The specific embodiment
Be surprised to find, making the polishing layer that is used for chemical mechanical polishing pads, join the simultaneously movement of the position of this nozzle opening of die cavity at curable material, with respect to (wherein the position of nozzle opening is along the central shaft C of die cavity by same technique
AxisOnly mobile in one direction) polishing layer made can reduce the density defective that occurs significantly in polishing layer, by the curable material of nozzle opening along and around the central shaft C of die cavity
AxisBe added in the die cavity in three directions.
Also find to use the polishing layer of the method preparation of the present invention technique identical with use (different is, CP between whole charge period, the position of nozzle opening is along the central shaft C of die cavity
AxisOnly move (namely, when curable material gathers die cavity, keeping the position of nozzle opening to be higher than the upper face of curable materials) in a direction and before the cake section cutting blade be used stone mill rather than belt mill) polishing layer of making compares the polished surface of the surface roughness with reduction.Find also cake is cut into that the cutting edge of cutting blade almost becomes small bending and wavy behind the multilayer chemical mechanical polishing layer.It is believed that prior art makes the method for holystone cutting edge cause removing material from the wavelike segments of cutting edge and forms flat polishing plane, but with the cost that is changed to along the tensile property of the cutting edge of the length of cutting blade; Cause cutting performance inconsistent and use the surface roughness of the polishing layer of this manufacturing to increase.Be surprised to find the wavelike segments that belt polishing cutting edge is easy to planarization and fine grinding cutting edge, the length along cutting blade keeps more consistent cutting edge simultaneously; Cause the surface roughness that has reduced significantly the chemical mechanical polishing layer that uses the method manufacturing.It is believed that in subsequently use and comprise that the surface roughness of the polished surface of reduction is easy to improve the polishing defect performance in the process of chemical mechanical polishing pads of this polishing layer.
As herein and the term " surface roughness " that in additional claim, uses relate to the roughness of the polished surface that uses the polishing layer that profilometer determines, for example, the Zeiss Surfcom profilometer that uses following parameter to arrange: measure type-Gaussian; Tilt-collimation; Slant correction-least square; Measure length-0.6 inch (15.24mm); Cutoff wavelength-0.1 inch (2.54mm); Measuring speed-0.24 inch/s (6.1mm/s); And cut-off filtering rate-300.
As herein and the term that in additional claim, uses " between charge period or CP " relate to the time (in second) that curable material is added to the whole time period of die cavity, from initial curable material enter into begin in the die cavity to enter in the die cavity constantly to last curable materials till.
As herein and the term " feed rate or CR " that in additional claim, uses relate to mass flowrate (kg/ second), the curable material of CP between charge period (in second) joins in the die cavity with this mass flowrate.
As herein and the term " starting stage starting point or the SP that in additional claim, use
IP" nozzle opening position when relating to starting stage initial of feed time section, it is consistent during with feed time section initial.
As herein and the term " starting stage end point or the EP that in additional claim, use
IP" nozzle opening position when relating to the end of starting stage of feed time section, it is just before the feed time section of transition stage begins.
As herein and the term " starting stage path " that in additional claim, uses relate to from starting stage starting point SP
IPEnd point EP to the starting stage
IPStarting stage of reinforced process in the motion path (if any motion is arranged) of nozzle opening position.
As herein and the term " transition stage starting point or the SP that in additional claim, use
TP" nozzle opening position when relating to transition stage initial of feed time section.Transition stage starting point SP
TPEnd point EP with the starting stage
IPIn identical position.
As herein and the term " transition stage transition point or the TP that in additional claim, use
TP" relate to the position of nozzle opening in the transition stage process of feed time section, at this moment between the moving direction of section inner nozzle aperture position with respect to the central shaft C of die cavity
AxisChange (the namely direction of motion on x and y size).
As herein and the term " transition stage end point or the EP that in additional claim, use
TP" relate to the primary importance of nozzle opening in the annular section of die cavity, at the direction of motion of this nozzle opening position, position central shaft C with respect to die cavity
AxisChange.The end point EP of transition stage
TP, also be the position of the transition stage of the feed time section nozzle opening when finishing, it is just before feed time section Remaining Stages.
As herein and the term " transition stage path " that in additional claim, uses relate to from transition stage starting point or SP
TPTo transition stage end point EP
TPThe transition stage process of feed time section in the path of taking, nozzle opening position.
As herein and the term " Remaining Stages starting point or the SP that in additional claim, use
RP" relate to the Remaining Stages of the feed time section nozzle opening position when initial.Remaining Stages starting point SP
RPEnd point EP with transition stage
TPIn identical position.
As herein and the term " Remaining Stages transition point or the TP that in additional claim, use
RP" relate to the position of nozzle opening in feed time section Remaining Stages process, at the moving direction of this nozzle opening position central shaft C with respect to die cavity
AxisChange.
As herein and the term " Remaining Stages end point or the EP that in additional claim, use
RP" nozzle opening position when the Remaining Stages that relates to the feed time section finishes, its end point with the feed time section is identical.
