinylester von Versatinsäure und
Vinylacetat; vinylaromatische Verbindungen, wie Styrol, usw. Methylmethacrylat ist
bevorzugt.
-
Zu
Beispielen der Monomere der Gruppen (c) können Acryl- und Methacrylsäure, Maleinsäure oder Maleinsäureanhydrid
gehören.
Zu den Monomeren der Gruppen (d) können C1-C10-Hydroxyalkyl(meth)acrylate gehören.
-
Beim
Verfahren zur Herstellung des Haftklebemittels, das das styrolhaltige
Polymer, z.B. einen Polystyrolfüllstoff,
einschließt,
gibt es zwei Mechanismen. Bei einem Mechanismus wird ein styrolhaltiges
Polymer in einer Haftklebemittelformulierung gelöst, die aus einem Monomergemisch
besteht. Die entstandene Lösung wird
dann mit oberflächenaktiven
Mitteln und Wasser und mit Hilfe der Energie emulgiert, die durch
Mischen mit starker Scherung zugeführt wird, in eine stabile Emulsion
von Partikeln mit einer relativ geringen Partikelgröße überführt. Die
entstandene Emulsion wird durch Emulsionspolymerisation polymerisiert.
Bei einem zweiten Verfahren wird ein Impflatex aus einem Styrolpolymer
durch Emulsionspolymerisation hergestellt, und die Emulsion der
Haftklebemittelformulierung wird in Gegenwart dieses Impflatex polymerisiert.
Das zweite Verfahren hat den Vorteil, daß im Endprodukt weniger Emulgator
möglich
ist, das Mischen bei starker Scherung entfällt und die Reaktion in einem
einzigen Reaktor durchgeführt
werden kann.
-
Das
styrolhaltige Polymer ist ein solches, das mindestens 80 Gew.-%
Styrol enthält,
und typischerweise eins, das 100 Gew.-% Styrol enthält.
-
Wahlfreie
Monomere, die bei der Herstellung von styrolhaltigen Polymeren enthalten
sein können,
sind α-Methylstyrol,
p-Methylstyrol, Acrylnitril, Methacrylnitril, Methacrylnitril, Methylmethacrylat
und Spurenmengen von anderen Monomeren, die zu einem Polymer mit
einem hohen Tg-Wert, mindestens 80°C, führen.
-
Das
Styrolcopolymer wird in einer Menge von 5 bis 30 %, auf das Gewicht
bezogen, das das Haftklebemittelpolymer und das styrolhaltige Polymer
einschließt,
in das Haftklebemittel eingeführt.
Mengen von mehr als etwa 30 Gew.-% beeinträchtigen die Leistung des Haftklebemittels.
Mengen unter etwa 5 Gew.-% erzielen keine Vorteile in bezug auf
die Kosten, obwohl sie die Eigenschaften des Haftklebemittels nicht
nachteilig beeinflussen. Die Menge Styrolcopolymers beträgt vorzugsweise
10 bis 20 Gew.-%.
-
Viele
Haftklebemittelformulierungen schließen Styrol als Comonomer ein.
Styrol ist gewöhnlich
in geringen Mengen, z.B. weniger als 5 Gew.-%, enthalten. Große Styrolmengen
in der Haftklebemittelformulierung führen zu einem inakzeptabel
hohen Tg-Wert des Haftklebemittelpolymers. Solche großen Styrolmengen
beeinflussen die Klebrigkeit einer Schlaufe beim PSA nachteilig.
Die Möglichkeit,
eine Styrolmenge durch Copolymerisation in das Haftklebemittelpolymer
einzuführen,
die gleich der ist, wenn die Haftklebemittelformulierung, wie beim
Hybridverbundstoff, in Gegenwart eines styrolhaltigen Polymers polymerisiert
wird, stellt keine akzeptable Wahl dar.
-
Die
Haftklebemittelformulierung ist so gestaltet, daß sie zu einem Hybridverbundstoff
mit einem Tg-Wert von –25
bis –90°C, vorzugsweise
von –40
bis –75°C, und einem
Adhäsionswert
bei der Klebrigkeit einer Schlaufe laut dem Testverfahren "Pressure-sensitive
TestCouncil" (PSTC)
PSTC-5 von mehr als 1 pound per linear inch (pli), vorzugsweise
mehr als 1,5 pli führt,
die auf einer Platte aus rostfreiem Stahl getestet wird. Obwohl
der Tg-Wert nicht wie bei einem einzigen Poly mer ausreichend definiert
ist, erzielt der Tg-Wert des Verbundstoffs einen Annäherungswert.
