Method for longitudinal processing by utilizing inverse spherical aberration correction and application
Technical Field
The invention belongs to the technical field of femtosecond laser processing, and particularly relates to a method for longitudinally stretching a femtosecond laser focus by utilizing inverse spherical aberration correction, so as to realize high-precision longitudinally uniform micro-optical element processing.
Background
The micro-optical element is a basic component of micro-nano photonics and has great importance in the aspects of optical chips, micro-phototherapy and the likeTo be applied. The femtosecond laser processing technology has become one of the main technologies for processing micro-optical devices due to its high processing precision, high patterning level and effective modification of materials. Taking quartz material as an example, femtosecond laser can induce a nano-grating structure in the femtosecond laser under higher power, and the high pulse energy of the femtosecond laser can remarkably change the refractive index of an induced region (up to 10)-3Magnitude) to obtain an optical diffraction element. In order to improve the efficiency of the optical diffraction element, it is necessary to increase the length of the induced nano-grating, i.e., to increase the depth-to-diameter ratio of the longitudinal process. Accordingly, the prior art generally adopts a method of overlapping multiple layers of gratings or reducing the numerical aperture (increasing the depth of focus). However, the former process takes a long time, and the superimposed gratings are liable to be staggered, thereby degrading the quality of the optical diffraction element. The latter is disadvantageous to miniaturization of the device due to the low process resolution resulting from the reduced numerical aperture.
Disclosure of Invention
Aiming at the defects of the prior art, the technical problems to be solved by the invention are as follows: a method for longitudinal machining using inverse spherical aberration correction is provided. The femtosecond laser focus is subjected to inverse spherical aberration correction through the spatial light modulator, and a focal spot which is obviously stretched along the longitudinal direction is obtained at a deeper position in the material to be processed, so that the stretched focal spot is directly utilized to continuously scan in the material to be processed, and the longitudinal processing with a large depth-diameter ratio is realized. The principle is as follows: the Booth group in uk proposes a phase modulation formula for spherical aberration correction, i.e. reducing the longitudinal stretching of the focal spot when the femtosecond laser is incident into the interior of the material by optical field phase modulation. Phase compensation for spherical aberration correction
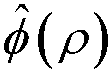
In order to realize the purpose,
wherein, λ is femtosecond laser wavelength, ρ is normalized pupil radius of femtosecond laser emission, and dnomFor any depth inside the material to be processed, s is a compensation factor (the specific value of which depends on the number of objective lenses)Numerical apertures NA and dnom),n 11 is the refractive index of air, n2The NA is the numerical aperture of the femtosecond laser emergent objective lens as the refractive index of the material to be processed. Wherein, the actual depth of the femtosecond laser incident into the material is determined by the s value. Based on Booth formula, the invention further introduces a stretching factor fst(0.1≤fstLess than or equal to 20), expanding the value of s in the formula from the original single value to a range, and accordingly obtaining the phase compensation hologram of the focal spot required to be stretched. Subsequently, the femtosecond laser is subjected to reverse spherical aberration phase modulation (longitudinal stretching of the focal spot is increased) by using the spatial light modulator, so that the focal spot of the femtosecond laser incident to the interior of the material to be processed is significantly stretched in the longitudinal direction, and a required stretched focal spot is formed.