As herein and the term " Remaining Stages path " that in additional claim, uses relate to from Remaining Stages starting point or SP
RPTo Remaining Stages end point EP
RPThe Remaining Stages process of feed time section in the path of taking, nozzle opening position.
As herein and the term that in additional claim, uses " polyurethanes) (poly (urethane)) " comprise that (a) is by (i) isocyanates and (ii) polyurethanes that makes of polyalcohol (comprising glycol) reaction; And (b) by (i) isocyanates and (ii) polyalcohol (comprising glycol) and (iii) polyurethanes that makes of the mixture reaction of water, amine or water and amine.
As herein and the term that in additional claim, uses " basic tight " relate to lining, the expression lining comprises≤space of 5% volume.
As herein and the term " substantially constant " that in additional claim, uses relate to the feed rate of curable materials in reinforced process, mean that two following expression formulas all will satisfy:
CR
max≤(1.1*CR
avg)
CR
min≥(0.9*CR
avg)
CR wherein
MaxIt is the biggest quality flow rate that curable materials joins die cavity in feed time section process (kg/ second); CR
MinIt is the minimum mass flow rate that curable materials joins die cavity in feed time section process (kg/ second); CR
AvgThat whole feed time section joins the gross weight (kg) of the curable materials of die cavity divided by the length (second) of feed time section.
As herein and the term " gelling time " that in additional claim, uses relate to curable materials, total hardening time of the mixture that expression is measured according to ASTMD3795-00a standard method of test (2006 audit) (measuring the standard method of test of thermal fluidity, curing and the behavior property of pourable thermosets by torque rheometer).
As herein and the term " almost circular cross section " that in additional claim, uses relate to die cavity (20), mean the central shaft C from die cavity
AxisProject to the greatest radius r of the die cavity (20) of x-y plane (30) to the vertical inner boundary (18) of surrounding wall (15)
CThan the central shaft C from die cavity (20)
AxisProject to the short radius r of the die cavity (20) of x-y plane (30) to the vertical inner boundary (18) of surrounding wall (15)
CLong≤20%.(seeing Fig. 2).
As herein and the term " die cavity " that in additional claim, uses relate to volume corresponding to vertical inner boundary (18) restriction of the horizontal inner boundary (14) of the top surface (6,12) of lining (4) and surrounding wall (15).(seeing Fig. 1-3).
As herein and the term that in additional claim, uses " substantially (substantially) perpendicular to " relate to First Characteristic (horizontal inner boundary for example; Vertical inner boundary) with respect to Second Characteristic (for example axle, x-y plane), the angle of expression First Characteristic and Second Characteristic is at 80 °-100 °.
As herein and the term that in additional claim, uses " basic (essentially) perpendicular to " relate to First Characteristic (horizontal inner boundary for example; Vertical inner boundary) with respect to Second Characteristic (for example axle, x-y plane), the angle of expression First Characteristic and Second Characteristic is at 85 °-95 °.
As herein and the zone that relates in the polishing layer of the term " density defective " that in additional claim, uses have the filling concentration of obvious reduction with respect to the remaining area of polishing layer.The density defective with the naked eye is observable when polishing layer is placed on the optical table (light table), and wherein the zone of density defective is compared with other zone of polishing layer and had the higher transparency.
As herein and the term " nozzle opening radius or the r that in additional claim, use
NO" relate to nozzle opening, but the minimum ring SC radius r of expression complete closed nozzle opening
SCR namely
NO=r
SCIn order to describe effect, see Fig. 8 A-8B.Fig. 8 A is that nozzle opening (62a) is had radius r fully
SCThe plane of minimum ring SC (63a) sealing (64a); Wherein nozzle opening is annular.Fig. 8 B is that nozzle opening (62b) is had radius r fully
SCThe plane of minimum ring SC (63b) sealing (64b); Wherein nozzle opening is other than ring type.Preferably, r
NO5-13mm.R more preferably
No8-10mm.
The method that is used to form the polishing layer of chemical mechanical polishing pads of the present invention is used the mould (1) that has mould matrix (2) and be connected to the surrounding wall (8) on the mould matrix (2); Wherein have top surface (6), lower surface (3) and average thickness (5), t
L, lining (4) be used adhesive (7) and be connected on the mould matrix (2), adhesive is arranged between the lower surface (3) and mould matrix (2) of lining (4).(seeing Fig. 1).
