Jeklo
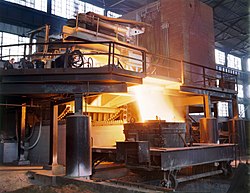
Jêklo je železova zlitina, pri kateri je poleg samega železa najpomembnejši zlitinski element ogljik. Ogljika je v jeklih razmeroma malo, lahko pa so dodani še drugi legirni elementi. Njegov masni delež je navadno manjši od 2 %. Kljub temu ima najpomembnejši vpliv na uporabne lastnosti jekel.
Najpogostejša so ogljikova jekla. To so jekla, ki poleg železa vsebujejo le ogljik ter manjše količine mangana, silicija in aluminija. Slednje tri elemente dodamo z namenom, da bi zmanjšali ali povsem izničili negativen vpliv nečistoč, kot so žveplo, fosfor, kisik in dušik. Druga skupina jekel so legirana jekla. Ta – za razliko od ogljikovih jekel - vsebujejo še znatne količine kroma, niklja, molibdena ali katerega drugega elementa. Posebna legirana jekla, ki so znana kot nerjavna, vsebujejo najmanj 11,5 % kroma. Orodna jekla so posebna vrsta jekel. Namenjena so odrezovanju in oblikovanju kovinskih in nekovinskih materialov v želeno obliko. Nekatera jekla dobijo svojo končno obliko z litjem (jeklena litina), medtem ko večino jekel oblikujemo v končno obliko z gnetenjem (preoblikovanjem) in jih lahko prištevamo h gnetnim zlitinam.
Značilnosti jekla
[uredi | uredi kodo]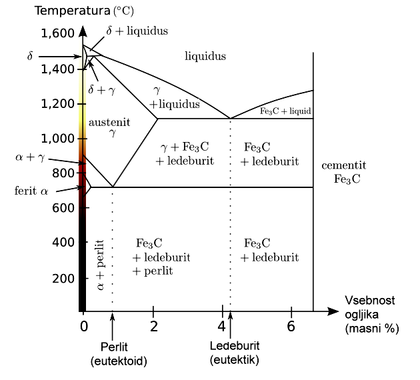
Železo je pogosto najti v zemeljski skorji v obliki rude, navadno železovega oksida, kot sta na primer magnetit in hematit. Železo se pridobiva iz rude tako, da se s pomočjo ogljika iz rude odstranjuje kisik, ki se sprošča v atmosfero kot ogljikov dioksid. Ta proces, znan kot taljenje, je bil prvič uporabljen za kovine z nižjimi tališči, kot sta na primer kositer, ki se tali pri približno 250 °C (482 °F) in baker (tališče pri približno 1.100 °C (2.010 °F)). Za primerjavo, lito železo se tali pri približno 1.375 °C (2.507 °F) [1] V antičnih časih so topili majhne količine železa s segrevanjem rude v trdnem stanju, zakopane v goreče oglje; pridobljene grude železa so s kladivom obdelovali, da iz njih iztisnejo nečistoče. Če se pri tem previdno premika rudo po ognjišču, je mogoče obvladati vsebnost ogljika.
Vse te temperature je mogoče doseči s starimi pristopi, ki jih je človeštvo poznalo že od bronaste dobe dalje. Ker se stopnja oksidacije železa nad 800 ° C (1,470 ° F) hitro poveča, je pomembno, da taljenje poteka v okolju z nizko vsebnostjo kisika. Za razliko od bakra in kositra se ogljik v tekočem ali trdnem železu dokaj hitro raztopi. Taljenje v prisotnosti ogljika, ki reducira železove okside, vodi do nastanka t. i. grodlja, to je zlitine, ki vsebuje preveč ogljika, da bi jo lahko imenovali jeklo.[1] Presežek ogljika in drugih nečistoč se odstrani v naslednjem koraku.
