Disclosure of Invention
The invention aims to solve the technical problem that the prior art is insufficient, and provides a local path planning method and system for intelligent driving under a mine, which are used for adaptively adjusting tracks, realizing transverse correction of a mine car before an intersection, ensuring that the mine car can safely pass through the intersection and improving the safety of an underground unmanned mine car at a branch intersection.
In order to solve the technical problems, the technical scheme adopted by the invention is as follows: a local path planning method for mine underground intelligent driving comprises the following steps:
1) detecting a characteristic beacon in the mine by the vehicle-mounted laser radar, if the characteristic beacon exists, indicating that the mine car is about to enter a bend, and entering the step 2); otherwise, indicating that the mine car is still in the straight-going stage, and entering the step 3);
2) extracting angle and distance information between the characteristic beacon and the mine car, calculating the relative distance between the characteristic beacon and the mine car in real time according to the angle and distance information, calculating the position of the mine car according to the absolute position of the beacon in the mine and the relative distance under a global coordinate system, realizing navigation positioning error correction, and entering step 4);
3) before the mine car enters the bend, adjusting the transverse deviation of the reference path according to the control error of the car body and the reactive reference path fed back by the mine car at the interface between the straight road and the bend to realize the transverse control correction of the mine car before entering the bend;
4) and after the mine car enters the curve, generating an expected path of the curve of the mine car according to the turning direction prompted by the beacon. The method applies the reactive path planning method to the local path planning of the unmanned mine car under the mine, uses the laser radar as the 'sight line' of the mine car, and solves the problem of inaccurate perception caused by dark visual field of the underground mining area; acquiring route scatter points in a mine car driving boundary acquired in real time by using a random point scattering-based mode, connecting the route scatter points through spline curves to generate an alternative route set, and ensuring that a planned route meets vehicle tracking conditions under the constraint of multiple targets; the characteristic beacon is set at the pre-bending position in consideration of the narrow road of the underground mining area, so that the correction of the positioning error is realized, the planned path is adjusted in real time by combining the tracking error, the mine car is ensured to enter the bend at a proper posture, the collision with the wall of the roadway is avoided, and the safety of the mine car in underground driving is improved. In the step 1), in the straight-going stage, the path planning is carried out by using the following steps:
A) carrying out discrete processing on the clustered and layered data points acquired by the vehicle-mounted laser radar to generate a travelable boundary;
B) taking the advancing direction of the vehicle as the positive direction of a y axis, being vertical to the advancing direction of the vehicle, taking the direction of anticlockwise rotation of 90 degrees of the advancing direction of the vehicle as the positive direction of an x axis, taking the transmitting center of the laser radar as the origin of coordinates to establish a coordinate system of the vehicle, and when a left boundary l is present in a travelable boundary, y is
l=a
lx
2+b
lx+c
lY and the right boundary r: y
r=a
rx
2+b
rx+c
rGenerating a reference path, wherein a
l、b
l、c
lRepresenting the left boundary curve coefficient, c
l>0,a
r、b
r、c
rRepresenting the coefficient of the right boundary curve, c
r<0; when only one boundary or no boundary exists in the drivable boundaries, detecting whether the laser radar has a fault; the reference path generation method comprises the following steps: randomly sampling in the area between the left boundary and the right boundary, i.e. the travelable area, and randomly generating route scatter points
Taking a laser radar mounting point as a starting point, taking a path scattered point which is farthest from the starting point in the longitudinal direction as an end point, and connecting all curves between any two longitudinally adjacent path scattered points between the starting point and the end point by utilizing cubic spline interpolation to obtain an alternative path; co-generate m
kTaking a strip path as an alternative path set, wherein m represents the scatter number of a transverse path, and k is a tableShowing the number of scattered points of the longitudinal path; calculating the fitness value of each alternative path by using the multi-objective advantage function, and taking the alternative path with the maximum fitness value as the multi-objective optimal reactive reference path, namely the reference path
g denotes the g-th segment, a, of the Path Path
g、b
g、c
gRepresents the curve coefficient of the g-th section of Path.
