Papers by Charles-Andre Gandin
HAL (Le Centre pour la Communication Scientifique Directe), Nov 15, 2018
HAL (Le Centre pour la Communication Scientifique Directe), Jan 11, 2021
HAL (Le Centre pour la Communication Scientifique Directe), Jun 17, 2019
HAL (Le Centre pour la Communication Scientifique Directe), May 12, 2022
HAL (Le Centre pour la Communication Scientifique Directe), May 30, 2018
HAL (Le Centre pour la Communication Scientifique Directe), May 11, 2022
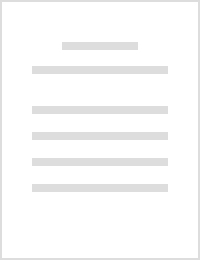
IOP Conference Series: Materials Science and Engineering
In laser powder bed fusion (L-PBF) process, a deposited powder layer is melted by a laser and sol... more In laser powder bed fusion (L-PBF) process, a deposited powder layer is melted by a laser and solidifies when the laser moves away. During solidification, the microstructure of the part is formed due to both epitaxial grain growth and nucleation. This structure has a strong influence on the final mechanical properties of parts and is influenced by the choice of process parameters such as the laser power and velocity or the scanning strategy. As a consequence, the prediction and characterization of this microstructure is of prime interest considering size, crystallographic orientations and shapes of grains. Among the approaches reported in the literature to model microstructure development, the Cellular Automaton (CA) method is a relevant choice to describe grain structure evolution. This model has been adapted to investigate microstructure formation during L-PBF process applied on an IN718 nickel-base superalloy. The steady state thermal behaviour at the scale of the melt pool is an...
IOP Conference Series: Materials Science and Engineering
In the present work, a methodology to identify parameters of an elastic viscoplastic behaviour la... more In the present work, a methodology to identify parameters of an elastic viscoplastic behaviour law is presented. Orthotropic elasticity and Hill48 plastic anisotropy for as-cast CMSX-4 are considered. In order to obtain the corresponding parameters by inverse analysis, an experimental database is built by tensile/relaxation tests at constant temperatures between 800°C and 1200°C on specimens oriented along <001>, <110> and <111> directions at different strain rates. Tests are performed with a resistive heating machine, using infrared thermography and digital image correlation. The obtained mechanical behaviour is very dependent on specimen orientation at all tested temperatures. Recrystallization behaviour is also very relevant to the specimens’ orientation.
HAL (Le Centre pour la Communication Scientifique Directe), Jun 20, 2022
HAL (Le Centre pour la Communication Scientifique Directe), Mar 14, 2006
Journal of Materials Science & Technology, 2022
16th edition of the International Conference on Computational Plasticity, 2021
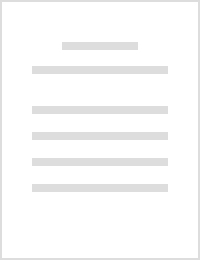
A 3D finite element model is developed to study heat exchange during the selective laser melting ... more A 3D finite element model is developed to study heat exchange during the selective laser melting (SLM) process. The level set functions are used to track the interface between the constructed workpiece and non-melted powder, and interface between the gas domain and the successive powder bed layers In order to reach the simulation in macroscopic scale of real part geometries in a reasonable simulation time, the energy input and the formation of the additive deposit are simplified by considering them at the scale of an entire layer or fraction of each layer. The layer fractions are identified directly from a description (e.g. using G-code) of the global laser scan plan of the part construction. Each fraction is heated during a time interval corresponding to the exposure time to the laser beam, and then cooled down during a time interval equal to the scan time of the laser beam over the considered layer fraction. The global heat transfer through the part under additive construction and...
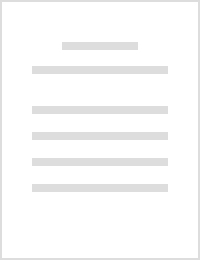
The objective of this work is to develop new numerical simulation techniques in meso- and macro-s... more The objective of this work is to develop new numerical simulation techniques in meso- and macro-scale to optimize the LBM process. The two scale models are under a level-set framework. A meso-scale simulation focuses on the laser interaction with the powder bed and subsequent melting and solidification. Thermomechanical finite element (FE) modelling is conducted at the scale of material deposition, and addresses the melting of the powder bed, the hydrodynamics of the fusion zone and the formation of local thermal stresses in the wake of the laser. A macro-scale simulation focuses on part construction. This thermomechanical finite element model addresses heat exchange and stress formation at the scale of the part by considering the non-exposed powder. In order to reach reasonable simulation time for industrial parts, the energy input and the formation of the additive deposit are simplified by considering them at the scale of an entire layer or fractions of each layer.
Uploads
Papers by Charles-Andre Gandin