Za proizvodnjo jekla z želenimi lastnostmi se mešanici železa / ogljika pogosto dodajo drugi materiali. Nikelj in mangan povečujeta natezno trdnost jekla v jeklu in austenitno obliko raztopine železo-ogljik stabilizirata, krom poveča trdoto in talilno temperaturo, vanadij tudi poveča trdoto, ne da bi jeklo bilo zaradi tega bolj dovzetno za kovinsko utrujenost.[2]
V proizvodnji nerjavečega jekla se talini doda vsaj 11 % kroma, tako da se na površini kovine stvori trd oksid, ki preprečuje korozijo. Volfram ovira nastanek cementita, tako da se med počasnejšim hlajenjem raje tvori martenzit, kar je ozadje za proizvodnjo hitroreznih jekel. Po drugi strani elementi, kot so žveplo, dušik in fosfor, povzročajo krhkost jekla, tako da je treba te običajno prisotne elemente med obdelavo iz taline jekla odstraniti.[2]
Tudi v ozkem območju koncentracij mešanic ogljika in železa, ki nosijo ime jeklo, to je do 2,1 masnih odstotkov C, lahko pride do nastanka več različnih metalurških struktur, ki imajo zelo različne lastnosti.Razumevanje teh lastnosti je bistvenega pomena za kakovost jekla. Pri sobni temperaturi je najbolj stabilna oblika čistega železa ferit ali α-železo, ki ima telesno centrirano kristalno strukturo ( BCC). To je precej mehka kovina, ki lahko raztopi le malo ogljika, ne več kot 0,005 pri 0 °C in 0,021 masnih odstotkov ogljika pri 723 °C. Pri 910 °C se čisto železo pretvori v ploskovno centrirano kubično (FCC)
Med ohlajanjem jekel z manj kot 0,8% ogljika (znanih kot podeutektoidna jekla), se avstenitna faza (FCC) v zmesi skuša pretvoriti nazaj v feritno fazo (BCC). Ogljik se več ne prilega strukturi FCC, ki ima za posledico prebitek ogljika. Eden od možnosti za izločevanje ogljika iz avstenitne kletke je, da se obori iz raztopine kot cementit, pri tem pa v svoji okolici tvori na ogljiku siromašen ferit ( fazo železa BCC železa), kar se kaže kot feritno ozadje s cementitnimi vključki. Cementit je trda in krhka intermetalna spojina s kemično formulo Fe3C. Eutektoidna točka, z 0,8% ogljika, se ohlajena kaže kot t. i. perlit, ki je dobil ime zaradi svojega bisernega videza. Pri večjih povečavah je mogoče razločiti lamelno strukturo ferita in cementita. Pri jeklih z več kot 0,8% ogljika, ima ohlajena snov strukturo v obliki perlita in cementita.[3]
Morda najpomembnejša polimorfna oblika jekla je martenzit, metastabilna faza, ki je bistveno močnejša od drugih faz jekla. Če se jeklo v austenitni fazi hitro kali, nastane martenzit: atomi, ki nimajo dovolj časa za tvorjenje cementita, "zamrznejo" na točkah, kjer se celična struktura iz FCC spremeni v deformirano obliko BCC. Glede na vsebnost ogljika obstajajo različne oblike martenzitne faze. Pod približno 0,2% ogljika ima BCC kristalno obliko ferita, pri višjih vsebnostih ogljika pa zavzame tetragonalno telesno centrirano strukturo (BCT) . Za preoblikovanje austenita v martenzit ni potrebna toplotna aktivacijska energija. Poleg tega spremembe v sestavi ni, tako da atomi praviloma ohranjajo svoje sosede[4]
Martenzit ima nižjo gostoto kot pa austenit, tako da pretvorba med njima povzroča spremembo prostornine, pri transformaciji iz austenita v martenzit orej pride do ekspanzije. Notranje napetosti se na splošno čutijo kot stiskanje kristalov martenzita in napetosti na preostali ferit. Na obe sestavini pri tem delujejo občutne strižne sile. sestavin. Če se kaljenje izvaja nestrokovno, lahko notranje napetosti povzročijo, da se del, ki se hladi, zdrobi. V vsakem primeru pride do porasta notranje trdosti in drugih mikroskopskih nepravilnosti. Če se jeklo kali z vodo, pogosto pride do razpok, ki pa lahko da niso vedno vidne..[5]
Zgodovina
[uredi | uredi kodo]Načrtovana in nenaključna proizvodnja jekla poteka iz predhodno pridobljenega železa. Ker je jeklo zlitina železa in ogljika, pri zgodovini jekla dejansko obravnavamo železo. Danes večino železa pretvorijo v jeklo.
Železa, za razliko od nekaterih drugih kovin kot so zlato, srebro in platina, v naravi ne najdemo v elementarni obliki, ampak navadno v kombinaciji s kisikom in žveplom. Z obdelavo iz železove rude odstranimo kisik in dodamo ogljik ali druge elemente za izboljšanje lastnosti materiala.
