Preparation process of medium-temperature chemical nickel-phosphorus plating alloy on metal surface
Technical Field
The invention relates to the technical field of chemical nickel-plating alloys, in particular to a preparation process of a medium-temperature chemical nickel-phosphorus-plating alloy on a metal surface.
Background
In modern society, with the continuous development of industry, the demand for steel materials is increasing. Steel is widely used as a commonly used iron-based metal material in many fields of national economy. However, steel materials are subjected to continuous and severe impact and abrasion in the use process, so that high requirements are imposed on the wear resistance and corrosion resistance of the materials. In order to prolong the service life of a workpiece and improve the performance of metal, various surface engineering technologies are developed and applied, wherein the chemical plating technology is widely applied to actual production due to the advantages of simple and convenient process, low cost, uniform plating thickness, large-area plating and the like.
Chemical plating is started from chemical nickel plating at first, and along with the development of science and technology and the progress of industry, the application range of chemical nickel plating is gradually expanded, so that the chemical nickel plating has considerable application in the industries of aerospace, automobiles, machinery, petrochemical industry and the like. The chemical plating liquid is divided into two major systems of alkaline and acidic, and is divided into three grades of high phosphorus, medium phosphorus and low phosphorus according to the phosphorus content of a plating layer. High-phosphorus coating: the chemical plating layer with the phosphorus content of more than 10 percent in the plating film belongs to amorphous non-magnetism and has higher corrosion resistance; the phosphorus content of the middle phosphorus layer is 6-10%, the corrosion resistance is lower than that of the high phosphorus layer, and the coating structure is the combination of microcrystal and amorphous; the phosphorus content of the low-phosphorus layer is lower than 6%, and the structure of nickel in the low-phosphorus layer is crystalline, so that the low-phosphorus layer has good mechanical properties but weaker corrosion resistance.
At present, the operation temperature of a plating solution commonly used in industrial production is 85-95 ℃, although the deposition speed of nickel is high, the process control is difficult, the energy consumption is high, the equipment consumption is serious, and the labor condition is severe. Research shows that the plating cost can be reduced by 5-10% when the temperature is reduced by 10 ℃. In addition, plating of materials (such as plastics, etc.) with lower softening points and high deformation temperatures at high temperatures can cause deformation and modification of the substrate, thereby limiting further application of electroless nickel plating. Therefore, lowering the plating temperature of electroless nickel plating is a hot spot of research in this field. In addition, the alkaline plating solution has higher plating speed at medium temperature, low energy consumption and higher brightness of the plated layer. However, the alkaline solution has poor stability and is difficult to maintain, the microstructure of the alkaline chemical nickel plating layer is flaky, the crystallite size is large, pores and even grain boundaries can be generated among grains, and the acidic chemical nickel plating layer has a layered or granular structure and can reach no pores, so that the wear resistance, the corrosion resistance and the hardness of the acidic chemical nickel plating layer are superior to those of the alkaline chemical nickel plating layer. Therefore, more and more researchers are dedicated to the research of the medium-temperature acid chemical nickel plating process.
In order to improve the relatively slow chemical plating deposition speed at low temperature and obtain a better plating layer, Zhonghuimei et al, university of Fujian, 2006 adopted an ultrasonic chemical nickel plating process to successfully plate on an organic film at low temperature. However, the use of ultrasonic waves is not a condition for the entire industrial application. In 1998, the nickel-phosphorus alloy plating temperature of Huangshan, Monksong and the like of the university of south China marble was controlled to 70 ℃ under an acidic condition, but specific names of acid and stabilizer are not stated. In 2000, the discussion about the chemical nickel plating deposition mechanism of Liu Yongjian and Wang Yingcha indicates that the addition of rare earth with proper species and proper dosage in the plating solution can increase the number of active points on the catalytic surface, thereby increasing the uniform nucleation capability and nucleation number during metal deposition, increasing the nucleation speed and improving the deposition speed of nickel ions. When the number of active points on the catalytic surface is increased to a certain degree, the content of the rare earth is continuously increased, and the number of the catalytic active points is not increased any more; at this time, the excessive rare earth prevents the adsorption of hypophosphite ions and decreases the deposition rate, but the amount of rare earth is not specified. In view of the above, it is necessary to design a preparation process of the medium-temperature chemical nickel-phosphorus-plated alloy on the metal surface.
Disclosure of Invention
The invention aims to provide a preparation process of a medium-temperature chemical nickel-phosphorus-plated alloy on a metal surface, which is characterized in that a proper amount of sodium hypophosphite, boric acid and lactic acid are added into a basic plating solution, so that a prepared coating is uniform and compact and is crystallized in a cellular structure, and the wear resistance and the corrosion resistance are improved.