The invention generates the planned path by randomly scattering points and connecting curves, replaces the mode of directly connecting the points with the maximum safe distance as the planned path, not only ensures the selectivity of the mine car path, but also solves the problem that the vehicle cannot track because of singular points in the planned path.
The path scatter
The specific generation process comprises: the laser radar mounting point is taken as a starting point, the vehicle advancing direction is taken as a longitudinal direction, and the direction vertical to the longitudinal direction is taken as a transverse direction; taking k interval points with delta p as a longitudinal interval and m transverse interval points with delta s as a transverse interval in a transverse direction passing through each longitudinal interval point in a travelable area, and generating k multiplied by m interval points as path scatter points
Wherein
0.5≤Δp≤3;0.3≤Δp≤1。
According to the method for generating the route scatter points, the longitudinal planning distance and the control period are kept in a reasonable ratio through setting of the longitudinal parameters, the planning foresight and practicability are guaranteed, a plurality of selectable routes are generated through setting of the transverse parameters, and the diversity of the routes is guaranteed.
In step B), the expression of the multi-objective advantage function is as follows:
f=ωdfdis+ωsfsmo+ωufsec;
wherein f isdisRepresenting path length, ωdRepresenting length weight, fsmoIndicates smoothness, ωsRepresenting a smoothness weight, fsecRepresenting the safe distance, ω, between the path and the travelable boundaryuRepresenting a safe distance weight, fmin_disRepresents the shortest distance, f, from the path scatter to the left and right boundaries(j+1)Represents a curve segment, f ″, between longitudinally adjacent path scatter points j and j +1(j+1)Representing a curve segment f(j+1)Of (c) is performed.
The method selects the path in the alternative path set in a multi-target optimization mode, ensures that the planned path achieves comprehensive optimization in path length, path smoothness and safety, and provides important guarantee for vehicle tracking. In step 2), the specific implementation process for implementing the navigation positioning error correction includes:
I) taking the advancing direction of the driving task as the positive direction of a y axis, taking the direction which is vertical to the advancing direction of the driving task and rotates 90 degrees anticlockwise to the advancing direction of the driving task as the positive direction of an x axis, taking the starting point of the driving task as the origin of coordinates to establish a global coordinate system, combining N beacons in pairs, respectively calculating the abscissa and the ordinate of the mine car by utilizing the position of each combination under the global coordinate system and the corresponding distance between the combination and the mine car, and screening out the coordinates of which the difference between the abscissas and the difference between the ordinates are both smaller than an error threshold value; wherein, the relative distance between the mine car and each combination is the component of the distance from the center of the reflector to the laser radar on the installation horizontal plane of the laser radar;
II) respectively averaging the abscissa and the ordinate in the screened coordinates to obtain the actual position of the mine car.
According to the invention, the laser radar reflector is arranged as the characteristic beacon, and the coordinate transformation and geometric theorem are applied, so that the reverse thrust of the mine car on the real-time position of the underground roadway is realized, the problem of inaccurate positioning caused by weak underground GPS signals is solved, and the navigation positioning error correction is realized.
The specific implementation process of the step 3) comprises the following steps: the lateral correction of the tramcar is achieved using the following curve, Trajectory:
wherein Tracjectory represents the reactive reference Path after adjusting the lateral offset, g represents the g-th segment of the Path Path, a
g、b
g、c
gCoefficient of the curve representing the g-th segment of Path, c
1Represents the intercept of the curve segment in the path closest to the mine car, epsilon represents the mine car heading correction factor, v represents the longitudinal speed of the mine car, deltad represents the relative position of the mine car in the longitudinal direction with respect to the beacon,
indicating the travel time of the mine car from the beacon.