The invention is realized by the following technical scheme:
the method for longitudinally processing by utilizing the inverse spherical aberration correction comprises the following specific steps:
(1) expanding the compensation factor s to obtain an inverse spherical aberration correction phase compensation hologram;
the method comprises the following specific steps: firstly, a stretching factor f is introduced for a spherical aberration correction formula
stExpanding the compensation factor s to [ s-f
st/2,s+f
st/2]The interval of (1), namely expanding the value of s from the original single value to a range; the value of the expanded compensation factor s determines the depth of the femtosecond laser incident into the material to be processed, so that the expansion of s enables the femtosecond laser focal spot to stretch longitudinally in the material to be processed; then, according to the formula in MATLAB
Calculating s, wherein
Substituting each parameter in the formula, and calculating an s value; wherein, λ is femtosecond laser wavelength, ρ is normalized pupil radius of femtosecond laser emission, and d
nomAt any depth within the material to be processed,
n 11 is the refractive index of air, n
2The NA is the numerical aperture of the femtosecond laser emergent objective lens as the refractive index of the material to be processed,phi is the spherical aberration correction phase, D (rho) is the defocusing phase, and then the calculation result of the compensation factor s is substituted into the interval [ s-f ] after the expansion of the compensation factor s
st/2,s+f
st/2]Dividing the interval into N equal parts, and enabling the expanded compensation factor to obtain N values in the interval; finally, the N values are substituted into a spherical aberration correction formula
Wherein,
for phase compensation, carrying in all parameters, and finally generating an inverse spherical aberration correction phase compensation hologram required by stretching a focal spot;
(2) modulating the phase to obtain a stretching focal spot;
the method comprises the following specific steps: firstly, loading an anti-spherical aberration correction phase compensation hologram on a spatial light modulator; then, enabling a beam of femtosecond laser to be incident to a spatial light modulator for phase modulation, and enabling the modulated reflected light to pass through a 4-f system consisting of a first lens and a second lens, wherein the focal lengths of the two lenses are 400mm and 300mm respectively; finally, the femtosecond laser emitted from the 4-f system enters the material to be processed through an objective lens to be focused, and linear focal spots stretched along the longitudinal direction are obtained;
(3) scanning point by point to carry out longitudinal processing;
the method comprises the following specific steps: and performing point-by-point scanning processing inside the material to be processed by using the stretched femtosecond laser linear focal spot, and finally realizing longitudinal processing with large depth-diameter ratio inside the material.
Further, the stretching factor f of step (1)stThe value is 0.1-20; the values of the quantities in the calculation formula are that lambda is 515-800nm and the processing depth dnom0.1-3000 μm, rho is 0-1, theta is 0-2 pi, n1=1,n21.46, NA 0.7-1.2, and N1000-2000.
Further, the resolution of the hologram in step (1) is 1024 × 1024-1920 × 1080 and the bit depth is 8.
Further, the wavelength of the femtosecond laser in the step (2) is 515-800nm, the pulse width is 100-400fs, the power is 50-1000mW, and the repetition frequency is 100Hz-200 kHz; the numerical aperture NA of the objective lens is 0.7-1.2, the magnification is 30-100, and the focusing depth is 1-500 mu m; the material to be processed is quartz.
Further, the point-by-point scanning in the step (3) is carried out, the scanning speed is 5 mu m/s-1mm/s, the exposure time is 5-2000 mu s, and the point distance is 10nm-1 mm.
Further, the depth-diameter ratio of the longitudinal processing in the step (3) is 3-500.
The invention also provides the application of longitudinal processing in the aspect of integrated photonic devices by utilizing inverse spherical aberration correction, namely the application of longitudinal processing in processing nano grating structures.
Compared with the prior art, the invention has the following advantages:
(1) linear focal spots which are obviously stretched along the longitudinal direction are obtained by utilizing inverse spherical aberration correction, a longitudinal structure with a large depth-diameter ratio can be processed in the material at one time, the longitudinal depth of the structure does not need to be accumulated through multiple processing, the structure staggering caused by multiple processing is avoided, and the processing efficiency and the structure quality are improved at the same time;
(2) and the stretching focal spot obtained by the inverse spherical aberration correction is directly processed longitudinally without reducing the numerical aperture NA to increase the processing depth, thereby improving the processing resolution.
