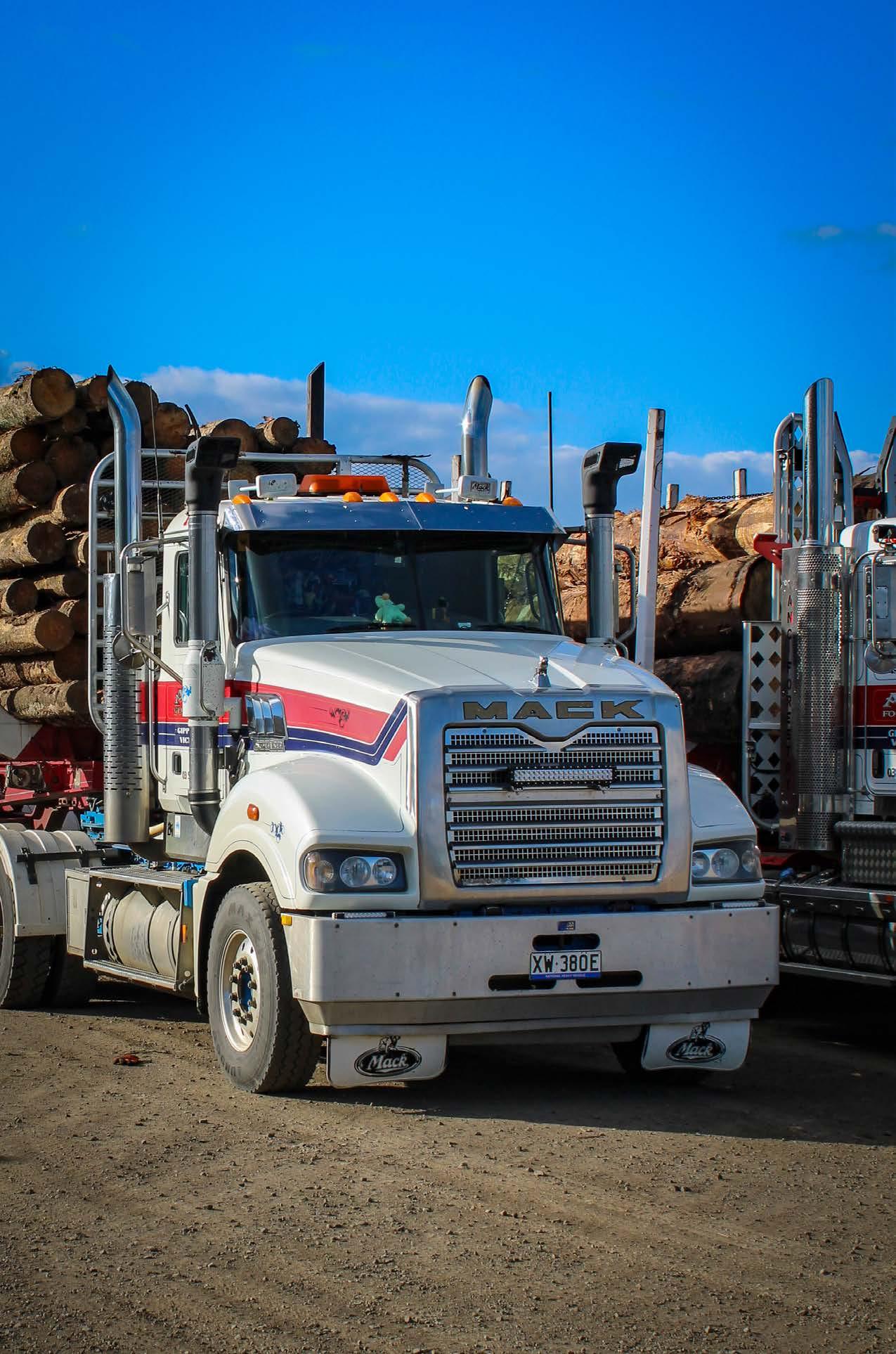




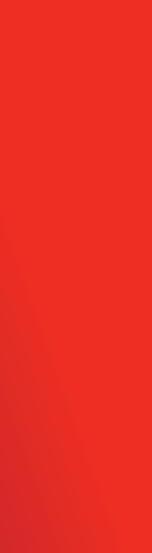
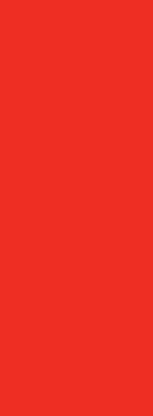