The invention utilizes the control error fed back by the mine car to adaptively adjust the track, realizes the transverse correction of the mine car in front of the intersection and ensures that the mine car can safely pass through the intersection.
In the step 4), the process of generating the expected path of the curve of the mine car comprises the following steps:
a) identifying the prompting turning direction of the characteristic beacon, and selecting the geometric description l, y of the drivable boundary of the mine tunnel with the same prompting directionl=alx2+blx+clOr r: yr=arx2+brx+cr(ii) a Wherein l represents a left turn; r represents a right turn;
b) taking k 'characteristic points on a travelable boundary l or r every delta p' in the advancing direction of the mine car, and generating a curve reference path by using a least square fitting method;
c) deletion curvature greater than Clim' generating a desired trajectory for the curve;
d) and the expected curve track is transversely deviated by delta q to be taken as the expected curve path.
The mine car is limited by a detection visual angle at a turning position, data of roadway walls on two sides of a roadway at the turning position cannot be accurately acquired, and data of only one side can be acquired. The invention also provides a method for planning the straight path under the mine, which comprises the following steps:
A) performing discrete processing on the clustered and layered data points acquired by the vehicle-mounted laser radar, and eliminating convex points in the travelable boundary points to generate travelable boundaries;
B) taking the advancing direction of the vehicle as the positive direction of a y axis, being vertical to the advancing direction of the vehicle, taking the direction of anticlockwise rotation of 90 degrees of the advancing direction of the vehicle as the positive direction of an x axis, taking the transmitting center of the laser radar as the origin of coordinates to establish a coordinate system of the vehicle, and when a left boundary l is present in a travelable boundary, y is
l=a
lx
2+b
lx+c
lAnd the right boundary r: y
r=a
rx
2+b
rx+c
rGenerating a reference path, wherein a
l、b
l、c
lRepresenting the left boundary curve coefficient, c
l>0,a
r、b
r、c
rRepresenting the coefficient of the right boundary curve, c
r<0; when only one boundary or no boundary exists in the drivable boundaries, detecting whether the laser radar has a fault; the reference path generation method comprises the following steps: randomly sampling in the area between the left boundary and the right boundary, i.e. the travelable area, and randomly generating route scatter points
Taking a laser radar mounting point as a starting point, taking a path scattered point which is farthest from the starting point in the longitudinal direction as an end point, and connecting all curves between any two longitudinally adjacent path scattered points between the starting point and the end point by utilizing cubic spline interpolation to obtain an alternative path; co-generate m
kTaking the path as an alternative path set, wherein m represents the scattering number of the transverse path, and k represents the scattering number of the longitudinal path; calculating a fitness value of each alternative path by using a multi-objective advantage function, and taking the alternative path with the maximum fitness value as a multi-objective optimal reactive reference path, namely a reference path
g denotes the g-th segment, a, of the Path Path
g、b
g、c
gRepresents the curve coefficient of the g-th section of Path.
The invention ensures the selectivity of the mine car path and solves the problem that the vehicle cannot track due to singular points in the planned path by generating the planned path through random point scattering and curve connection.
The invention also provides a system for planning the local path under the mine, which comprises computer equipment; the computer device is configured or programmed for performing the steps of the mine downhole local path planning method of the invention.
In order to facilitate acquisition of corresponding data, the computer device is in communication with a vehicle-mounted lidar; the vehicle-mounted laser radar is used for acquiring signals of characteristic beacons arranged at cut interfaces of straight roads and curved roads in a mine.