Drawings
FIG. 1 is a schematic optical path diagram of a longitudinal machining method using anti-spherical aberration correction according to the present invention;
FIG. 2 is a schematic diagram of the present invention for obtaining a longitudinally stretched focal spot using anti-spherical aberration correction;
FIG. 3 is an anti-spherical aberration corrected phase compensation hologram in accordance with the present invention; wherein the upper right-hand digit represents the stretch factor f corresponding to the hologramstTaking values;
FIG. 4 is a scanning electron microscope image of a method of longitudinal machining using anti-spherical aberration correction according to the present invention; wherein the scale bar is 2 μm; wherein the upper right-hand number represents the stretch factor fstTaking values;
FIG. 5 is a scanning electron microscope image of a method for cycle-controlled high aspect ratio machining with inverse spherical aberration correction according to the present invention. Where the scale bar is 5 μm and the upper numbers represent the period of the setup.
Detailed Description
The following detailed description of embodiments of the invention refers to the accompanying drawings. It should be understood that the detailed description and specific examples, while indicating the present invention, are given by way of illustration and explanation only, not limitation.
Example 1
And obtaining a stretching focal spot inside the material to be processed by utilizing the inverse spherical aberration correction.
According to Booth formula, the femtosecond laser focus focused in the material to be processed is phase-modulated, i.e. the phase compensation factor s is expanded into an interval [ s-f ] from the original single valuest/2,s+fst/2]Thereby the focal spot is stretched significantly in the longitudinal direction, resulting in a linear focal spot that can be processed with a large depth-to-diameter ratio in the longitudinal direction.
Utilizing the inverse spherical aberration correction to obtain a stretching focal spot in the material to be processed, and specifically comprising the following steps of:
(1) expanding the compensation factor s to obtain an inverse spherical aberration correction phase compensation hologram: firstly, a stretching factor f is introduced aiming at Booth formula
stMake the compensation factor s take on the value of [ s-f
st/2,s+f
st/2]The interval of (1), namely expanding the value of s from the original single value to a range; the value of the compensation factor s determines the depth of the femtosecond laser incident into the material to be processed, so that the expansion of s enables the femtosecond laser focal spot to be stretched obviously in the material to be processed along the longitudinal direction; then, according to the formula in MATLAB
Calculating s, wherein
Substituting each parameter in the formula, and calculating an s value; wherein λ is 515nm, d
nom3000 μm, rho is 0-1, theta is 0-2 pi, n
1=1,n
21.46, NA 1.2; then, according to the calculation result of s, s is calculatedThe value is expanded into an interval [ s-f ]
st/2,s+f
st/2]F used
stThe value is sequentially seven values of 0, 1, 2, 3, 4, 5 and 6, and seven expanded value intervals are correspondingly obtained; dividing a value interval into 1000 equal parts, and enabling s to obtain 1000 values in the interval; and finally, substituting the 1000 s values into a spherical aberration correction formula and the parameters to finally generate seven inverse spherical aberration correction phase compensation holograms required by stretching the focal spot, wherein the resolution ratio is 1080 multiplied by 1080 and the bit depth is 8.
(2) Modulating the phase to obtain a stretched focal spot: the femtosecond laser wavelength is 515nm, the pulse width is 400fs, the power is 50mW, and the repetition frequency is 200 kHz; the numerical aperture NA of the objective lens is 0.9, the magnification is 100, the focusing depth is 50 mu m, and the material to be processed is quartz; firstly, sequentially loading seven anti-spherical aberration correction phase compensation holograms onto a spatial light modulator; then, enabling a beam of femtosecond laser to be incident to a spatial light modulator for phase modulation, and enabling the modulated reflected light to pass through a 4-f system consisting of a first lens and a second lens, wherein the focal lengths of the two lenses are 400mm and 300mm respectively; finally, the femtosecond laser emitted from the 4-f system enters the quartz through the objective lens to be focused into the quartz, and a linear focal spot which is obviously stretched along the longitudinal direction is obtained.
As can be seen from fig. 1, the femtosecond laser is first incident to the spatial light modulator loaded with the anti-spherical aberration correction phase compensation hologram for phase modulation; then, the modulated reflected light sequentially passes through the first lens and the second lens, and finally enters the material to be processed through the objective lens to form a required stretching focal spot.