-
Die
Polymerisation des Impflatex sowie auch der Haftklebemittelformulierung
kann durch thermische Initiatoren oder ein Redox-System eingeleitet
werden. Ein thermischer Initiator wird typischerweise bei Temperaturen
von oder mehr als etwa 70°C
verwendet, und Redox-Systeme sind bei Temperaturen von weniger als etwa
70°C bevorzugt.
Die bei diesem Verfahren verwendete Menge des thermischen Initiators
beträgt
0,1 bis 3 Gew.-%, vorzugsweise nicht mehr als etwa 0,5 Gew.-%, auf die gesamten
Monomere bezogen. Thermische Initiatoren sind auf dem Fachgebiet
von Emulsionspolymeren allgemein bekannt und dazu gehören z.B.
Ammoniumpersulfat, Natriumpersulfat und dgl. Die Menge des Oxidations-
und des Reduktionsmittels im Redox-System beträgt etwa 0,1 bis 3 Gew.-%. Es
kann irgendein auf diesem Fachgebiet bekanntes geeignetes Redox-System
verwendet werden; das Reduktionsmittel kann z.B. ein Bisulfit, ein
Sulfoxylat, Ascorbinsäure, Erythorbinsäure und
dgl. sein. Das Oxidationsmittel kann Wasserstoffperoxid, organisches
Peroxid, wie t-Butylperoxid, Persulfate und dgl. einschließen.
-
Kettenübertragungsmittel,
die auf dem Fachgebiet der wäßrigen Emulsionspolymerisation
allgemein bekannt sind, werden typischerweise verwendet, sind jedoch
nicht erforderlich. Zu Beispielen gehören Dodecylmercaptan, Mercaptocarbonsäuren und
Ester von Mercaptocarbonsäure.
Das Kettenübertragungsmittel wird
in Mengen von etwa 0,01 bis 0,5 Gew.-%, vorzugsweise von 0,02 bis
0,15 Gew.-%, bezogen auf das Gewicht der Monomere, zugesetzt.
-
Wirksame
Temperaturen für
die Emulsionspolymerisationsreaktion liegen im Bereich von etwa
50 bis etwa 100°C,
wobei dies davon abhängt,
ob der Initiator ein thermischer oder ein Redox-System ist.
-
Die
Emulgatoren, die geeignet verwendet werden, sind typischerweise
anionisch, nichtionisch oder Gemische davon. Zu geeigneten nichtionischen
Emulgatoren gehören
Polyoxyethylen-Kondensate. Polyoxyethylen-Kondensate können mit
der allgemeinen Formel R-(CH2CH2O-)nH angegeben werden, wobei R der Rest eines
Fettalkohols mit 10 bis 18 Kohlenstoffatomen, ein Alkylphenol, eine
Fettsäure
mit 10 bis 18 Kohlenstoffatomen, ein Amid, ein Amin oder ein Mercaptan
ist und wobei n eine ganze Zahl von 1 oder mehr ist. Die oberflächenaktiven
Mittel Igepal gehören
zu einer Reihe von Alkylphenoxy-poly-(ethylenoxy)ethanolen mit Alkylgruppen,
die etwa 7 bis 18 Kohlenstoffatome enthalten, und mit 4 bis 100
Ethylenoxy-Einheiten, wie Octylphenoxy-poly(ethylenoxy)ethanole,
Nonylphenoxy-poly(ethylenoxy)ethanole und Dodecylphenoxy-poly(ethylenoxy)ethanole.
Zu Beispielen von nichtionischen oberflächenaktiven Mitteln gehören Polyoxyalkylen-Derivate
des Anhydrids von Hexitol (einschließlich Sorbitane, Sorbide, Mannitane
und Mannide), Partialester von langkettigen Fettsäuren, wie
Polyoxyalkylen-Derivate von Sorbitanmonolaurat, Sorbitanmonopalmitat,
Sorbitanmonostearat, Sorbitantristearat, Sorbitanmonooleat und Sorbitantrioleat.
