Solution
High-quality maintenance that can prevent chiller shutdown and reduce energy loss
Centrifugal chillers are playing the key role for process and air-conditioning in the area of mainly commercial use, industrial use and District Heating and Cooling. Mitsubishi Heavy Industries Thermal Systems (MHI Thermal Systems) provides both time-based maintenance and condition-based maintenance for supporting energy loss reduction, energy-saving and stable operations with avoiding chiller shutdowns. We analyze operating data to accurately understand the condition of the chillers and provides the customers with necessary information for their decision-making, whether a certain maintenance is needed and when it should be conducted.
FEATURES
Periodic inspection and maintenance based on MHI Thermal System’ expertise
MHI Thermal Systems has extensive and long history with various types of chillers including centrifugal chillers for more than 50 years. More than 10,000 units have been delivered in the world. During such long period, we have acquired a broad range of maintenance expertise in Japan and worldwide, including statutory inspections. Based on this accumulated expertise, we can offer to the customer professional maintenance plans that deliver energy-saving, stable operations and reducing operating costs. On-site periodic inspections ascertain the operating condition of the chillers by gathering and analyzing data. Periodic maintenance, like overhauls, is planned for preventing failure. In addition to maintenance, swift action is taken when caution or failure are detected.
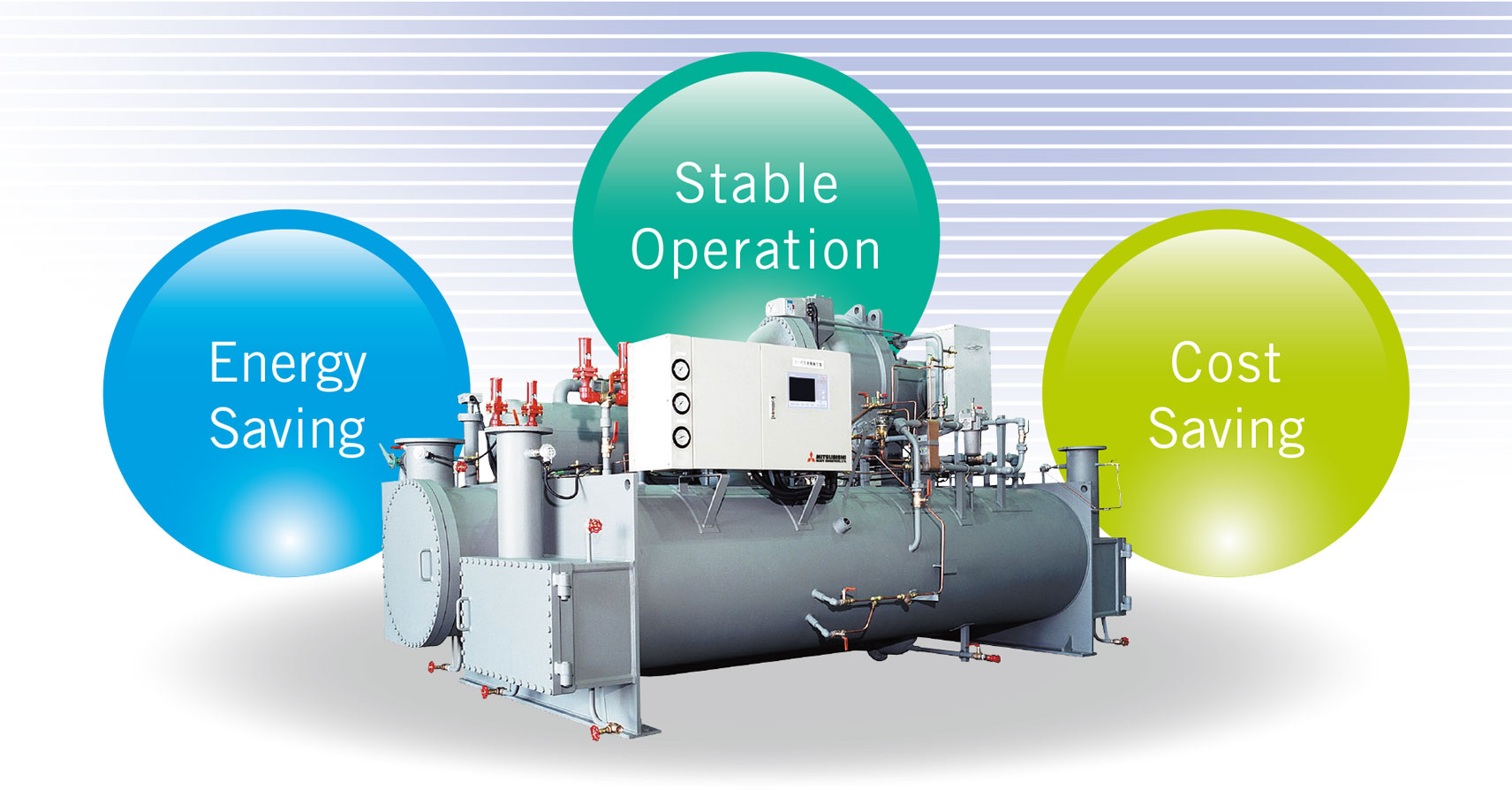
High-quality maintenance that reduces energy loss
The condition of a chiller varies according to factors such as its usage status and the environment where it has been installed. In addition to time-based maintenance, it is also essential to conduct condition-based maintenance for which timelines cannot be predetermined. With understanding the condition of the chiller and its operating status, we can propose appropriate maintenance program which could eventually result in saving energy. The chiller cooling system can be simply illustrated. In the evaporator tubes, water is cooled by evaporation heat. Evaporated refrigerant is compressed and discharged into the condenser. Refrigerant, which has become highly heated and pressurized is cooled by water in the condenser. It is condensed and liquefied. The high-pressure refrigerant is depressurized by the expansion valve and returns to the evaporator. The refrigerant circulates and chilled water is supplied continuously as shown below.

Δh shows the motor input without fouling of condenser tubes. Δh’ shows the motor input with fouling of condenser tubes.
Providing information for making decisions on whether and when maintenance is needed
The 24-hour, year-round monitoring systems based on our acquired various types of data that make it possible to accurately understand the condition of the chillers. Proposals for maintenance currently needed are presented together with evidence. For example, tube cleaning is proposed with an evaluation of tube fouling and energy loss by using historical temperature data of main heat exchangers, liquid terminal temperature difference (LTD). The proper maintenance can thus be performed at the right time according to the customer’s business circumstances. Our recommended maintenance items are shown in the table below. In addition to periodical standard maintenance items, we closely communicate and share information with customers through periodical inspections for the necessity of tube cleaning, eddy current testing (ECT), overhaul of compressor unit, and electrical equipment etc. Further, we plan to launch the customer portal service for visualizing and sharing the condition of chillers at real time. With the said our extended services, we will work for the health of customers assets and for their satisfaction as a partner.

EXPERIENCES
MHI Thermal Systems serves customers in 26 countries.