In order to realize the purpose, the invention provides a preparation process of a medium-temperature chemical nickel-phosphorus plating alloy on a metal surface, which comprises the following steps:
(1) preparing a formula of solution A: 27-54g/L of nickel sulfate, 9-42g/L of buffering agent, 0-28mL/L of lactic acid, 0.2-0.4g/L of inorganic acid, 1-2mL/L of rare earth brightener and a small amount of stabilizer;
(2) preparation of solution A: weighing the above medicines according to the formula dosage of the plating solution, adding water, stirring to dissolve and stand, standing for more than 5 hours, filtering out insoluble substances, adding an additive, stirring and dissolving to obtain solution A;
(3) and (3) preparation of a liquid B: firstly, preparing 40-80g/L sodium hypophosphite solution, then weighing the solution, adding a proper amount of water, stirring for dissolving, standing for more than 5 hours, filtering out insoluble substances, and stirring to obtain solution B;
(4) preparing a plating working solution: mixing the solution A and the solution B according to the proportion of 1: 1, mixing the prepared solution A and the solution B, heating the mixture in a constant-temperature water bath at 60-68 ℃ for 1 hour, and adjusting the pH value to 5.0 to obtain the plating working solution.
Preferably, the buffer is anhydrous sodium acetate.
Preferably, the inorganic acid is boric acid.
Preferably, the stabilizer is potassium iodide.
Preferably, the molar ratio of the nickel sulfate to the sodium hypophosphite in the plating working solution is 0.13-0.15. Preferably, the preparation process of the medium-temperature chemical nickel-phosphorus plating alloy on the metal surface comprises the following steps:
(1) preparing a formula of solution A: 27-54g/L of nickel sulfate, 9-21g/L of sodium acetate, 0-14mL/L of lactic acid, 0.2-0.4g/L of inorganic acid, 1-2mL/L of rare earth brightener and a small amount of stabilizer;
(2) preparation of solution A: weighing the above medicines according to the formula dosage of the plating solution, adding water, stirring to dissolve and stand, standing for more than 5 hours, filtering out insoluble substances, adding an additive, stirring and dissolving to obtain solution A;
(3) and (3) preparation of a liquid B: firstly, preparing 20-40g/L sodium hypophosphite solution, then weighing the solution, adding a proper amount of water, stirring for dissolving, standing for more than 5 hours, filtering out insoluble substances, and stirring to obtain solution B;
(4) preparing a plating working solution: mixing the solution A and the solution B according to the proportion of 1: 1, mixing the prepared solution A and the solution B, heating the mixture in a constant-temperature water bath at 60-68 ℃ for 1 hour, and adjusting the pH value to 5.0 to obtain the plating working solution.
The steel piece is plated by using the plating working solution, and the specific process comprises the following steps: (1) polishing and derusting; (2) chemical degreasing; (3) washing with water; (4) activating with 10% sulfuric acid; (5) washing with water; (6) washing with deionized water; (7) plating (60-68 ℃ for 1 h); (8) and (5) washing with water. The deposition rate of the dried coating was then measured: the deposition rate of the plating layer is determined by a gravimetric method, and the dried test piece is accurately weighed before and after plating, and then calculation is carried out. The calculation formula is as follows:
wherein ν is the deposition rate μm/h; m
1And M
0The mass g of the test piece after and before plating; rho is the plating density of 7.85g/cm
3(ii) a S is the area cm of the test piece
2(ii) a t is plating time h.
The specific deposition principle is as follows: the hypophosphite is oxidized to generate nascent hydrogen, nickel ions are reduced to metallic nickel by the nascent hydrogen, part of the hypophosphite is reduced to elemental phosphorus by the nascent hydrogen, and the phosphorus and the nickel are co-deposited to form a chemical nickel-plating layer. The nascent hydrogen is expressed theoretically by the chemical reaction equation as follows:
Ni2++2[H]→Ni+2H+…………………………………②
2[H]→H2↑……………………………………………③
H2PO2-+[H]→P+H2O+OH-……………………………④
the reaction takes place on the surface of catalytic activity, and needs the external energy supply under the acidic condition, the reaction produces metallic nickel, phosphite radical, hydrogen ion and hydrogen, the hydrogen ion makes the pH value of the plating solution drop gradually, inhibit the reduction of nickel (② type), promote the codeposition of phosphorus (④ type).
Therefore, the preparation process of the medium-temperature chemical nickel-phosphorus alloy plating on the metal surface is adopted, and a proper amount of sodium hypophosphite, boric acid and lactic acid are added into the basic plating solution, so that the prepared coating is uniform and compact and is crystallized in a cellular structure, and the wear resistance and the corrosion resistance are improved.