-
Zu
geeigneten anionischen Emulgatoren gehören die einwertigen Salze aus
Sulfaten der vorstehend genannten nichtionischen Emulgatoren, Mono-
oder Dinatriumsalze von Halbestern oder Diestern von Sulfosuccinaten,
Natriumsalze von Alkylbenzolsulfonaten. Es kann ein einziger Emulgator
verwendet werden oder die Emulgatoren können in Kombination verwendet
werden. Wenn Kombinationen von Emulgatoren verwendet werden, ist
es vorteilhaft, einen relativ hydrophoben Emulgator in Kombination
mit einem relativ hydrophilen Mittel zu verwenden. Ein relativ hydrophobes
Mittel ist eins mit einem Trübungspunkt
in einer 1 %igen wäßrigen Lösung von
weniger als 190°F
(88°C),
und ein relativ hydrophiles Mittel ist eins mit einem Trübungspunkt in
einer 1 %igen wäßrigen Lösung von
190°F (88°C) oder darüber. Der
Konzentrationsbereich der Gesamtmenge der Emulgatoren beträgt vorteilhafterweise
0,5 bis 5 %, bezogen auf die wäßrige Phase
des Latex, unabhängig
vom Feststoffgehalt. Die Packung der oberflächenaktiven Mittel wird typischerweise
in einer Menge von 2 bis 7 Gew.-% der Emulsionen verwendet.
-
Es
kann ein alkalischer Puffer irgendeines herkömmlichen Typs, der mit dem
Stabilisator kompatibel ist, verwendet werden, wenn es erwünscht ist,
den pH-Wert des Systems bei einem erwünschten Wert zu halten. Die
Menge des Puffers beträgt
im allgemeinen etwa 0,1 bis 5 Gew.-%, auf die Monomere bezogen.
-
Die
folgenden Beispiele sollen Ausführungsformen
der Erfindung erläutern
und deren Umfang nicht einschränken.
-
Beispiel 1
-
Acrylhaftklebemittel mit
20 % Polystyrol gelöst
und dann emulgiert
-
Polymerisationsverfahren
-
Die
Emulsionspolymerisation eines Haftklebemittels erfolgte auf herkömmliche
Art und Weise. Insbesondere wurde ein 1 gallon Reaktor mit Stickstoff
gespült,
und dann wurde eine "erste
Charge" zugesetzt,
die einen Teil der beim Haftklebemittel verwendeten Monomere einschließt. Der
Inhalt wurde auf 80°C
erwärmt. Die
Polymerisation der Monomere in der ersten Charge erfolgte durch
den Zusatz einer 2,73 %igen Natriumpersulfatlösung (1,75 ml) innerhalb von
10 Minuten mit einer Rate von 0,175 g/min.
-
Das
polymerisierbare Emulsionsgemisch wurde erzeugt, indem die "Haftklebemittelformulierung" in einem Mischer
mit einer starken Scherung mit dem "Emulgator" gemischt wurde. Nach der Einleitung
wurden der Initiator, das polymerisierbare Emulsionsgemisch und
der Puffer innerhalb eines Zeitraums von etwa 4 Stunden zugesetzt.
Nach der Zugabe des Initiators und des polymerisierbaren Emulsionsge mischs
wurde die Reaktion weitere 15 Minuten bei 80°C gehalten. Der Reaktionsinhalt
wurde auf 75°C
abgekühlt,
und es wurden 2 ml 1 %iges Eisen zugesetzt. Um die Reaktion zu beenden,
wurden Redox-Verzögerer zugesetzt,
zuerst wurden jeweils 4 ml zugesetzt, und die Reaktion wurde 30
Minuten belassen. Dieses Verfahren wurde je nach Erfordernis wiederholt,
bis das freie Monomer auf weniger als 0,1 % verringert worden war. Erste
Charge
Komponente | Menge
(g) |
1.
deionisiertes Wasser | 44,3 |
2.
Natriumpyrophosphat, 3 % | 42,3 |
3.
Emulgator K30 (29,9 %) | 0,317 |
4.
Aerosol A 102 (32 %) | 2,45 |
5.
2-Ethylhexylacrylat | 28,05 |
6.
Acrylsäure | 0,15 |
7.
