Tamahagane
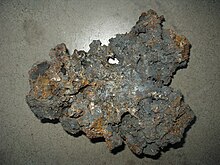
Le tamahagane (玉鋼 ) est la fraction de qualité supérieure de la loupe métallique issue du tatara, le bas fourneau traditionnel japonais. Des meilleurs morceaux du tamahagane est issu l'acier traditionnel utilisé dans la fabrication des sabres japonais[1].
En 2008, il est essentiellement produit dans la préfecture de Shimane.
Production
[modifier | modifier le code]Extraction du minerai
[modifier | modifier le code]Le minerai de fer extrait au Japon se présente généralement sous la forme de gravier ou de sable fin noir. Le mot 砂鉄 (satetsu ) peut désigner toutes les formes de minerai, il est cependant plus employé pour désigner le sable ferrugineux. Le minerai, produit de l'érosion de couches naturelles, s'est déposé au fond des cours d'eau et s'y est mélangé avec d'autres sédiments. On le trouve principalement en bord de mer, dans les marais et au fond ou près des cours d'eau. Le satetsu se reconnaît à sa couleur allant du rouge au noir. Il ne contient que 1 % de fer pur.
Autrefois, le minerai de fer était séparé des autres sédiments en le faisant passer dans des canaux où l'eau était brassée. Ainsi, le minerai de fer plus dense se déposait au fond alors que les autres sédiments étaient emportés par le courant. Aujourd'hui, cette méthode est abandonnée du fait de son impact sur l'environnement.
Le fer présent dans le satetsu se trouve essentiellement sous la forme de trois minéraux distincts :
- la magnétite Fe3O4 ;
- la marcassite FeS2 ;
- l'hématite Fe2O3.
Réduction du minerai au tatara
[modifier | modifier le code]On extrait le fer pur du satetsu par réduction dans un bas fourneau, appelé tatara.
Un cycle opérationnel du tatara est de cinq jours : un pour préparer les parois de la cuve du tatara, trois pour fabriquer l'acier et un pour l'extraire du fourneau. Au cours d'un cycle, le tatara consomme environ 8 tonnes de satetsu ainsi que 13 tonnes de charbon de bois (qui sert à la fois de combustible et de réducteur).
Lorsque la température atteint 1 400 °C, on introduit de l'oxygène à l'aide de soufflets. Cet oxygène réagit avec le carbone provenant du charbon de bois pour donner de l'oxyde de carbone et la chaleur nécessaire aux réactions[1].
Le procédé donne une loupe, un bloc hétérogène d'acier de 2 tonnes, appelée kera. Une moitié du kera est composée d'acier ayant entre 0,6 et 1,5 % de carbone et est appelée tamahagane ; 50 à 66 % de ce tamahagane possède la teneur en carbone optimale pour la fabrication d'un sabre[1]. L'acier en périphérie est le tamahagane le plus recherché, du fait de sa plus forte teneur en carbone.
La technique du tatara a perduré jusqu'en 1925 environ. En 1975, le gouvernement japonais décide de rallumer les bas fourneaux de Shimane.
Caractéristiques du tamahagane
[modifier | modifier le code]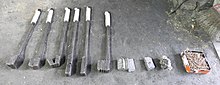
Les forgerons estiment qu'un bon tamahagane doit être lourd, dense, d'aspect brillant argenté et de structure cristalline fine. Au contraire, un mauvais tamahagane est grisâtre.
Avec la technique du tatara, le carbone n'est pas uniformément réparti dans le fer, ce qui est un défaut si l'on recherche un acier avec de bonnes propriétés mécaniques comme, par exemple, dans la fabrication d'un sabre traditionnel japonais : le forgeron pourra alors couper les meilleurs morceaux de la loupe (kera), les souder à la forge pour obtenir un lingot, puis « feuilleter » ce même lingot en l'étirant et le repliant sur lui-même plusieurs fois, afin d’homogénéiser les couches de fer contenant trop de carbone avec celles n'en contenant pas ou moins, donnant un acier composite de très bonne qualité.
Notes et références
[modifier | modifier le code]- Julien Peltier, « Katana, la lame du guerrier », Guerres & Histoire, no 38, , p. 77.