As can be seen from fig. 2, when the femtosecond laser after the aspheric aberration correction is incident into the material to be processed from the objective lens, the femtosecond laser emitted from different positions of the objective lens focuses to a certain depth of the longitudinal axis due to the phase compensation of the aspheric aberration correction, and the depth is determined by the expanded s value; therefore, the stretching factor f is utilizedstBy fully expanding the s value, a linear focal spot which is obviously stretched along the longitudinal direction in the figure can be formed.
As can be seen from FIG. 3, when the stretch factor f is givenstWhen 0, 1, 2, 3, 4, 5 and 6 are taken in sequence, corresponding to each otherSeven different anti-spherical aberration correction phase compensation holograms are generated; the holograms are loaded on a spatial light modulator, and the femtosecond laser focal spot light field reflected by the spatial light modulator obtains the needed anti-spherical aberration correction.
As can be seen from FIG. 4, the stretch factor f is determinedst0, 1, 2, 3, 4, 5 and 6 are sequentially taken, and a series of nanowires with different shapes can be etched and written by respectively exposing the obtained stretching focal spots on a certain section (X-Y plane) in the quartz. As the stretch factor increases, the width of the nanowire gradually decreases while the length significantly increases. This shows that expanding s by using the stretch factor can obtain a linear focal spot that is significantly stretched in the longitudinal direction, and the depth-to-diameter ratio of the focal spot increases with the increase of the stretch factor, which can be up to 500. Meanwhile, the numerical aperture NA of the objective lens used in the processing is 0.9, which is obviously higher than the NA used in the depth longitudinal processing in the prior art, so that higher processing resolution can be provided.
Example 2
And processing the nano grating structure with large depth-diameter ratio by utilizing the stretching focal spot.
When the repetition frequency of the femtosecond laser is high, a continuous line or plane can be obtained by scanning point by point. The femtosecond laser focused inside the material to be processed is used for stretching the focal spot, and point-by-point scanning is carried out along the Z-axis direction (the section where the stretched focal spot is positioned is set as an X-Y plane), so that the nano-grating structures (namely a series of equidistant nano-surfaces vertical to the X-Y plane) arranged along the X-Y plane can be obtained.
The method for processing the nano grating structure with the large depth-diameter ratio by utilizing the stretching focal spot comprises the following specific steps:
(1) expanding the compensation factor s to obtain an inverse spherical aberration correction phase compensation hologram: same as example 1, wherein f is usedstThe value is 20, and the corresponding expansion interval of s is [ s-10, s +10 ]]。
(2) Modulating the phase to obtain a stretched focal spot: the same as example 1, wherein the objective lens used had a depth of focus of 500. mu.m.
(3) And scanning point by point to carry out longitudinal processing: scanning the stretched femtosecond laser linear focal spot point by point in the quartz along the Z-axis direction; the scanning speed is 5 μm/s, the exposure time is 5 μ s, and the dot pitch is 50 nm; finally, a series of nano-gratings (as shown in fig. 5) arranged along the X-Y plane are obtained, the grating period can be increased from 200nm to infinity (related to the pre-designed line spacing during processing, which is only increased to 1000nm for comparison), the section length is 43 μm, and the single line width is 90 nm. The depth-diameter ratio is 43 mu m/90nm to 477.
The preferred embodiments of the present invention have been described in detail with reference to the accompanying drawings, however, the present invention is not limited to the specific details of the above embodiments, and various simple modifications can be made to the technical solution of the present invention within the technical idea of the present invention, and these simple modifications are within the protective scope of the present invention.
It should be noted that the various technical features described in the above embodiments can be combined in any suitable manner without contradiction, and the invention is not described in any way for the possible combinations in order to avoid unnecessary repetition.
In addition, any combination of the various embodiments of the present invention is also possible, and the same should be considered as the disclosure of the present invention as long as it does not depart from the spirit of the present invention.