When its reaction forms the cake that solidifies, the lining (4) that method of the present invention is used is easy to and curable match materials, wherein curable material be bonded to lining (4) with enough intensity thus the cake that solidifies in slicing processes is not peeled off from lining.Preferably, the lining (4) of method use of the present invention is periodically removed and is changed from mould matrix (2).The lining (4) that method of the present invention is used can be when solidifying and any types of material of its combination for curable material.Preferably, lining (4) is the polyurethanes polymeric material.More preferably, the lining of use (4) is by the prepolymer reaction product of toluene di-isocyanate(TDI) and poly-fourth diether glycol (polytetramethylene ether glycol) and the polymer of aromatic diamines curing agent (curative) reaction generation.Preferred, the aromatic diamines curing agent is selected from 4,4 '-methylene-two-o-chloraniline and 4,4 '-methylene-two-(3-chloro-2,6-diethyl aniline).Preferably, prepolymer reaction product has the unreacted NCO concentration of 6.5 to 15.0 weight percentages.The prepolymer that has the unreacted NCO concentration of 6.5 to 15.0wt% content on the market comprises, for example: made by AirProducts an Chemical
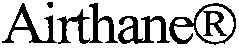
Prepolymer PET-70D, PHP-70D, PET-75D, PHP-75D, PPT-75D and PHP-80D; And made by Chemtura
Prepolymer LFG740D, LF700D, LF750D, LF751D, LF753D and L325.Preferably, this curing agent and prepolymer reaction product are with NH in unreacted NCO and the curing agent in prepolymer
2The stoichiometric proportion of (perhaps OH) is 90-125% (more preferably, 97-125 percentage; More preferably, 100-120%) combination.This stoichiometry or can be directly by this stoichiometric raw material is provided, perhaps being exposed to wittingly or by accident the reaction of moisture middle ground by NCO and water provides.The lining that uses (4) can be as porous or non-porous.Preferably, the lining of use (4) is non-porous substantially.
The lining (4) that method of the present invention is used preferably has 2 to 10cm average thickness (5) t
L(more preferably 2 to 5cm) uses granite base comparator (for example Chicago digital indicator Cat#6066-10) at a plurality of random points that cross lining (4) (for example 〉=10 point).(seeing Fig. 1).
The adhesive (7) that the inventive method is used can be any adhesive that is suitable for lining (4) is connected to mould matrix (2).For example, the adhesive of use (7) is optional from contact adhesive, hotmelt, contact adhesive (contact adhesive) and their combination.Preferably, the adhesive of use (7) (a) is bonded to mould matrix (2) with enough intensity with lining (4) and breaks away from from mould matrix (2) to prevent lining in the cake sectioning (4); And (b) mould matrix (2) is not had physical damage or leave over hazard residue (namely damage mould matrix (2) and the lining replaced between functional combination residual) situation under remove from mould matrix (2).Preferably, adhesive (7) is contact adhesive.
Mould matrix (2) of the present invention can be any suitable rigid material, and it will support to be added into the weight of the curable materials in the die cavity; To be easy to be used for shifting loading mould cavity between reinforced, as to solidify (for example large stove) and the cutting curing cake equipment; Can bear the temperature change of respective process and not have bending.Preferably, the mould matrix (2) of use is stainless steel (more particularly 316 stainless steels).
The top surface (12) of the lining that uses in the methods of the invention limits the horizontal inner boundary (14) of die cavity (20).(seeing Fig. 2-3).Preferably, the horizontal inner boundary (14) of die cavity (20) is flat.More preferably, the horizontal inner boundary (14) of die cavity (20) is flat and substantially perpendicular to the central shaft C of die cavity
AxisMore preferably, the horizontal inner boundary (14) of die cavity (20) is flat and is basically perpendicular to the central shaft C of die cavity
Axis
The surrounding wall (15) of the die cavity that uses in the inventive method (10) limits the vertical inner boundary (18) of die cavity (20).(seeing Fig. 2-3).Preferably, surrounding wall limits the vertical inner boundary (18) of die cavity (20), and it is substantially perpendicular to x-y plane (30).More preferably, surrounding wall limits the vertical inner boundary (18) of die cavity (20), and it is basically perpendicular to x-y plane (30).
Die cavity (20) has central shaft C
Axis(22), it is consistent with Z axis and crossing with the horizontal inner boundary (14) of die cavity (20) at central point (21).Preferably, central point (21) is positioned at the cross section C that die cavity (20) projects to x-y plane (30)
X-sectGeometric center.(seeing Fig. 2-4).
Die cavity projects to the cross section C on x-y plane
X-sectCan be any rule or irregular two-dimensional shape.Preferably, the cross section C of die cavity
X-sectBe selected from polygon or ellipse.More preferably, the cross section C of die cavity
X-sectTo have mean radius r
C(preferably, the r wherein of circular cross section substantially
C20-100cm; More preferably, r
C25-65cm; Most preferably, r
C40-60cm).Most preferably, die cavity is approximately and has the circular cross section of being substantially C
X-sectStraight (right) cylindrical shaped region; Wherein die cavity has symmetry axis C
X-sym, the central shaft C of itself and die cavity
AxisUnanimously; The right cylindrical shaped region is as giving a definition:
C
x-area=πr
C 2,
R wherein
CThe transverse cross-sectional area C of die cavity
X-areaProject to the mean radius on the x-y plane; r
C20-100cm (more preferably, r
C25-65cm; Most preferably, r
C40-60cm).
Die cavity (20) has looping pit zone (40) and annular region (50).(seeing Fig. 3-4).