Styrol | 0,68 |
8.
Methylmethacrylat | 2,8 |
- K30 ist ein Natriumalkansulfonat
- Aerosol A 102 ist ein Dinatrium-ethoxylierter Alkohol-Halbester
von Sulfosuccinsäure
Haftklebemittelformulierung Emulgator - nv
- = nichtflüchtige Bestandteiles
Initiator 1.
deionisiertes Wasser | 91
g |
2.
Natriumpersulfat | 9
g |
Summe | 100
g |
Puffer 1.
deionisiertes Wasser | 38,36
g |
2.
Natriumcitrat | 11,64
g |
Summe | 50
g |
Redox-Verzögerer 1.
deionisiertes Wasser | 62,61
g |
2.
t-BHP (70 %) | 1,08
g |
1.
deionisiertes Wasser | 62,42
g |
2.
SFS | 0,61
g |
-
Es
wurden 2 ml einer 1 %igen Eisen(III)-sulfat-Lösung verwendet. t-BHP ist tert.-Butylhydroperoxid und
SFS ist Natriumformaldehydsulfoxylat.
-
Abschließende Eigenschaften
des Haftklebemittels
-
Beispiel 2
-
Haftklebemittelformulierung
in Gegenwart eines Polystyrol-Impflatex
polymerisiert
-
Polymerisationsverfahren
-
Dem
Polymerisationsverfahren von Beispiel 1 wurde gefolgt. Allgemein
ausgedrückt
wurde es mit folgenden Schritten ergänzt:
- 1.
Der Reaktor wurde mit Stickstoff gespült.
- 2. Erste Stufe: die erste Charge, die im wesentlichen aus Styrol
als Monomer bestand, wurde zugesetzt und auf 78°C erwärmt. Zugesetzter Initiator
(9 %ige Lösung
von Natriumpersulfat) 4,4 g. Die Exotherme wurde abgewartet. In
dieser ersten Stufe wurde ein Polystyrol-Impflatex erzeugt.
- 3. Nach der ersten Stufe und der Erzeugung des Polystyrol-Impflatex
wurden der Initiator (3,6 %), der Puffer und das polymerisierbare
Emulsionsgemisch innerhalb von etwa 4 Stunden zugesetzt.
- 4. Nach der Zugabe des polymerisierbaren Emulsionsgemischs wurde
das Reaktionsprodukt für
eine weitere Stunde bei 90°C
erwärmt.
- 5. Nach Abschluß der
Reaktion wurde das freie Monomer geprüft. Das Reaktionsprodukt wurde
auf 75°C abgekühlt und
mit Redox-Verzögerern nachbehandelt,
um das freie Monomer auf weniger als 0,1 % zu verringern.
Erste
Charge: Erzeugung eines Polystyrol-Impflatex - Versene 220 ist Ethylendiamintetraessigsäure
- Genopol 1879 ist ein verzweigtes Alkylethoxylat
Haftklebemittelformulierung enthält
auch 0,16 g Dodecylmercaptan (DDM) 220 ppm Emulgator - Disponil FES 32 ist ein Natriumsalz eines
Fettalkoholpolyglycolethersulfats
Initiator 1.
deionisiertes Wasser | 96,4
g |
2.
Natriumpersulfat | 3,6
g |
Summe | 100
g |
Puffer 1.
deionisiertes Wasser | 46,12
g |
2.
Natriumcitrat | 14,0
g |
Summe | 62,12
g |
Redox-Verzögerer 1.
deionisiertes Wasser | 33,9
g |
2.
t-BHP (70 %) | 1,08
g |
1.
deionisiertes Wasser | 34,39
g |
2.
SFS | 0,61
g |
3.
Lösung
von Eisen (Eisen(III)-sulfat); 2 ml einer 1 %igen Lösung; in
das erste eingemischt. | |
-
Abschließende Eigenschaften
des Haftklebemittels
-
Beispiel 3
-
Auswertung der Haftklebemittel
-
Die
Emulsionen der Beispiele 1 und 2 wurden verwendet, um verschiedene
Testproben herzustellen, und mit Emulsionsgemischen verglichen,
die aus einem Haftklebemittellatex mit der Formulierung von Beispiel 1
oder Beispiel 2 (nur Haftklebemittelformulierung) und einem Polystyrollatex
bestanden. Die Latexproben wurden bei einem pH = 7 eingestellt.