Težavo pri pridobivanju železa v preteklosti je predstavljalo predvsem visoko tališče železa, pri katerem je možno iz rude izločiti kisik. Tališča, ki znaša 1535 °C, ni bilo možno doseči z odprtim ognjem, ki je lahko dosegel temperaturo do največ 1100 °C. Človek je poznal železovo rudo, vendar je ni znal obdelovati.
Do 20. stol. pr. n. št.
[uredi | uredi kodo]Najstarejše najdbe, ki kažejo prve znake uporabe železa, izhajajo iz starega Egipta in Mezopotamije in datirajo okoli 4000 let pr. n. št. Egipčani in Sumerci so v tem času iz železa izdelovali nakit, konice sulic in bodala. Železo, ki so ga obdelovali, vsebuje več kot 6 % niklja, tako kot snov meteoritov, kar nakazuje, da je izvor tega železa nezemeljski oz. iz meteoritov. Nikelj-železo je bilo primerno za obdelavo, ne da bi ga bilo treba predhodno segreti do temperature tališča čistega žleza.
Prve najdbe železnih predmetov, ki ne vsebujejo niklja in so zemeljskega izvora, so iz obdobja med 3000 in 2000 let pr. n. št. ter izhajajo iz Anatolije (danes Turčije), Egipta in Mezopotamije. Manjše kepe železa so našli v talilnicah bakra, kar podpira teorijo, da je bilo to železo stranski produkt proizvodnje bakra.
Z vpihovanjem zraka skozi votle cevi, so v pečeh dosegali višje temperature ognja (do 1200 °C), hkrati pa se je temperatura tališča železove rude, z dodajanjem ogljika v obliki oglja, znižala. Tako so iz železove rude dobili grude stopljenega železa ali t. i. železov cvet. Ne glede na to ali so železov cvet dobili kot stranski produkt ali z načrtno proizvodnjo, so v tem obdobju železovo rudo že lahko obdelovali. Ogret železov cvet so nadalje obdelovali s kladivom, da so se znebili neželenih primesi.
Od 20. stol. pr. n. št. do 14. stol. n. št.
[uredi | uredi kodo]Dosedanja odkritja damascenskega (s kovanjem vzorčasto okrašenega) jekla iz 20. stol. pr. n. št. izhajajo iz območja nekdanje Anatolije. Civilizaciji Hetitov iz Anatolije pripisujejo najstarejšo proizvodnjo jekla. Železo so mehanično ločili od ostalih snovi v železovi rudi in kovali vroče železo pri 800 °C, s čimer so dodatno izločili nečistoče v obliki tekoče žlindre. Tako so dobili kovano železo. Hetiti so iz jekla izdelovali orožje ali pa ga uporabljali kot menjalno sredstvo za srebro z Asirci.
Egipčani so svoje železne premete vrednotili zadosti, da so jih pokopavali v grobnice. Egipčanski vladar Tutankamon, ki je umrl leta 1323 pr. n. št. je bil pokopan z železnim bodalom.
Starim Grkom in Rimljanom je bil proces pridelave jekla tako zanimiv, da so ga opisovali celo pisatelji. Homerjeve pesnitve (okoli 880 pr. n. št.), Herodotova »Zgodovina« (446 pr. n. št.), Aristotel (350 pr. n. št.) in Plinijeva »Zgodovina narave« (leta 77) opisujejo procese pridelave jekla. Grki in Rimljani so jeklo uporabljali predvsem za meče. Kljub visoki natezni trdnosti ga niso uporabljali v konstrukcijske namene. Čeprav bi lahko izdelovali dolge traverze, je vse kar najdemo, nekaj majhnih nosilcev v kopališčih iz kovanega železa.
Indijci so za damasciranje uporabljali jeklo imenovano Wootz. To jeklo so pričeli proizvajati okoli 3. stoletja pr. n. št. na jugu Indije in je vsebovalo veliko ogljika. Wootz so dobili tako, da so železovo rudo karbonizirali, da so jo lahko stalili, zatem pa še dekarbonizirali, do stopnje vsebovanega ogljika od 1 % do 1,6 %. Jeklo so nato v obliki materiala in končnih izdelkov izvažali v Evropo, Kitajsko, Arabski svet in Bližnji vzhod, kljub temu pa je postopek izdelave zelo kvalitetnega jekla Wootz ostal skrivnost vse do prenehanja njegove proizvodnje v 17. stoletju.