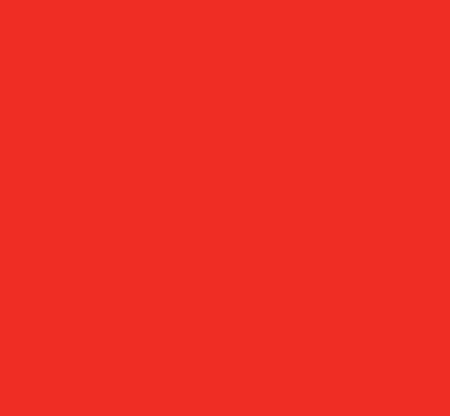
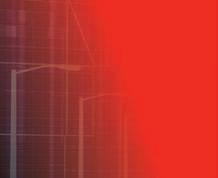
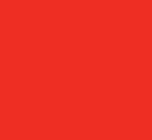
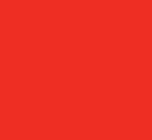







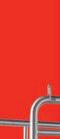



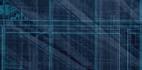

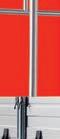

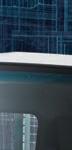

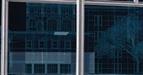

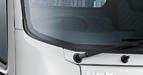

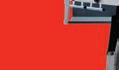

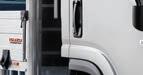
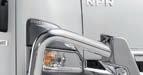

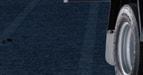

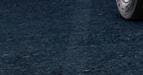

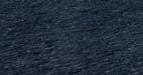
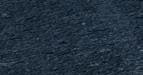

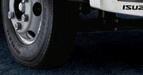

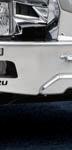


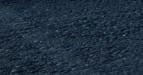
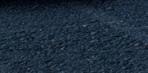
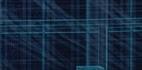

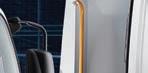


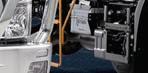






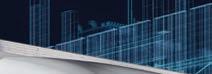
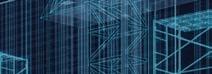

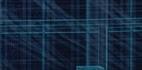




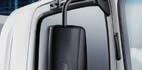
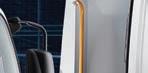


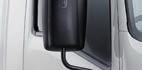

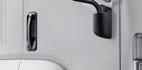
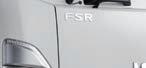

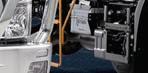
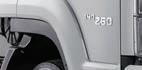
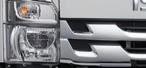

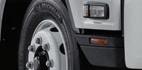

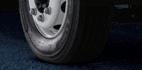
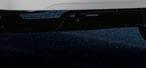



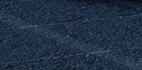


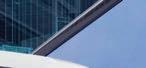
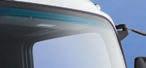

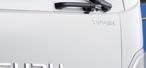

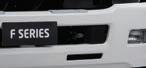
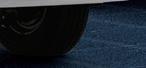

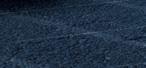


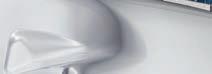
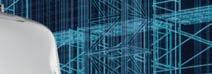
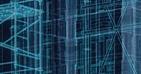
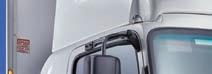

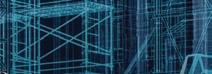

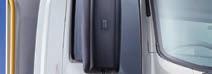


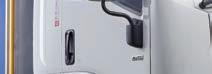
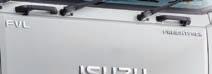

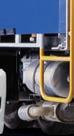
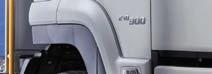


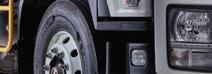
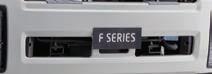