The technical solution of the present invention is further described in detail by the accompanying drawings and embodiments.
Drawings
FIG. 1 is a flow chart of a process for preparing a medium-temperature chemical nickel-phosphorus plating alloy on a metal surface according to the invention;
FIG. 2 is a graph showing the effect of sodium hypophosphite dosage on plating speed in an embodiment of the process for preparing a medium temperature chemical nickel-phosphorus plated alloy on metal surface according to the present invention;
FIG. 3 is a graph showing the effect of temperature on plating rate of an embodiment of the process for preparing a medium temperature chemical nickel-phosphorus plating alloy on a metal surface according to the present invention;
FIG. 4 is a graph showing the change of plating speed for different anhydrous sodium acetate amounts according to an embodiment of the process for preparing a medium temperature chemical nickel-phosphorus plating alloy on a metal surface;
FIG. 5 is a graph showing the effect of lactic acid dosage on plating speed in an embodiment of the process for preparing a medium-temperature chemical nickel-phosphorus plating alloy on a metal surface according to the present invention;
FIG. 6 is a SEM image of the coating layer of an embodiment of the preparation process of the medium-temperature chemical nickel-phosphorus alloy plating on the metal surface;
FIG. 7 is an EDS energy spectrum of the plating layer of the embodiment of the preparation process of the medium-temperature chemical nickel-phosphorus plating alloy on the metal surface.
Detailed Description
FIG. 1 is a flow chart of a process for preparing a medium-temperature chemical nickel-phosphorus plating alloy on a metal surface, and as shown in the figure, the invention provides a process for preparing a medium-temperature chemical nickel-phosphorus plating alloy on a metal surface, which comprises the following steps:
(1) preparing a formula of solution A: according to the concentration, 27-54g/L of nickel sulfate, 9-42g/L of buffering agent, 0-28mL/L of lactic acid, 0.2-0.4g/L of inorganic acid, 1-2mL/L of rare earth brightening agent and a small amount of stabilizing agent, wherein the buffering agent is anhydrous sodium acetate, the inorganic acid is boric acid, and the stabilizing agent is potassium iodide;
(2) preparation of solution A: weighing the above medicines according to the formula dosage of the plating solution, adding water, stirring to dissolve and stand, standing for more than 5 hours, filtering out insoluble substances, adding an additive, stirring and dissolving to obtain solution A;
(3) and (3) preparation of a liquid B: firstly, preparing 40-80g/L sodium hypophosphite solution, then weighing the solution, adding a proper amount of water, stirring for dissolving, standing for more than 5 hours, filtering out insoluble substances, and stirring to obtain solution B;
(4) preparing a plating working solution: mixing the solution A and the solution B according to the proportion of 1: 1, mixing the prepared solution A and the solution B, heating the mixture in a constant-temperature water bath at the temperature of between 60 and 68 ℃ for 1 hour, and adjusting the pH value to be 5.0 to obtain plating working solution, wherein the molar ratio of nickel sulfate to sodium hypophosphite in the plating working solution is between 0.13 and 0.15.
Further, the preparation process of the medium-temperature chemical nickel-phosphorus plating alloy on the metal surface comprises the following steps:
(1) preparing a formula of solution A: 27-54g/L of nickel sulfate, 9-21g/L of sodium acetate, 0-14mL/L of lactic acid, 0.2-0.4g/L of inorganic acid, 1-2mL/L of rare earth brightener and a small amount of stabilizer;
(2) preparation of solution A: weighing the above medicines according to the formula dosage of the plating solution, adding water, stirring to dissolve and stand, standing for more than 5 hours, filtering out insoluble substances, adding an additive, stirring and dissolving to obtain solution A;
(3) and (3) preparation of a liquid B: firstly, preparing 20-40g/L sodium hypophosphite solution, then weighing the solution, adding a proper amount of water, stirring for dissolving, standing for more than 5 hours, filtering out insoluble substances, and stirring to obtain solution B;
(4) preparing a plating working solution: mixing the solution A and the solution B according to the proportion of 1: 1, mixing the prepared solution A and the solution B, heating the mixture in a constant-temperature water bath at 60-68 ℃ for 1 hour, and adjusting the pH value to 5.0 to obtain the plating working solution.