Kitajci, ki so železo in jeklo pričeli uporabljati približno 1000 let kasneje kot Hetiti, so močno razširili uporabo te kovine. Uporabljali so jo za orodje, orožje, posodo, kuhinjske pripomočke in tudi v konstrukcijske namene. Prvi železni viseči most so konstruirali in izvedli Kitajci. Njihovo prečiščevanje staljenega surovega železa in kovaško obdelovanje, je bilo okoli 500 pr. n. št. zelo razvito, saj so enako tehnologijo Evropejci pričeli uporabljati šele 2000 let kasneje.
Od 15 stol. n. št. do 19 stol. n. št.
[uredi | uredi kodo]V Evropi lito železo do 14. stoletja ni bilo cenjeno. S pričetkom uporabe jekla za topove pa se je zanimanje za železovo rudo povečalo. Pomemben pobudnik razvoja je bila tudi železnica s svojimi potrebami. Železničarji so potrebovali kvalitetnejši material za tirnice, ki so jih sicer morali menjavati vsakih 6 mesecev in so bile vzrok za številne nesreče.
Povečana pridelava jekla je terjala porabo velikih količin oglja, kar je pomenilo ogromno krčenje gozdov, zato je v 17. stol. prišlo do zamenjave oglja s premogom, vendar je premog vseboval žveplo, kar je naredilo jeklo krhko. Rešitev so našli pivovarji, ki jim je pri uporabi premoga za varjenje piva nezaželeno žveplo dajalo smrdljiv priokus pivu. Žvepla so se znebili tako, da so premog pekli, tako da je ostal čisti ogljik. Švedski kemik Torbern Olof Bergman je leta 1781 v svoji znanstveni razpravi Disseratatio Chemica de Analysi Ferri razkril pomembno vlogo ogljika v železni zlitini in determiniral kompozicijo litega železa, jekla in surovega železa. Odslej je bila razlika med železom in jeklom jasno določena.
Britanski izumitelj Henry Bessemer je izumil tehniko masovne proizvodnje jekla in jo leta 1855 patentiral. Bessemer je med projektiranjem topovskih izstrelkov za Britansko vojsko prišel na idejo, da bi iz poceni železne zlitine odstranjevali ogljik, namesto da so ga dodajali dragemu nizko karbonskemu surovemu jeklu. Bessemerjev postopek je zajemal vpihovanje zraka pod velikim pritiskom (s pomočjo parnega stroja) v staljeno surovo železo, kar je imelo dvojni učinek: kisik je nase vezal ogljik in se izločil kot ogljikov dioksid, hkrati pa je oksidacija dobavljala toploto, ki je bila potreba za ohranjanje taline, saj se je z zniževanjem ravni ogljika poviševala talilna temperatura. Odkritje je pomenilo pričetek poceni industrijske proizvodnje jekla.
Nemški inženir Carl Wilhelm Siemens je leta 1856 predstavil izboljšavo talilne peči. Iznašel je regeneracijski postopek, na osnovi katerega je francoski inženir Pierre-Émile Martin leta 1864 konstruiral in patentiral peč. Ta je dobila ime Siemens-Martinova peč. Pri teh pečeh se uporablja postopek regeneracije toplote tako, da se v plamenih peči temperatura bistveno zviša s predogrevanjem zraka in generatorskega plina, ki služi kot gorivo. S konvektorskim postopkom se proizvajajo kisla in bazična jekla glede na vrsto obloge v konvektorjih, kjer se poleg grodlja tali tudi staro železo. Možnost uporabe starega železa pri proizvodnji novega je pomenila pomemben korak naprej v jeklarski industriji.
Angleža Percy Carlyle Gilchrist in Sidney Gilchrist Thomas sta leta 1878 modificirala Bessemerjev proces. Z dodajanjem apnenca ali dolomita sta iz taline odstranila fosfor in žveplo. Možnost odstranjevanja nečistoč je pomenil novo prelomnico, saj sta postali angleška in nemška železova ruda, ki sta vsebovali veliko fosforja, prav tako uporabni za pridelavo kvalitetnega jekla, kot je bila prej švedska ruda. Proces je po izumitelju poimenovan Thomasov proces.
Po številnih poizkusih izumiteljev v 19 stoletju je elektropeči leta 1900 razvil Francoz Paul L.T. Heroult. V elektropečeh se je s pomočjo oglenih elektrod tik nad surovinami ustvaril električni oblok, ki je talil surovine ter zgoreval ogljik. Pri tem postopku ni bilo treba dovajati zraka, zato se v talini niso ustvarjali dodatni zračni mehurčki. Elektroobločni postopek je omogočil izdelavo visokokakovostnih in posebnih vrst jekel, ki so jih uporabljali za orodja in vzmetnice. Osnovna pomanjkljivost električnih peči je visoka količina porabljene energije.