Preferably, the looping pit of die cavity (20) zone (40) is the right cylindrical shaped region in die cavity (20), and it is projected as circular cross section DH in x-y plane (30)
X-sect(44) and have a symmetry axis DH in looping pit zone
Axis(42); Axle DH
Axis(42) with the central shaft C of die cavity
AxisConsistent with Z axis.(seeing Fig. 3-4).The circular cross-sectional area DH in looping pit zone (40)
X-sect(44) has transverse cross-sectional area DH
X-area, as give a definition:
DH
x-area=πr
DH 2,
R wherein
DHThe circular cross section DH in looping pit zone
X-sect(44) radius (46).Preferably, r
DH〉=r
NO(more preferably, r
DH5 to 25mm; Most preferably, r
DH8 to 15mm).
Preferably, the annular region (50) of die cavity (20) is the shaped region of the annular (toroid) in die cavity (20), and it is projection circular cross-section D on the x-y plane
X-sect(54) and have an annular region symmetry axis D
Axis(52); D
AxisCentral shaft C with die cavity
AxisConsistent with Z axis.(seeing Fig. 3-4).The circular cross-sectional area D of annular region (50)
X-sect(54) has circular cross-sectional region D
X-area, as give a definition:
D
x-area=πR
D 2-πr
D 2,
R wherein
DThe circular cross section D of annular region
X-sectLarge radius (56); r
DThe circular cross section D of annular region
X-sectLittle radius (58); R wherein
D〉=r
DHR
D>r
DR
D<r
CPreferably, r
D〉=r
DHAnd r
D5-25mm.More preferably, r
D〉=r
DHAnd r
D8-15mm.Preferably, r
D〉=r
DHR
D>r
DR
D<(K*r
C), wherein K is that (more preferably, K is 0.014-0.1 to 0.01-0.2; Most preferably, K is 0.04-0.086).More preferably, r
D〉=r
DHR
D>r
DR
D20-100mm (more preferably, R
D20-80mm; Most preferably, R
D25-50mm).
The length C P of feed time (in second) can change significantly.For example, the length C P of feed time depends on the size of die cavity, average feed rate CR
AvgCharacteristic (such as gel time) with curable materials.Preferably, feed time CP is 60-900 second (more preferably is 60-600 second, be most preferably 120-360 second).Typically, feed time CP is subject to the restriction of the gel time of curable materials.Preferably, feed time CP is less than or equal to the gel time of the curable materials that is added into die cavity.More preferably, feed time CP is less than the gel time of curable material.
Feed rate CR (kg/ second) can be at whole feed time CP process change.For example, feed rate CR can be intermittent.Namely, but feed rate CR one or many in whole feed time section process temporarily drops to zero.Preferably, joined in the die cavity with the cardinal principle constant rate of speed at the curable material of whole feed time section.More preferably, the material curable at whole feed time section CP joined in the die cavity with substantial constant speed, average feed rate CR
AvgIt is (0.015 to 1kg/ second more preferably 0.015 to 2kg/ second; 0.08 to 0.4kg/ second most preferably).
Reinforced stage CP is divided into three independent stages: starting stage, transition stage and Remaining Stages.The beginning correspondence of starting stage the beginning of reinforced stage CP.The end of starting stage is just before the beginning of transition stage.The end of transition stage is just before Remaining Stages begins.The end correspondence of Remaining Stages the end of reinforced stage CP.
Nozzle moves or is out of shape (as flexible) in the process of reinforced stage CP, thereby the position of nozzle opening is all removable in three directions.Nozzle (60) is mobile or distortion (as flexible) in the process of reinforced stage CP, thereby the position of nozzle opening (62) is along the central shaft C of die cavity (120) in reinforced process CP
Axis(122) mobile with respect to the horizontal inner boundary (112) of die cavity (120), the position of maintenance nozzle opening (62) is more than the upper surface (72) of curable materials (70) with when curable material (70) converges to die cavity (20) in the time.(seeing Fig. 5 A-5B).Preferably, in reinforced process CP the position of nozzle opening (62) along the central shaft C of die cavity (120)
Axis(122) mobile with respect to the horizontal inner boundary (112) of die cavity (120), the height of position more than the upper surface (72) of curable materials (70) of maintenance nozzle opening (62) with when curable material (70) converges to die cavity (120) in the time.(seeing Fig. 5 B).In the position of feed time section nozzle opening along the central shaft C of die cavity
AxisIn its motion, temporarily stop (namely in the axial motion of z).Preferably, the position of nozzle opening in its motion with respect to the central shaft C of die cavity
AxisAt each transition stage transition point TP
TP(if any) and Remaining Stages transition point TP
RP(namely in the temporary transient stop motion in the position of Z-direction nozzle opening) suspends.