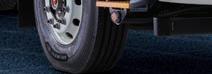



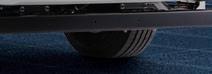

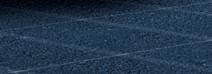
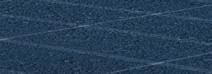

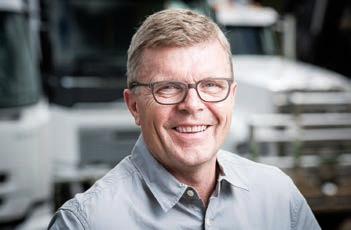
he trucking industry has always been in flux, constantly changing and developing to cope with the inevitable growth in size and complexity of the freight task. At the same time as this openness to change and development, there is also an innate conservatism which has characterised the development of our culture.
Every now and then some ‘outside the box’ thinking, or a major change in the nature of the freight task brings out the industry’s capacity for innovative thinking to solve an issue and, more often than not, creates a workable, and, hopefully profitable, solution.
This period seems to be building up to being one of those flexion points. This is where the trucking industry has to come up with new solutions and learn to live with some new realities in order to move forward into the 2030s.
The issues are starting to pile up. The average age of truck drivers continues to increase at a substantial clip. The experienced drivers are well into retirement age, as the baby boomers are now in their seventies.
That population is still the knowledge base in the industry, an industry which struggles to get young school leavers to even consider it. At the same time attempts to make us a more attractive proposition have been unsuccessful, poorly thought out and poorly funded.
Meanwhile, on another front, the trucking industry is set for major upheaval with the planned transition away from carbon to the bright sunlit uplands of a carbon free trucking industry.
The fact of the matter is, the freight task in the 2030s will be much bigger than it is now. The pressure to get away from carbon will be intense. There will be little progress towards that scenario if we don’t get our heads around how to survive in this brave new world. The consequences if we don’t, will be the road transport industry being a drag on economic growth and an impediment to progress.
It is simply a matter of asking ourselves whether we are ready for change and willing to make the difficult decisions which are becoming imperative. It’s pointless trying argue about change, because it’s coming whether we are like it or not.
Denial is not an option, drivers are aging and the replacement numbers are too low. The idea that autonomous trucks are going to be a solution any time soon is unthinkable in Australia, apart from a few major highway exceptions.
PUBLISHED BY
Prime Creative Media Pty Ltd
ABN 51 127 239 212
379 Docklands Drive, Docklands VIC 3008 Australia
Telephone: 03 9690 8766
Fax: 03 9682 0044
Email: enquiries@primecreative.com.au
Chief Executive Officer: John Murphy
Managing Editor: Geoff Crockett
Editor: Tim Giles
Journalist: Alex Catalano
Contributor: Bob Woodward
Correspondent: Will Shiers (UK)
Advertising Manager: Trevor Herkess: 0411 411 352, trevor.herkess@primecreative com.au
Client Success Manager: Salma Kennedy, salma.kennedy@primecreative.com.au
Production Manager: Michelle Weston
Circulation & Subscriptions Manager: Bobby Yung
Head of Design: Blake Storey
Designers: Cat Zappia, Jacqueline Buckmaster, Danielle Harris
Official Media Partners:
REGISTERED BY Australia Post - ISSN 1445-1158
SUBSCRIPTION
03 9690 8766
subscriptions@primecreative.com.au
Instead, trucking needs to turn its attention to a more rational and collaborative distribution system which avoids the level of empty or partially loaded running we do today and consolidates loads onto bigger, more productive trucks. At the same time we need to be attuned to the preferences of Generation Z, not the boomers.
There is no debate to be had about zero emissions. The ball is rolling globally and burying our heads in the sand will simply see us left behind by the rest of the world and become an economic back water.
EDITOR
PowerTorque Magazine is available by subscription from the publisher.
The right of refusal is reserved by the publisher.
Annual rates: AUS $60.00 (inc GST). For overseas subscriptions, airmail postage should be added to the subscription rate.
PowerTorque Magazine is owned and published by Prime Creative Media.
All material in PowerTorque Magazine is copyright and no part may be reproduced or copied in any form or by any means (graphic, electronic or mechanical including information and retrieval systems) without written permission of the publisher.
The Editor welcomes contributions but reserves the right to accept or reject any material.