Od 20. stol. n. št. do danes
[uredi | uredi kodo]V začetku 20. stoletja je bila zaradi njegove neenotne kompozicije ukinjena uporaba litega in surovega železa v konstrukcijske namene. V skladu s tedanjimi predpisi je bilo pri gradnji dovoljeno uporabljati le jeklo. Konstrukcijsko jeklo je bilo material specifičnih oblik, zanesljive kemične sestave in točno določene trdote, kar pa je zagotavljalo primerno stopnjo varnosti konstrukcije.
Jeklo je material, ki je prisoten pri vsej arhitekturi 20. stoletja: v ploščah, vezivih, vijakih, žebljih, v obliki palic in mrež kot armatura v betonu. Konstrukcijsko jeklo je omogočilo razvoj hitro postavljivih poslovnih objektov, strehe velikih razponov brez vmesnih nosilcev in gradnjo nebotičnikov.
Pomemben napredek v jeklarski industriji je bilo odkritje nerjavečega jekla. Anglež Harry Brearley ga je prvič proizvedel z dodajanjem kroma železu v električni peči leta 1913. Po njegovem odhodu iz laboratorijev Brown Firth je z raziskavami nadaljeval dr. William H. Hatfield, ki je leta 1924 izumil še danes najbolj razširjeno vrsto nerjavečega jekla, t. i. jeklo »18/8«, katerega 18 % teže predstavlja krom in 8 % teže je niklja.
Danes se večina konstrukcijskega jekla proizvaja s procesom imenovanim osnovni oksidacijski postopek (BOS – ang. Basic oxygen steelmaking), ki je izboljšana metoda Bessemerjevega procesa v t. i. LD–konverterju, ki je poimenovan po dveh Avstrijskih krajih – Linz in Donawitz. Postopek je razvilo in prvič predstavilo Avstrijsko podjetje Voestalpine AG leta 1952. Z vpihovanjem čistega kisika na surovo železo se temperatura dvigne do 1700 °C, zniža se raven ogljika in pridobivamo nizko karbonsko jeklo. Bistvena izboljšava od Bessemerjevega postopka je uporaba kisika namesto zraka, ki skupaj z modernim prečiščevalnim procesom zagotavlja dobro zrnavost in dobro varljiv material z enakomerno trdnostjo in žilavostjo.
Leta 1952 je bila ustanovljena Evropska skupnost za premog in jeklo, z namenom zagotoviti rekonstrukcijo ključnih industrij po drugi svetovni vojni. Proces je bil za obe panogi zelo zahteven, vendar se je le tako oblikovala vitka, fit in moderna jeklarska industrija. Jeklo je postalo moderen material z obetajočo prihodnostjo. Danes je jeklo najpogosteje recikliran material na svetu. Ocenjujemo, da je od novo proizvedenega jekla približno 42,3 % recikliranega materiala. Vse jeklo, ki je na razpolago se reciklira. Dolga življenjska doba in uporaba v konstrukcijske namene pomeni zaloge za recikliranje v prihodnosti, toda da bi zapolnili današnje potrebe je treba proizvajati tudi jeklo iz železove rude.
Sistematika jekel
[uredi | uredi kodo]Jeklo je elastično, modul elastičnosti E znaša od 2,0 do 2,2×105 N/mm². Čisto železo ima trdoto le 60 HV. S postopki toplotne obdelave dosegamo v jeklu trdote tudi do 800 HV, s postopki toplotno kemične obdelave pa tudi vrednosti 2000 HV. Natezna trdnost čistega železa znaša približno 200 N/mm², jekla pa tudi do 4000 N/mm².
Tehnična železa, med katere spada jeklo, so med kovinami oziroma zlitinami po uporabnosti najbolj razširjena. Gospodarska in tehnična uporabnost ni le v veliki količini, temveč tudi v izredno visoki uporabnosti lastnosti. Lastnosti jekel spreminjamo predvsem z legiranjem, s plastičnim preoblikovanjem v toplem in hladnem ter s toplotno obdelavo. Tako je mogoče natezno trdnost spreminjati od 200 do 4000 N/mm2, magnetne lastnosti pa od feromagnetnih do paramagnetnih. Korozijsko obstojnost lahko prilagajamo najrazličnejšim zahtevam, prav tako tudi tehnološke lastnosti. Jeklo lahko oblikujemo v vročem z ulivanjem, kovanjem, valjanjem in stiskanjem; v hladnem pa z valjanjem, vlečenjem, stiskanjem in z odrezovanjem. Jekla lahko izdelujemo tudi s postopki prašne metalurgije. Jeklene dele lahko spajamo z varjenjem, lotanjem, kovičenjem, vijačenjem.