Be positioned at the annular section (namely continuing for the starting stage) of die cavity in the position of the whole starting stage inner nozzle opening of feed time section.Can keep static in the position of whole starting stage nozzle opening, the starting point SP of starting stage
IPEnd point EP with the starting stage
IP(be SP in identical position
IP=EP
IP).Preferably, work as SP
IP=EP
IPThe time, the starting stage is>0 to 90 second time is long (more preferably>0 long to 60 second time; Most preferably 5 to 30 second time is long).More preferably, the position that the upper surface that begins material curable to the die cavity from starting stage of feed time section begins to rise to the moment nozzle opening that transition stage begins keeps static; The starting point SP of starting stage
IP(80) and the end point EP of starting stage
IP(81a) (the starting point SP of itself and transition stage
TP(82a) consistent) along the central shaft C of die cavity
Axis(222) same position in annular region (140).Preferably, looping pit zone (140) is straight round cylinder; The symmetry axis DH of looping pit
Axis(142) with the central shaft C of die cavity
Axis(222) and the z axle overlap.(seeing Fig. 6 A-6C).Position-movable at the starting stage nozzle opening, wherein the starting point SP of starting stage
IPEnd point EP with the starting stage
IPDifference (is SP
IP≠ EP
IP).Preferably, work as SP
IP≠ EP
IPThe time, the starting stage is>0 long to (CP-10.02) second time; Wherein CP is the feed time section in second.More preferably, work as SP
IP≠ EP
IPThe time; Starting stage is>0 long to (CP-30) second time; Wherein CP is the feed time section in second.More preferably, in the process of the feed time section of starting stage when the upper surface of the curable material in the die cavity (220) rises, from the starting point SP of starting stage
IP(80) to the end point EP of starting stage
IP(81b) (the starting point SP of itself and transition stage
TP(82b) unanimously) the location optimization ground of nozzle opening is along the central shaft C of die cavity
Axis(222) mobile in looping pit zone (140), with the position of maintenance nozzle opening when whole starting stage of feed time section is in curable material is aggregated to die cavity (220) height at the upper surface that is higher than curable material.(seeing Fig. 6 A-6C).
The position of nozzle opening moves to point in the annular region from the point in the looping pit zone of die cavity in the transition stage process of feed time section.Preferably, transition stage is that (more preferably, 0.2 to 5 second time is long for 0.02 to 30 second time length; Most preferably, 0.6 to 2 second time is long).Preferably, in the transition stage process position of nozzle opening with respect to the central shaft C of die cavity
AxisMove (preferably 15 to 35mm/ seconds, most preferably 20 to 30mm/ seconds) for 10 to 70mm/ seconds with average speed.Preferably, the position of nozzle opening is at its central shaft C with respect to die cavity
AxisMotion at each transition stage transition point TP
TP(if any) and Remaining Stages end point EP
TPThe temporary transient stop motion in position of x and y direction nozzle opening (namely) suspends.Preferably, in the transition stage process from transition stage starting point SP
TP, through any transition stage transition point TP
TPTo transition stage end point EP
TP, the position of nozzle opening is with respect to the central shaft C of die cavity
AxisWith constant speed movement.Preferably, in the process of transition stage the position of nozzle opening from transition stage starting point SP
TP, through a plurality of transition stage transition point TP
TPMove to transition stage end point EP
TPThe transition stage path proximity that wherein projects to the x-y plane is curve (more preferably the transition stage path proximity is spiral transition curve).Most preferably, in the transition stage process position of nozzle opening directly from transition stage starting point SP
TPMove to transition stage end point EP
TPThe transition stage path that projects to the x-y plane is straight line.
Fig. 6 A-6C has described to have central shaft C
Axis, with symmetry axis DH
AxisThe looping pit zone (140) of right cylindrical shape (142); With symmetry axis D
AxisThree different transition stage paths in the die cavity (220) of the annular region (150) of anchor ring shape (152); The central shaft C of die cavity wherein
Axis, the looping pit zone symmetry axis DH
Axis(142) and the symmetry axis D of annular region
Axis(152) each is consistent with the z axle.The First Transition stage path of describing in Fig. 6 A-6C is at the looping pit zone of die cavity (220) (140) inherent transition stage starting point SP
TP(82a) beginning also directly is extended to the interior transition stage end point EP of annular region (150) of die cavity (220)
TP(89); Transition stage path (83a) is projected as straight line (84) in x-y plane (130).The second transition stage path of describing in Fig. 6 A-6C is at the looping pit zone of die cavity (220) (140) inherent transition stage starting point SP
TP(82b) beginning also directly is extended to the interior transition stage end point EP of annular region (150) of die cavity (220)
TP(89); Transition stage path (83b) is projected as straight line (84) in x-y plane (130).The 3rd transition stage path of describing in Fig. 6 A-6C is at the looping pit zone of die cavity (220) (140) inherent transition stage starting point SP
TP(82a) beginning; By the transition point TP of transition stage in looping pit zone (140)
TP(88) transition; Then directly be extended to the transition stage end point EP that is positioned at annular region (150)
TP(89); Transition stage path (85) is projected as a pair of interconnective straight line (87) in x-y plane (130).That note is the end point EP of transition stage
TP(89) corresponding to the starting point SP of Remaining Stages
RP(90) (being that they are in identical position).