Die Emulsionen wurden mit einem Beschichtungsgewicht von 25 g/m
2 direkt auf 2 ml Mylar aufgebracht. Die
entstandenen Bänder
wurden auf verschiedene Substrate aufgebracht, z.B. rostfreier Stahl
(SS) und Polyethylen niedriger Dichte (LDPE), und es wurde die Ablösefestigkeit
ausgewertet. Bei einigen der Proben wurde die Scherung auf der Basis
eines Tests ausgewertet, bei dem ein 1/2 inch Folienquadrat einem
Gewicht von 500 g ausgesetzt wurde (als 1/2 × 1/2 × 500 bezeichnet), und einem
anderen, bei dem ein 1 inch Quadrat einem Gewicht mit 1000 g ausgesetzt
und ausgewertet wurde (als 1 × 1 × 1000 bezeichnet).
Ein anderer Test war die gemessene Ablösung entsprechend dem bei 35°F (2°C) oder 20°F (–7°C) mit Wellpappe
durchgeführte
Test; als 35 CC bzw. 20 CC bezeichnet. (Die Herstellung der Proben
und die angewendeten Testverfahren für die Auswertung der Klebemittel
oder Beschichtungen in den Beispielen basierten auf Standardtests
der Industrie. Sie sind in Veröffentlichungen
des Pressure Sensitive Tape Council (PSTC), Glenview, Illinois beschrieben.)
Die Ergebnisse sind in Tabellen 1 bis 5 aufgeführt. Tabelle
1
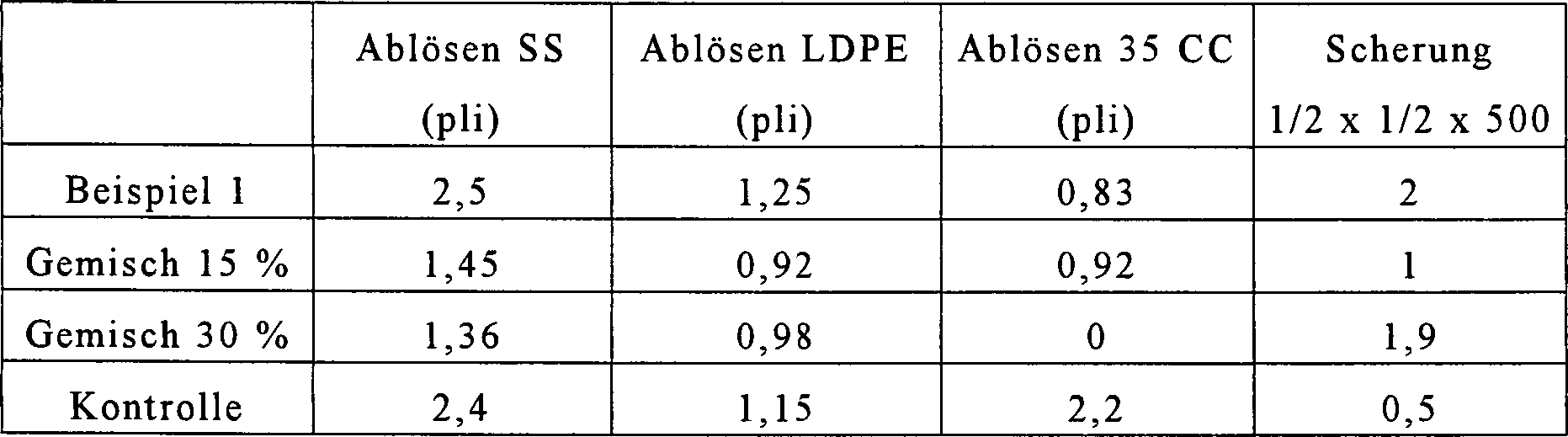
- pli
- = pounds per linear
inch
-
Die
Tabelle 1 vergleicht den Hybridverbundlatex von Beispiel 1 mit dem
Verfahren des Latexmischens, d.h. des Mischens eines Polystyrollatex
mit einer Haftklebemittel-Kontrolle (gleiche Monomerzusammensetzung
wie bei der Haftklebemittelformulierung von Beispiel 1 aufgeführt). Die
Haftklebemittelformulierung allein wurde als "Kon trolle" bezeichnet, und es wurden Gemische
mit 15 und 30 Gew.-% Polystyrol verglichen. Wie aus Tabelle 1 ersichtlich
ist, behält
das Polystyrol, entweder als Verbundstoff oder Gemisch und obwohl
als Füllstoff
gedacht, die Leistungseigenschaften für ein Haftklebemittel der Haftklebemittel-Kontrolle
bei. Das PSA von Beispiel 1 braucht den Vergleich mit der Kontrolle
im jedem Bereich nicht zu scheuen, abgesehen vom Ablösen bei
geringer Temperatur, d.h. 35 CC. Es ist dem Ablösen bei 35 CC für das 15
%ige Gemisch im wesentlichen gleich und deutlich besser als die
mit 30 % gemischte Probe.