Kaljeno jeklo
Kaljênje je postopek toplotne obdelave jekel, pri katerem jeklo najprej segrejemo do kalilne temperature (v področje avstenita), nato pa ga hitro ohladimo. Na ta način dobimo trdo strukturo - martenzit. Ogljikovo jeklo mora vsebovati zadostno količino ogljika (0,6 - 2,06 % ogljika), da je kaljivo. Lastnost jekel, da se jim pri kaljenju poveča trdota, imenujemo kaljivost. Pojem, ki označuje, ali se je predmet pri kaljenju prekalil po vsem prerezu, pa imenujemo prekaljivost. Zaradi hitrega ohlajanja se pri kaljenju pojavijo v materialu velike notranje napetosti; grozi nevarnost, da bi predmet počil. Da to preprečimo, zakaljen predmet popustimo. Popuščanje je postopek, pri katerem zakaljeni predmet segrejemo do 180 °C (ko martenzit še ne izgubi trdote); segrevamo takoj po kaljenju, še preden se predmet popolnoma ohladi do temperature okolice. Glavni namen kaljenje je navadno povečanje trdote jekla.
Razdelitev jekel
[uredi | uredi kodo]glede na kemično sestavo
[uredi | uredi kodo]- nelegirano jeklo
- navadno ogljikovo jeklo
- rafinirano ogljikovo jeklo
- legirano jeklo
- malo legirano jeklo
- visoko legirano jeklo ali močno legirano jeklo
- avstenitno jeklo
- feritno jeklo
glede na vrsto uporabe
[uredi | uredi kodo]- orodno jeklo primeri oznak TC140, 210CrW12
- npr. HSS jeklo primeri oznak HS12-1-5-5
- splošno konstrukcijsko jeklo ali navadno konstrukcijsko jeklo primeri oznak S355J2G3
- konstrukcijsko jeklo za toplotno obdelavo
- posebno konstrukcijsko jeklo
- npr. ventilno jeklo
Neporušitvene preiskave
[uredi | uredi kodo]S temi preiskavami odkrivamo napake v materialu, ne da bi ga poškodovali ali celo uničili in ga kasneje lahko vgradimo v kakšno napravo. Najbolj sta razširjeni dve metodi: preiskava z ultrazvokom in preiskava z rentgenskimi žarki
Največji proizvajalci jekla
[uredi | uredi kodo]Vir: Svetovna jeklarska organizacija (World Steel Association)
Uvrstitev (2014) |
2014[6] | 2013[7] | 2012[8] | 2011[9] | 2010 | 2009 | 2008 | 2007 | Podjetje | Sedež |
---|---|---|---|---|---|---|---|---|---|---|
1 | 98,1 | 96,1 | 93,6 | 97,2 | 98,2 | 77,5 | 103,3 | 116,4 | ArcelorMittal | Luksemburg |
2 | 49,3 | 50,1 | 47,9 | 33,4> | 35,0 | 26,5 | 37,5 | 35,7 | Nippon Steel & Sumitomo Metal | Japonska |
3 | 47,1 | 45,8 | 42,8 | 44,4 | 52,9[10] | 40,2[11] | 33,3 | 31,1 | Hebei Iron and Steel | Kitajska |
4 | 43,3 | 43,9 | 42,7 | 43,3 | 37,0 | 31,3 | 35,4 | 28,6 | Baosteel Group | Kitajska |
5 | 41,4 | 38,4 | 39,9 | 39,1 | 35,4 | 31,1 | 34,7 | 31,1 | POSCO | Južna Koreja |
6 | 35,3 | 35,1 | 32,3 | 31,9 | 30,1 | 26,4 | 23,3 | 22,9 | Jiangsu Shagang | Kitajska |
7 | 34,3 | 33,7 | 30,2 | 29,8 | 22,1 | 20,1 | 16,0 | 16,2 | Ansteel | Kitajska |
8 | 33,1 | 39,3 | 36,4 | 37,7 | 36,6 | 30,3 | 27,7 | 20,2 | Wuhan Iron and Steel | Kitajska |
9 | 31,4 | 31,2 | 30,4 | 29,9 | 31,1 | 25,8 | 33,0 | 34,0 | JFE | Japonska |
10 | 30,8 | 31,5 | 31,4 | 30,0 | 25,8 | 17,3 | 12,2 | 12,9 | Shougang | Kitajska |