Compared with the prior art, the invention has the beneficial effects that:
1. the mine roadway wall detection and reactive planning path generation method based on the laser radar is used, the mine area environment sensing is realized by the laser radar, and a reactive path planning mode is adopted, so that the problem of difficulty in sensing and planning caused by dim light is solved, and the intelligent control of the mine car is preliminarily realized;
2. the invention adopts a positioning compensation method facing to a laser radar beacon, detects a characteristic beacon through the laser radar, calculates the relative position and angle between the beacon and a mine car in real time, converts the relative position and angle to a global coordinate system through the coordinate system, and reversely pushes the position of the mine car according to the absolute position of the beacon, thereby realizing the correction of navigation positioning errors;
3. the invention adopts a track generation method based on feedback type tracking error correction, self-adaptively adjusts the track by utilizing the control error fed back by the mine car, realizes the transverse correction of the mine car before the intersection, ensures that the mine car can safely pass through the intersection, improves the safety of the underground unmanned mine car at the branch intersection, and solves the problem that the intersection fails to turn if the tracking error of the mine car is not corrected in time at the intersection of a straight road and a curve of the underground mine.
Detailed Description
The intelligent vehicle modified by the underground development machine is adopted in the embodiment, the laser radar is arranged at the tail of the vehicle in front of the vehicle, the vehicle can run in the straight direction and the reverse direction, and the intelligent driving experiment is carried out in an underground mining area.
Referring to fig. 1, a reactive local path planning and trajectory generation method under a mine includes the following steps:
step 1: detecting a characteristic beacon in the mine by the vehicle-mounted laser radar, if the characteristic beacon exists, indicating that the mine car is about to enter a bend, and entering the step 2); otherwise, indicating that the mine car is still in the straight-going stage, and entering the step 3);
step 2: extracting angle and distance information between the characteristic beacon and the mine car, calculating the relative distance between the characteristic beacon and the mine car in real time according to the angle and distance information, calculating the position of the mine car according to the absolute position of the beacon in the mine and the relative distance under a global coordinate system, realizing navigation positioning error correction, and entering step 4);
and step 3: before the mine car enters the bend, adjusting the transverse deviation of the reaction type planning path according to the control error of the car body and the reaction type planning path fed back by the mine car at a straight road and bend cutting interface, and realizing the transverse control correction of the mine car before entering the bend;
and 4, step 4: and after the mine car enters the curve, generating an expected path of the curve of the mine car according to the turning direction prompted by the beacon.
The generation of the straight-going phase reactive planning path in step 1 is further described with reference to fig. 2(a) and fig. 2 (b):
carrying out discrete processing on the clustered and layered data points acquired by the vehicle-mounted laser radar to generate a travelable boundary;
taking the advancing direction of the vehicle as the positive direction of a y axis, being vertical to the advancing direction of the vehicle, taking the direction of anticlockwise rotation of 90 degrees of the advancing direction of the vehicle as the positive direction of an x axis, taking the transmitting center of the laser radar as the origin of coordinates to establish a coordinate system of the vehicle, and when a left boundary l is present in a travelable boundary, y is
l=a
lx
2+b
lx+c
lY and the right boundary r: y
r=a
rx
2+b
rx+c
rGenerating a reference path, wherein a
l、b
l、c
lRepresenting the left boundary curve coefficient, c
l>0,a
r、b
r、c
rRepresenting the coefficient of the right boundary curve, c
r<0; when only one boundary or no boundary exists in the drivable boundaries, detecting whether the laser radar has a fault; the reference path generation method comprises the following steps: randomly sampling in the area between the left boundary and the right boundary, i.e. the travelable area, and randomly generating route scatter points
Taking a laser radar mounting point as a starting point, taking a path scattered point which is farthest from the starting point in the longitudinal direction as an end point, and connecting all curves between any two longitudinally adjacent path scattered points between the starting point and the end point by utilizing cubic spline interpolation to obtain an alternative path; co-generate m
kThe strip path is used as an alternative path set, m represents a horizontal directionThe number of path scatter points, k represents the number of longitudinal path scatter points; calculating the fitness value of each alternative path by using the multi-objective advantage function, and taking the alternative path with the maximum fitness value as the multi-objective optimal reactive reference path, namely the reference path
g denotes the g-th segment, a, of the Path Path
g、b
g、c
gRepresents the curve coefficient of the g-th section of Path.