Example 1
The concentrations of the other additives and nickel sulfate were fixed: 15g/L of anhydrous sodium acetate, 10ml/L of lactic acid, 0.2g/L of boric acid, a proper amount of potassium iodide, 27g/L of nickel sulfate, and plating temperature of 65 ℃ for 1h, wherein the contents of sodium hypophosphite in the plating solution are respectively changed to be 20g/L, 25g/L, 28g/L, 29g/L, 30g/L, 31g/L, 33g/L, 35g/L and 40g/L, and tests are carried out, and as can be seen from figure 2, the plating speed shows the change trend of slow increase, rapid decrease and slow decrease along with the increase of the amount of sodium hypophosphite. When the content of sodium hypophosphite is lower than 28g/L, the relative nickel salt content is higher, and when the nickel salt content is higher or exceeds a critical value, Ni in the solution is caused2+Too high leads to the premature generation of nickel hypophosphite precipitate, thereby lowering the stability of the plating solution and lowering the plating speed. With the increase of the content of the sodium hypophosphite, when the content of the sodium hypophosphite reaches 28g/L, the negative effect relative to nickel salt is reduced, the plating speed is increased, and when the molar ratio of the nickel sulfate to the sodium hypophosphite is 0.13-0.15, the plating speed is maximum. The plating rate is sharply decreased after reaching the maximum value because the concentration of free hypophosphite ions in the solution is increased as the amount of sodium hypophosphite used is increased, and excessive hypophosphite ions react with nickel ions to generate precipitates, resulting in instability of the plating solution and thus lowering the plating rate.
Example 2
27g/L of nickel sulfate, 30g/L of sodium hypophosphite, 15g/L of anhydrous sodium acetate, 1ml/L of rare earth brightener, 10ml/L of lactic acid, 0.2g/L of boric acid and a small amount of potassium iodide are taken, experiments are carried out at different temperatures, as can be seen from figure 3, the plating speed is in a change trend of 'increasing first and then reducing' along with the increase of the temperature, and the deposition rate is increased due to the fact that the temperature is increased to enable ions to move violently. Integrated by the Arrhenius formula
A is constant, and thus the influence of temperature on the reaction rate, i.e., k is exponential to temperature T, can be seen. And the index factor
The boltzmann energy distribution law shows that the fraction of molecules with energy above Ea in the total number of molecules is greater than Ea, and for a given chemical reaction, when the temperature T is increased,
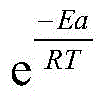
the value of (a) increases, that is, the proportion of the activated molecules in the total number of molecules increases, resulting in an increase in the k value and an increase in the reaction rate. The rate reaches the maximum at 64 ℃, and after that, the temperature continues to rise, and the plating rate drops and tends to be gentle, because the activity of sodium hypophosphite in the plating solution continuously rises due to the rise of the temperature, the precipitation of phosphorus in the plating solution is promoted, so that the instability of the plating solution is increased, the plating solution starts to decompose, and at the moment, although the temperature rises and the k value increases, the rate constant is not dominant, and the plating rate is reduced under the combined action of the temperature rise and the k value.
Example 3
Fixing other additive concentrations: 27g/L of nickel sulfate, 30g/L of sodium hypophosphite, 10ml/L of lactic acid, 0.2g/L of boric acid and a proper amount of potassium iodide, wherein the plating temperature is 65 ℃, and the time is 1 h. Experiments are carried out by changing the content of anhydrous sodium acetate in the plating solution to be respectively 9g/L, 12g/L, 13.5g/L,15g/L, 16.5g/L,18g/L and 21g/L, and as can be seen from figure 4, when the concentration of sodium acetate is smaller, the plating speed is not changed greatly along with the concentration of sodium acetate, and when the dosage of sodium acetate is larger than 13g/L, the deposition rate is suddenly increased, then is suddenly decreased and finally tends to be gentle. This change occurs because sodium acetate acts both as a buffer and as an accelerator. As a buffering agent, the pH value of the plating solution can be effectively prevented from changing too much in the plating process, thereby prolonging the service life of the plating solution. The reaction in solution: h2PO2-+H2O→HPO3 2-+H++2[H]+e-,[H]+[H]→H2([H]As active hydrogen), a small amount of acetic acidSodium acts as a promoter, acts on this reaction, weakens the bonding force of hydrogen and phosphorus atoms in sodium hypophosphite, and accelerates H on the one hand2PO2-The P-H bond is broken, the metal surface can obtain electrons from broken phosphorus and hydrogen atoms, the reduction capability of the metal surface is obviously enhanced along with the enrichment of the electrons on the metal surface, and the reduction process of nickel ions and hydrogen ions can be accelerated, so that the deposition speed is improved. On the other hand, the reaction is apt to generate [ H ]],[H]To Ni2+Has a promoting effect on reduction. It is known that a small amount of sodium acetate is equivalent to enhance the activity of sodium hypophosphite. When the amount of sodium acetate used becomes large, the reaction: h2PO2-+H2O→HPO3 2-+H++2[H]+ e-accelerates, excess active hydrogen is produced, side reactions: [ H ]]+[H]→H2Cause a large amount of [ H ]]The self-reaction competes with the reduction reaction on the metal surface and becomes the main reaction, thereby affecting the reduction of nickel ions on the metal surface and finally affecting the plating rate.