11 | 26,2 | 25,3 | 23,0 | 23,8 | 23,5 | 21,9 | 24,4 | 26,5 | Tata Steel | Indija |
12 | 23,3 | 22,8 | 23,0 | 24,0 | 23,2 | 26,4 | 21,8[12] | 23,8 | Shandong Iron and Steel Group | Kitajska |
13 | 21,4 | 20,2 | 20,1 | 19,9 | 18,3 | 14,0 | 20,4 | 20,0 | Nucor Corporation | ZDA |
14 | 20,6 | 17,2 | 17,1 | 16,3 | 12,9 | 8,4 | 9,9 | 10,0 | Hyundai Steel | Južna Koreja |
15 | 19,7 | 20,4 | 21,4 | 22,0 | 22,3 | 15,2 | 23,2 | 21,5 | United States Steel Corporation | ZDA |
16 | 19,0 | 19,0 | 19,8 | 20,5 | 21,6 | 14,2 | 20,4 | 18,6 | Gerdau | Brazilija |
17 | 18,9 | 18,8 | 17,3 | 16,7 | 15,4 | 14,8 | 15,0 | 14,2 | Maanshan Iron and Steel Company | Kitajska |
18 | 18,5 | 19,3 | 17,3[13] | 19,2[14] | 17,5 | - | - | - | - | Kitajska |
19 | 16,3 | 15,9 | 15,1 | 17,9 | 16,7 | 11,0 | 15,9 | 17,0 | ThyssenKrupp | Nemčija |
20 | 16,3 | 16,8 | 15,1 | 16,5 | 22,1 | 9,1 | 7,4 | 7,6 | Benxi Steel | Kitajska |
21 | 16,1 | 15,5 | 14,9 | 12,1 | 11,9 | 10,9 | 11,3 | 9,7 | Novolipetsk Steel | Rusija |
22 | 15,5 | 16,1 | 15,9 | 16,8 | 16,3 | 15,3 | 17,7 | 16,2 | Evraz | Rusija |
23 | 15,4 | 14,3 | 12,7 | 14,0 | 12,7 | 8,9 | 11,0 | 10,9 | China Steel | Tajvan |
24 | 15,4 | 15,0 | 14,1 | 15,9 | 15,1 | 11,8 | 11,3 | 11,1 | Valin Steel Group | Kitajska |
25 | 15,2 | 14,3 | 13,8 | 12,4 | 8,8 | 8,4 | 6,5 | 7,8 | Jianlong Steel | Kitajska |
26 | 14,4 | 14,3 | 13,6 | 12,6 | 11,4 | 10,6 | 10,0 | 10,1 | IMIDRO | Iran |
27 | 14,2 | 15,7 | 15,1 | 15,3 | 14,7 | 16,7 | 19,2 | 17,3 | Severstal | Rusija |
28 | 13,6 | 13,2 | - | - | - | - | - | - | Fangda Steel | Kitajska |
29 | 13,6 | 13,5 | 13,5 | 13,5 | 13,6 | 13,5 | 13,7 | 13,9 | Steel Authority of India Limited | Indija |
30 | 13,0 | 11,9 | 13,0 | 12,2 | 11,4 | 9,6 | 12,0 | 13,3 | Magnitogorsk Iron and Steel Works | Rusija |
31 | 12,7 | 11,8 | 8,5 | N/A | 6,4 | 5,5 | 3,8 | 3,0 | JSW Steel Ltd | Indija |
32 | 11,4 | 12,7 | 13,2 | 11,2 | 9,8 | 9,9 | 7,5 | 6,2 | Kitajska | |
33 | 11,2 | 14,3 | 12,5 | 14,4 | 13,8 | 7,0 | 8,2 | 9,1 | Metinvest | Ukrajina |
34 | 10,9 | 10,3 | 7,7 | 9,4 | 10,0 | 8,5 | 9,0 | Anyang Steel | Kitajska | |
35 | 10,7 | 10,0 | 10,1 | 9,9 | 9,6 | 9,5 | 9,2 | 9,3 | Kitajska | |
36 | 10,7 | 10,7 | 10,2 | 10,2 | 10,1 | 10,1 | 8,8 | 9,8 | Baotou Steel | Kitajska |
37 | 10,5 | 9,7 | 7,3 | 5,8 | N/A | N/A | N/A | N/A | Hebei Jingye Iron and Steel | Kitajska |
38 | 10,3 | 11,2 | 10,1 | 10,2 | 8,6 | 7,6 | 6,9 | 7,4 | Kitajska | |
39 | 10,3 | 10,2 | 9,1 | 8,6 | N/A | N/A | N/A | N/A | Handan Zongheng Iron and Steel | Kitajska |
Skupno | 1637+ | 1607 | 1548 | 1490 | 1413 | 1219 | 1329 | 1351 | - | - |
Literatura
[uredi | uredi kodo]- Bojan Kraut: Krautov strojniški priročnik (KSP)
- Franc Vodopivec: Kovine in zlitine, Inštitut za kovinske materiale in zlitine, 2002
- Aleksander Kveder (ur.): Metalurški priročnik, Tehniška založba Slovenije, 1972
- Eduard Houdremont: Einführung in die Sonderstahlkunde. Verlag von Julius Springer, Berlin 1935, 566 p.