The position of nozzle opening is positioned at annular region (namely for the part of feed time section Remaining Stages, the looping pit zone may be passed or be positioned in the position of nozzle opening) in the process of the Remaining Stages of feed time section.Preferably, be positioned at annular region (the namely duration of Remaining Stages) in the position of the whole Remaining Stages nozzle opening of feed time section.Preferably, the Remaining Stages 〉=10 second time is long.More preferably, Remaining Stages be 10 to<(CP-0.2) second time long; Wherein CP is the feed time section in second.Still more preferably, Remaining Stages be 30 to<(CP-0.2) second time long; Wherein CP is the feed time section in second.Most preferably, Remaining Stages be 0.66*CP to<(CP-0.2) second time long; Wherein CP is the feed time section in second.Preferably, in the Remaining Stages process position of nozzle opening with respect to the central shaft C of die cavity
AxisMove (more preferably 15 to 35mm/ seconds, most preferably 20 to 30mm/ seconds) for 10 to 70mm/ seconds with average speed.Preferably, the position of nozzle opening is at its central shaft C with respect to die cavity
AxisMotion at each Remaining Stages transition point TP
RPThe temporarily stop motion of position of x and y direction nozzle opening (namely) suspends.Preferably, in the Remaining Stages process from Remaining Stages starting point SP
RP, through each Remaining Stages transition point TP
RPThe position of nozzle opening is with respect to the central shaft C of die cavity
AxisWith constant speed movement.Preferably, in the process of Remaining Stages the position of nozzle opening from Remaining Stages starting point SP
RPMotion is through a plurality of Remaining Stages transition point TP
RPThe Remaining Stages path that wherein projects to the x-y plane is a series of continuous lines.Preferably, Remaining Stages transition point TP
RPAll be positioned at the annular region of die cavity.Preferably, project to a series of connecting lines on the x-y plane by the Remaining Stages path and be approximately central shaft C with die cavity
AxisCircle or two-dimensional helical line that distance changes.Preferably, a series of connecting lines that projected on the x-y plane by the Remaining Stages path are approximately two-dimensional helical, continuous Remaining Stages transition point TP wherein
RPWith with the central shaft C of die cavity
AxisThe distance that increases or reduce projects on the x-y plane.More preferably, these a series of connecting lines that projected on the x-y plane by the Remaining Stages path are approximately circular, wherein continuous Remaining Stages transition point TP
RPWith with the central shaft C of die cavity
AxisThe distance that equates projects on the x-y plane and these a series of connecting lines that projected on the x-y plane by the Remaining Stages path are regular polygon (namely equilateral and isogonisms).Preferably, wherein regular polygon has 〉=(limit more preferably 〉=8,5 limits; Limit most preferably 〉=10; Limit preferably≤100; Limit more preferably≤50; Limit most preferably≤20).Most preferably, the Remaining Stages path proximity is helix.Namely, in the Remaining Stages process, the position of nozzle opening is along the central shaft C of die cavity
AxisMove continuously to remain on more than the height of the upper face that gathers the curable materials in the die cavity, (preferably, regular polygon has 5 to 100 limits for the path of regular polygon on the x-y plane along projecting in the position of while nozzle opening; More preferably, 5 to 50 limits; Again more preferably, 8 to 25 limits; Most preferably, 8 to 15 limits).
Fig. 7 A-7C has described a part of preferred Remaining Stages path (95), and it has central shaft C
Axis(222), with symmetry axis DH
AxisThe looping pit of right cylindrical shape (142) zone (140) and with symmetry axis D
AxisBe approximately helix (helix) in the die cavity (220) of the annular region (150) of anchor ring shape (152); The central shaft C of die cavity wherein
Axis, the looping pit zone symmetry axis DH
Axis(142) and the symmetry axis D of annular region
Axis(152) each is consistent with the z axle.Remaining Stages path (95) is at the inherent Remaining Stages starting point of annular region (150) SP of die cavity (220)
RP(90) beginning and continuity are by a plurality of Remaining Stages transition point TP in the annular region (150) of die cavity (220)
RP(92); All Remaining Stages transition point TP
RPCentral shaft C with die cavity
Axis(222) distance equates; And Remaining Stages path (95) project on the x-y plane (130) is the straight line (97) of ten sections equal lengths, forms decahedra (100).That note is Remaining Stages starting point SP
RP(90) corresponding to transition stage end point EP
TP(89) (namely they are in identical position).
Curable material comprises liquid prepolymer.Preferably, curable material comprises liquid prepolymer and many microcomponents (microelement), and many microcomponents are evenly dispersed in the liquid prepolymer.
Preferably polymerization of liquid prepolymer (namely solidifying) is selected from polyurethanes with formation, polysulfones, polyether sulfone, nylon, polyethers, polyester, polystyrene, acrylate copolymer, polyureas, polyamide, polyvinyl chloride, polyvinyl fluoride, polyethylene, polypropylene, polybutadiene, polymine, polyacrylonitrile, PEO, polyolefin, polyacrylic acid (alkyl) ester, polymethylacrylic acid (alkyl) ester, polyamide, PEI, polyketone, epoxy resin, silicones, by ethene, propylene, the polymer that diene monomers forms, protein, the polymer of polysaccharide and aforementioned at least two kinds combination.Preferably, the liquid prepolymer polymerization comprises the material of polyurethane with formation.More preferably, liquid prepolymer polymerization (curing) with form polyurethanes (polyurethane, polyurethane).