Example 4
Fixing other additive concentrations: 27g/L of nickel sulfate, 30g/L of sodium hypophosphite, 15g/L of anhydrous sodium acetate, 0.2g/L of boric acid and a small amount of potassium iodide, wherein the plating temperature is 65 ℃, and the time is 1 h. Experiments were conducted by changing the lactic acid content in the plating solution to 0ml/L, 2ml/L, 4ml/L, 6ml/L, 8ml/L,10ml/L, 12ml/L, 14ml/L, respectively, and it can be seen from FIG. 5 that the plating rate tends to decrease gradually as the amount of lactic acid used increases, because the plating solution contains the complex complexing agent, but since the boric acid concentration is too low, it does not function well with lactic acid, and when the amount of lactic acid used increases, Ni tends to increase2+Mostly complexed with lactic acid, Ni in solution2+The content decreases and reduced Ni2+ decreases, resulting in a decrease in plating rate.
The preparation and use process conditions of the optimal medium-temperature chemical nickel-phosphorus alloy plating solution are optimized by adding a proper amount of rare earth brightener and stabilizer potassium iodide into the basic plating solution and using anhydrous sodium acetate as a buffering agent: 27g/L of nickel sulfate, 30g/L of sodium hypophosphite, 15g/L of anhydrous sodium acetate, 0ml/L of lactic acid, 0.2g/L of boric acid, a small amount of potassium iodide, 1ml/L of rare earth brightener, 65 ℃ of plating solution temperature, 5.0 of pH value and 1 hour of heating time.
The A3 cold-rolled steel plate is treated by the plating solution optimized by the optimal formula test through the optimal process, the experiment is carried out by using the experimental method, the SEM scanning of the plated film is carried out, the appearance of the SEM is shown in figure 6, the compactness of crystals is good, the crystal particles are fine, uniform, complete and compact, Ni-P is introduced into the plated layer, the corrosion resistance and the mechanical property of the film are greatly improved, and the steel body material can be well protected.
The coating composition analysis result of the optimized plating solution obtained by EDS (electron-beam deposition) spectroscopy is shown in FIG. 7, the abscissa of the result is Eb, which is the bonding energy of electrons in a certain shell of elements contained in the coating, the spectrum shows three peaks of Fe atomic energy spectrum and three peaks of Ni atomic energy spectrum, the electron bonding energy of the first shell of the two atoms is larger than the energy (1253.6eV) of a characteristic X-ray excitation source Mg (K α 1,2) line used by the spectrometer, the electrons in the other shells cannot be excited, the electrons in the other shells can be ionized, but the intensities of the peaks are not the same because the intensities of the peaks are related to the probability of photoionization and the escape depth of photoelectrons, i.e. the mean free path, of the electrons excited on different orbits are different, the escape depths of photoelectrons with different energies of different substances are different, therefore, the peaks of the different orbits are not the same, the peaks of P atomic energy spectrum also show that the peaks of the different elements are dense, the peaks of the coating with different orbits also show that C atomic energy spectrum shows that the coating mainly contains Ni, Fe, P and the coating has a uniform phosphorus content of the coating, and the coating has a chemical property of iron, and the result shows that the coating has a chemical nickel-phosphorus content of 5.5% and a chemical nickel-iron-containing chemical nickel-2, and a chemical nickel-iron-2-containing chemical nickel-2 alloy coating, and a chemical nickel-2-iron-2 alloy coating with a homogeneous nickel-containing chemical nickel-2 alloy coating, and a homogeneous nickel-containing chemical nickel-iron-containing chemical.
TABLE 1 coating element ratio
Therefore, the preparation process of the medium-temperature chemical nickel-phosphorus alloy plating on the metal surface is adopted, and a proper amount of sodium hypophosphite, boric acid and lactic acid are added into the basic plating solution, so that the prepared coating is uniform and compact and is crystallized in a cellular structure, and the wear resistance and the corrosion resistance are improved.
Finally, it should be noted that: the above embodiments are only for illustrating the technical solutions of the present invention and not for limiting the same, and although the present invention is described in detail with reference to the preferred embodiments, those of ordinary skill in the art should understand that: modifications and equivalents may be made to the invention without departing from the spirit and scope of the invention.