- Eduard Houdremont: Handbuch der Sonderstahlkunde. 3. verbesserte Auflage (letzter Hand), Springer-Verlag Berlin, Göttingen, Heidelberg, und Verlag Stahleisen, Düsseldorf 1956, 1538 S. in 2 Bänden.
- Verein Deutscher Eisenhüttenleute (Izd.): Werkstoffkunde Stahl, Band 1: Grundlagen. Springer-Verlag Berlin, Heidelberg, New York, Tokyo, und Verlag Stahleisen, Düsseldorf 1984, 743 S.
- Verein Deutscher Eisenhüttenleute (Izd.): Werkstoffkunde Stahl, Band 2: Anwendungen. Springer-Verlag Berlin, Heidelberg, New York, Tokyo, und Verlag Stahleisen, Düsseldorf 1985, 862 S.
- Claus und Micah Wegst: Stahlschlüssel – Key to Steel 2010 Nachschlagewerk. Verlag Stahlschlüssel 2010, ISBN 3-922599-26-5.
- Industrieverband Massivumformung: Neue Stähle für die Massivumformung. Inforeihe Massivumformung, März 2012, ISBN 978-3-928726-28-3.
Glej tudi
[uredi | uredi kodo]- jeklena litina
- seznam držav po proizvodnji jekla
- nitridiranje
- kaljenje jekel
- Jeklo / tabele in grafike (v nemščini.)
Zunanje povezave
[uredi | uredi kodo]- ↑ 1,0 1,1 Smelting. Encyclopædia Britannica. 2007.
- ↑ 2,0 2,1 »Alloying of Steels«. Metallurgical Consultants. 28. junij 2006. Arhivirano iz prvotnega spletišča dne 21. februarja 2007. Pridobljeno 28. februarja 2007.
- ↑ Smith & Hashemi 2006, str. ;365–372 .
- ↑ Smith & Hashemi 2006, str. ;373–378 .
- ↑ »Quench hardening of steel«. Arhivirano iz prvotnega spletišča dne 17. februarja 2009. Pridobljeno 19. julija 2009.
- ↑ »"World Steel Association - Top steel-producing companies 2014"« (PDF). Arhivirano iz prvotnega spletišča (PDF) dne 4. marca 2016. Pridobljeno 13. julija 2015.
- ↑ »"World Steel Association - Top steel-producing companies 2012"«. Arhivirano iz prvotnega spletišča dne 19. julija 2016. Pridobljeno 13. julija 2015.
- ↑ »World Steel Association: 2012/2013 Top 50 steel-producing companies and rank« (PDF). Arhivirano iz prvotnega spletišča (PDF) dne 13. maja 2015. Pridobljeno 13. julija 2015.
- ↑ »Top steel producers« (PDF). Arhivirano iz prvotnega spletišča (PDF) dne 7. marca 2012. Pridobljeno 13. julija 2015.
- ↑ MetalBulletin: Top steelmakers 2010
- ↑ MetalBulletin: Top steelmakers 2009
- ↑ China's top steel producers in 2008
- ↑ MetalBulletin: Top steel producers in China
- ↑ MetalBulletin: Top steelmakers 2011