Preferably, liquid prepolymer comprises the material that contains polyisocyanates.More preferably, liquid prepolymer comprises the product of polyisocyanates (for example vulcabond) and material containing hydroxy groups.
Preferably, polyurethanes is selected from di-2-ethylhexylphosphine oxide 4,4 '-cyclohexyl isocyanate, cyclohexyl diisocyanate, IPDI, hexamethylene diisocyanate, propylidene-1, the 2-vulcabond, tetramethylene-1, the 4-vulcabond, 1, the own diisocyanate of 6-, dodecane-1, the 12-vulcabond, cyclobutane-1, the 3-vulcabond, cyclohexane-1, the 3-vulcabond, cyclohexane-1, the 4-vulcabond, 1-isocyano-3,3,5-trimethyl-5-isocyano hexahydrotoluene, methyl cyclohexane support vulcabond, the triisocyanate of hexamethylene diisocyanate, 2,4,4 trimethyls-1, the triisocyanate of 6-hexane diisocyanate, the uretdione of hexamethylene diisocyanate (urtdione), the second vulcabond, 2,2,4-trimethyl hexamethylene diisocyanate, 2,4,4-tri-methyl hexamethylene-vulcabond, dicyclohexyl methyl hydride diisocyanate and their composition.Most preferably, polyisocyanates is aliphatic and has and be less than 14% unreacted NCO.
Preferably, the material of the hydroxyl of the present invention's use is polyalcohol.Exemplary polyalcohol comprises PPG for example, hydroxy-end capped polybutadiene (comprising part and complete all hydrogenated spin-off), PEPA, polycaprolactone polyol, polycarbonate polyol and their mixture.
Preferably, polyalcohol comprises PPG.The example of PPG comprises that polytetramethylene ether diol (PTMEG), polyethylene propane diols (polyethylene propylene glycol), polyoxy are for propane diols and their mixture.Hydrocarbon chain has saturated or unsaturated key, and replace or unsubstituted fragrance and cyclic group.Preferably, polyalcohol of the present invention comprises PTMEG.The polyester polyol that is fit to includes but not limited to polyethylene glycol adipate glycol (polyethylene adipate glycol), polybutylene glyool adipate, poly-adipate glycol-propylene glycol ester glycol, phthalic acid-1,6-hexylene glycol, poly-(adipic acid hexylene glycol ester) glycol and their mixture.Hydrocarbon chain has saturated or unsaturated key, or replace or unsubstituted fragrance and cyclic group.The polycaprolactone polyol that is fit to includes but not limited to 1, the polycaprolactone that initial polycaprolactone, the PTMEG of initial polycaprolactone, the BDO of initial polycaprolactone, the neopentyl glycol of initial polycaprolactone, the trimethylolpropane of initial (initiated) polycaprolactone, the diethylene glycol (DEG) of 6-hexylene glycol is initial and their mixture.Hydrocarbon chain has saturated or unsaturated key, or replace or unsubstituted fragrance and cyclic group.Suitable Merlon includes but not limited to poly terephthalic acid carbonic ester and poly-(carbonic acid hexylene glycol) glycol.
Preferably, multiple microcomponent is selected from and is detained bubble, hollow polymer material (namely microballoon), liquid hollow polymer material, water-soluble material (for example cyclodextrin) and the insoluble phase material (for example mineral oil) of filling.Preferably, multiple microcomponent is microballoon, for example, polyvinyl alcohol, pectin, polyvinylpyrrolidone, hydroxyethylcellulose, methylcellulose, hydroxypropyl methylcellulose, carboxymethyl cellulose, L-HPC, polyacrylic acid, polyacrylamide, polyethylene glycol, polyhydroxy ethers Acrylite (polyhydroxyetheracrylite), starch, maleic acid, PEO, polyurethane, cyclodextrin and their combination (for example from Sweden Akzo Nobel of Sundsvall Expancel).For example, microballoon can be with the chemical method modification to pass through for example branching, protection (block) and crosslinked change solubility, swelling and other performance.Preferably, microballoon has the median diameter less than 150 μ m, and more preferably median diameter is less than 50 μ m.Most preferably, the median diameter that has of microballoon (48) is less than 15 μ m.Note, the median diameter of microballoon can be changed and the mixture of different size or different microballoon (48) can be used.The prepreerence material of microballoon is that the copolymer of acrylonitrile and vinylidene chloride is (for example, from Akzo Nobel's
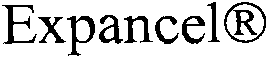
).