The longitudinal direction in the invention refers to the y-axis direction, and the transverse direction is the x-axis direction; a rotation of 90 ° counter-clockwise in the direction of forward movement of the vehicle means a rotation on the plane of the y-axis.
Scatter of path
The specific generation process comprises: the laser radar mounting point is taken as a starting point, the vehicle advancing direction is taken as a longitudinal direction, and the direction vertical to the longitudinal direction is taken as a transverse direction; taking k interval points with delta p as a longitudinal interval and m transverse interval points with delta s as a transverse interval in a transverse direction passing through each longitudinal interval point in a travelable area, and generating k multiplied by m interval points as path scatter points
Wherein
0.5≤Δp≤3;0.3≤Δp≤1。
The method comprises the following steps of setting a multi-objective advantage function, considering path smoothness, path length and safety distance between a local path and a travelable boundary by multiple objectives, wherein the advantage function is as follows:
f=ωdfdis+ωsfsmo+ωufsec
in the above formula, fdisRepresenting path length, ω d2 denotes the length weight, fsmoIndicates smoothness, ω s4 denotes smoothness weight, fsecRepresenting the safe distance, ω, between the path and the travelable boundaryu1.5 denotes the safe distance weight, fmin_disRepresents the shortest distance, f, from the path scatter to the left and right boundaries(j+1)Represents a curve segment, f ″, between longitudinally adjacent path scatter points j and j +1(j+1)Representing a curve segment f(j+1)Of (c) is performed. As shown in fig. 2(b), the boundary of the mine is not a smooth straight line or curve, the path with the largest safety distance is obtained by averaging the left and right boundaries of the mine, and the path has many singular points and cannot be tracked by vehicles; the method for smoothing the path with the maximum safety distance comprises the following steps: the method comprises the steps that 5 characteristic points are taken at equal intervals on a path with the maximum safety distance, cubic spline interpolation is carried out on the 5 characteristic points to generate a smooth path, the path obtained by the method has high requirement on selection of the characteristic points, and meanwhile if the number of laneway wall defect points is large, the larger the difference of the transverse distances among the characteristic points is, the worse the smoothness of the path is possible; the obtained path has lower requirement on the accuracy of the roadway wall data, and has higher stability and generalization performance on the aspects of path length, path smoothness and safety synthesis, thereby being easy to realize vehicle tracking.
The correction of the navigation positioning error in step two is further described with reference to fig. 3(a) and fig. 3 (b):
fig. 3(a) is a driving scene of an underground mine, which is a F-shaped driving route with a total length of one way 147m, and which includes 15 steps, wherein the straight line is 1, 4,5, 8, 11, 12, 15; the pre-turning is 2, 6, 9 and 13; the turns are 3, 7, 10, 14. The beacons are set at the edge of the mine tunnel in the top view as shown in fig. 3, and in order to ensure that no laser signal blocking occurs between the beacons, the beacons may be set at vertically different positions and should be spaced from each other by a certain distance.
Under a vehicle coordinate system, extracting angle and distance information [ R ] between the center of the characteristic beacon reflector and the vehicle-mounted laser radar through clustering and layeringi,ωi,αi](reference: Xujing Bond, Liuyang, Wang Xiaoze, Von Song, Liu boat.) research on laser-guided AGV Global positioning method based on reflective markers [ J]Manufacturing automation 2020,42(02): 113-; 1,2, …, N, alphaiIs the horizontal rotation angle omega from the center of the reflector to the laser radariThe vertical angle from the center of the reflector to the laser radar is defined; riThe distance from the center of the reflector to the laser radar; where N is the number of characteristic beacons at each intersection of a straight and curved cut.