-
Wen
Styrol in einer Menge von 20 % in das Haftklebemittel copolymerisiert
wurde, würde
das den Tg-Wert um etwa 20°C
erhöhen.
Es wäre
wie eine Erhöhung
des Tg-Wertes des PSA von –60
auf –40°C. Dieses
Ergebnis würde
die Klebrigkeit einer Schlaufe und möglicherweise andere Eigenschaften
des Haftklebemittels nachteilig beeinflussen.
-
Tabelle
2 zeigt die Ergebnisse der Verwendung von drei Polystyrolquellen.
Die Proben A, B und C wurden entsprechend Beispiel 1 hergestellt.
Die Probe A verwendete ein handelsübliches Polystyrol mit hohem Molekulargewicht,
die Probe B verwendete ein handelsübliches Polystyrol mit geringem
Molekulargewicht, und die Probe C verwendete im Monomer gelöste Getränkebecher
aus Polystyrol. Tabelle
2
-
Alle
Proben ergaben Leistungseigenschaften, die sich sehr ähnlich waren,
womit deutlich wird, daß die Leistungseigenschaften
durch die unterschiedlichen verwendeten Polystyrolpolymere nicht
stark beeinflußt wurden.
-
Tabelle
3 vergleicht die Ergebnisse des Hybridverbundstoffs von Beispiel
1, der Polystyrol einschließt, einer
Kontrolle aus PSA allein und des Verbundstoffs von Beispiel 1 mit
einem klebrigmachenden Mittel. Tabelle
3
-
Wie
erwartet verbesserte die Zugabe eines klebrigmachenden Harzes die
Ablösewerte
des Hybridverbundstoffs von Beispiel 1 bei einem geringen Einfluß auf die
Scherung.
-
Zusammenfassend
zeigen diese Ergebnisse, daß das
Verfahren zum Einführen
eines styrolhaltigen Polymers, z.B. eines Polystyrolfüllstoffs,
in eine Haftklebemittelformulierung, wodurch ein Hybridverbundlatex erzeugt
wird, für
PSA-Zwecke geeignet ist. Die Leistung wird nicht nachteilig beeinflußt, und
die Kosten werden verringert.
-
Beim
bevorzugten Herstellungsverfahren, d.h. dem Polymerisieren der Haftklebemittelformulierung
in Gegenwart eines Polystyrol-Impflatex, hat der Polymerfüllstoff
insgesamt einen positiven Einfluß auf die Leistungseigenschaften
und die Kosten. Die Leistungsergebnisse für den Latex, der in Beispiel
2 hergestellt wurde, im Vergleich mit einer PSA- Kontrolle und einem Gemisch aus PSA
mit Polystyrollatex sind in Tabelle 4 aufgeführt. Tabelle
4
-
Das
bevorzugte Beispiel zeigt eine gewisse Differenzierung gegenüber dem
Latexgemisch und ist der PSA-Kontrolle ähnlicher. Wie in Tabelle 3
verbessert der Zusatz eines klebrigmachenden Harzes zum Gemisch mit
20 % das Ablösen
auf LDPE und Wellpappe, Tabelle 5. Tatsächlich braucht die Leistung
des Latex von Beispiel 2 den Vergleich sowohl mit dem klebriggemachten
Gemisch als auch dem klebriggemachten handelsüblichen Allzweckklebemittel
für Etiketten
nicht zu scheuen, Tabelle 5. Tabelle
5