Liquid prepolymer further comprises curing agent alternatively.Preferably curing agent comprises Diamines.Suitable poly-diamines (polydiamine) comprises the primary and secondary Diamines.Preferably poly-diamines includes but not limited to diethyl toluene diamine (DETDA), 3,5-dimethyl disulfide generation-2,4-toluenediamine and its isomer, 3,5-diethyl Toluene-2,4-diisocyanate, 4 diamines and isomer thereof (for example 3,5-diethyl Toluene-2,4-diisocyanate, 6-diamines); 4,4 '-two (Zhong Ding is amino)-diphenyl methanes, 1,4-pair-(sec-butyl is amino)-benzene, 4.4 '-methylene-two (2-chloroanilines), 4,4 '-methylene-two-(3-chloro-2, the 6-diethylaniline) (MCDEA), polybutylene oxide-two-p-aminobenzoic acid ester, N, N '-dialkyl group diaminodiphenyl-methane, p, p '-methylene dianiline (MDA) (MDA), m-phenylene diamine (MPD) (MPDA); Methylene-two-2-chloroaniline (MBOCA); 4,4 '-methylene-two-(2 chloroaniline) (MOCA), 4,4 '-methylene-two-(2, the 6-diethylaniline) (MDEA), 4,4 '-methylene-two-(2,3 dichloroaniline) (MDCA), 4,4 '-diaminourea-3,3 ' diethyl-5,5 '-dimethyl diphenylmethane, 2,2 ', 3,3 '-tetrachloro diaminodiphenyl-methane, two p-aminobenzoic acid propylene glycol esters, and their mixture.Preferably, diamine curing agent is selected from 3,5-diaminourea sulfo--2,4-toluenediamine and isomer thereof.
Curing agent also can comprise glycol, trihydroxylic alcohol, tetrahydroxylic alcohol and hydroxy-end capped curing agent.Suitable glycol, trihydroxylic alcohol, tetrahydroxylic alcohol group comprise ethylene glycol, diethylene glycol (DEG), polyethylene glycol, propane diols, polypropylene glycol, low-molecular-weight polytetramethylene ether diol, 1, two (2-hydroxyl-oxethyl) benzene, 1 of 3-, 3-pair-[2-(2-hydroxyl-oxethyl) ethyoxyl] benzene, 1,3-pair-2-[2-(2-hydroxyl-oxethyl) ethyoxyl] and ethyoxyl } benzene, 1,4-butanediol, 1,5-pentanediol, 1,6-hexylene glycol, resorcinol-two-(beta-hydroxyethyl) ether, hydroquinones-two-(beta-hydroxyethyl) ether and their mixture.Preferably hydroxy-end capped curing agent comprises 1, two (2-hydroxyl-oxethyl) benzene, 1 of 3-, 3-is two-[2-(2-hydroxyl-oxethyl) ethyoxyl] benzene, 1, and 3-is two-{ 2-[2-(2-hydroxyl-oxethyl) ethyoxyl] ethyoxyl } benzene, BDO, and their mixture.Hydroxy-end capped and diamine curing agent can comprise one or more saturated, unsaturated, aromatic and cyclic groups.In addition, hydroxy-end capped and diamine curing agent can comprise one or more halogen groups.
Preferably, (that different is CP between whole charge period, and the position of nozzle opening is along the central shaft C of die cavity with the use same process to use the cake of method of the present invention preparation
AxisOnly moving (namely, when curable material gathers die cavity, keeping the position of nozzle opening to be higher than the upper face of curable materials) in a direction) cake made compares the density defective that contains still less.More preferably, use in the cake that method of the present invention makes, in the polishing layer of each cake at least 50% or more (more preferably at least 75% or more, most preferably at least 100% or more) without the density defective.Again preferably, to have mean radius be r to die cavity
CBe substantially circular cross section; R wherein
C40 to 60cm; Use method of the present invention preparation cake (different is that the position of CP nozzle opening between whole charge period is along the central shaft C of die cavity from using same process
AxisOnly moving in a direction) cake made compares, and increased by 2 times (more preferably increasing by 3 times) without the quantity of the polishing layer of density defective.
In the method for the invention, use the cutting blade with cutting edge that the cake section of solidifying is the polishing layer of a plurality of expectation thickness.Preferably, the polishing compound is applied to the cutting edge of cutting blade, and band is used to the fine grinding cutting edge before the cutting cake is a plurality of polishing layers.The polishing compound that this method is used preferably includes the alumina abrasive that is dispersed in the aliphatic acid.More preferably, the polishing compound that uses in the method for the present invention comprises the alumina abrasive that is dispersed in the 70-82wt% in 18 to 35wt% the aliphatic acid.The sanding belt of using in the method for the present invention is preferably the leather sanding belt.Most preferably, the sanding belt of using in the method for the present invention for the leather sanding belt of turning tool (for example, is preferably
Turning tool).
Alternatively, in the method for the invention, in order to be easy to sectioning, the cake of curing is heated.Preferably, the cake that solidifies in the sectioning process is used the heat lamp heating, and the cake that solidifies in sectioning is cut into slices is a plurality of polishing layers.
Preferably, (that different is CP between whole charge period, and the position of nozzle opening is along the central shaft C of die cavity with the use same process to use the polishing layer of method of the present invention preparation
AxisOnly move (namely in a direction, when curable material gathers die cavity, keep the position of nozzle opening to be higher than the upper face of curable materials), and cutting blade uses the polishing of polishing stone and does not use sanding belt before section) polishing layer made compares the surface roughness that polished surface has decline.More preferably, use the surface roughness of the polishing layer of method manufacturing of the present invention to have at least 10% reduction (more preferably at least 20%; Most preferably at least 25%).