Because the mine car is only influenced by the transverse position and the longitudinal position when being controlled at the bottom layer, but not influenced by the vertical position, the calculation of the vertical position of the mine car is not considered; taking the left boundary of the mine as the forward direction of a y-axis driving task, taking the direction which is vertical to the forward direction of the driving task and rotates 90 degrees anticlockwise as the forward direction of an x-axis, taking the starting point of the driving task as the origin of coordinates to establish a global coordinate system, and utilizing the absolute position (x) of a beacon under the global coordinate systemi',yi'), (i ═ 1,2, 3) reverse thrust car position [ x0,y0]Firstly, two beacons are combined into three groups, and the transverse and longitudinal positions of the mine car are respectively calculated, and the beacons (x) are used1',y1')、(x2',y2') take two beacon absolute positions (x) as an examplei',yi') as the center of circle, by the relative distance R between the mine car and the beaconicosωi(i-1, 2) calculating intersection coordinates for the radius:
(x-x′1)2+(y-y′1)2=R2 1 cos2ω1
(x-x'2)2+(y-y'2)2=R2 2 cos2ω2
each group generating 2Possible coordinates for each tramcar, three sets yielding a total of 6 possible coordinates for each tramcar
(m ═ 1,2,3,4,5, 6); then, the 6 groups of coordinates are screened, and coordinates with the difference between the horizontal coordinates and the difference between the vertical coordinates smaller than an error threshold value are screened out:
and finally, averaging the screened coordinates to generate coordinates which are the actual positions of the mine cars. The experimental result is shown in fig. 3(b), and it can be known from fig. 3(b) that the positioning accuracy on the ground can reach centimeter level and is relatively stable, and the positioning error of the underground mining area can be continuously increased along with the time.
The trajectory generation method based on feedback-type tracking error correction described in step three is further described with reference to fig. 4(a) and 4 (b):
the lateral correction of the tramcar is achieved using the following curve, Trajectory:
wherein Tracjectory represents the reactive Path after adjusting the lateral offset, g represents the g-th segment of the Path Path, a
g、b
g、c
gCoefficient of the curve representing the g-th segment of Path, c
1Denotes the intercept of the curve segment closest to the mine car in the path, ε 0.1 denotes the mine car heading correction factor, v 10km/h denotes the longitudinal car velocity, Δ d denotes the relative position of the mine car in the longitudinal direction with respect to the beacon,
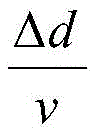
indicating the travel time of the mine car from the beacon. The experimental result is shown in fig. 4(b), before pre-entering into a curve, when the error between the vehicle and the expected path is large (more than 1.5m), the vehicle tracks the original multi-target path, and the mine road is limited to be too short and the original multi-target path is trackedThe error can not be corrected in time, and the bend-in failure can be caused, but the planned path can be adjusted in time according to the error between the vehicle and the expected path by adopting the track generation method based on the feedback type tracking error correction, so that the error between the mine car and the expected path before the bend-in can be kept in a small range, and the mine car can smoothly pass through the intersection.
And (3) generating a curve expected path: firstly, identifying the left turn (l) and the right turn (r) of the prompting turn direction of the beacon, and selecting the geometric description l: y of the driving boundary of the mine roadway with the same prompting direction
l=a
lx
2+b
lx+c
lOr r: y
r=a
rx
2+b
rx+c
rNext, 20 feature points are taken on the curve at intervals of Δ p' of 0.3m in the advancing direction of the mine car, and left turn is taken as an example
As a reference path point, generating a curve reference path by using least square fitting, and then limiting the curvature of the curve reference path, namely deleting the curvature larger than C
lim' 0.15 points generate the desired trajectory y of the curve
cur=a
curx
2+b
curx+c
curFinally, the curve planned trajectory y is obtained by shifting the curve desired trajectory lateral deviation Δ q to 1.7 in consideration of the vehicle body width
cur'=a
curx
2+b
curx+c
cur+Δq。
Furthermore, the safety of the underground mine is considered, when the mine car collides with an obstacle in the running process, the mine car is immediately decelerated and stopped, and the safety is ensured.