While every effort has been made to ensure the accuracy of information, Prime Creative Media will not accept responsibility for errors or omissions or for any consequences arising from reliance on information published.
The opinions expressed in PowerTorque Magazine are not necessarily the opinions of, or endorsed by the publisher unless otherwise stated.
DAF is versatile and an all-rounder with the perfect combination of superior comfort and luxury for the driver and maximum vehicle efficiency for the operator. So, you need a prime mover with superior robustness and high payload? There’s a DAF for that!
Whether your needs are long-distance haulage, city distribution, construction transportation, bulk or tank transport, the versatility of DAF keeps you moving, and that’s good for business. DAF.COM.AU
Dozens of smart new road transport and distribution operations popping up around Australia are moving away from the traditional trucking model.
This year’s Rural Transport Rising Star, Luke Cannon, has come a long way in a few years from a livestock truck workshop, through to truck driving, to handling a busy livestock transport fleet like Fraser’s.
The winner of the Truck of the Year Australasia 2024, the Western Star X Series was a long time in the making. It’s here now and PowerTorque has looked into the origin story of this ground breaking range of trucks for the Australasian market.
Looking at the realities which will face transport operations as they migrate across from fossil fuel dependency to the zero carbon economy, one of experts in the field examines some possible scenarios.
The National Heavy Vehicle Regulator has been active in New South Wales for over two years now, so we spent the day at the Mount White Checking Station to see how the transition has changed the interface between the trucking community and its regulator.
Descending from a long line of shearers and sheep farmers, Mark Williams is a primary producer and shearer based outside of Goulburn in New South Wales.
Volvo’s engineers have managed to squeeze out 780hp from its new 17-litre engine, which is just enough for the FH16 to knock arch-rival Scania off the top spot to become Europe’s most powerful production truck.
It’s a perennial question on many and varied topics, but the question, ‘does size matter?’ is also relevant in the truck world. There’s cab size and engine size and many other things to consider.
28 FROM LOGBOOKS TO LEGAL
Navigating contracts and onboarding in the trucking world can be confusing at the best of times. The team at Clear Employment Relations Advice Team explain the ins and outs.
60 NHVR PROVIDES INDUSTRY ‘HEALTH CHECK’
NHVR Chief Operations Officer Paul Salvati addresses the newest iteration of the National Roadworthiness Survey, which hopes to drive safety and efficiency improvements across Australia’s heavy vehicle fleet.
64 CHAMPIONING FAIR TOLLING FOR HEAVY VEHICLES
NatRoad CEO Warren Clark says the recently released NSW Independent Toll Review leaves plenty to be desired when it comes to meaningful reform for a sustainable transport system.
78 REASONS TO GO DIGITAL
Nobody wakes up each morning and hopes to spend the day filling out and filing paperwork. Relying on paper and manual processes limits your ability to become more efficient, have better safety outcomes and boost your bottom line.
80 IMPLEMENTING SAFETY MANAGEMENT SYSTEMS FOR TRANSPORT OPERATORS
Adding a safety management system to your fleet can have major benefits aside from just meeting legal and regulatory standards.
82 SAFETY IS A TEAM EFFORT
Regular PowerTorque contributor Bob Woodward reminds us that safety is a team effort and we all need to engage as part of the team. He also highlights the safety capabilities of the unused potential in some truck systems.
• Supporting drivers for more than 50 years
• Seating – on a higher level
The new Volvo VNL Autonomous was shown off at the ACT Expo in Las Vegas, developed in partnership with Aurora Innovation, which created the autonomous technology inside the truck.
It is currently slated for use across the United States, with a view to expand distribution worldwide.
“We are at the forefront of a new way to transport goods, complementing and enhancing transportation capacity, and thereby enabling trade and societal growth,” says president of Volvo Autonomous Solutions Nils Jaeger.
“This truck is the first of our standardised global autonomous technology platform, which will enable us to introduce additional models in the future, bringing autonomy to all Volvo Group truck brands, and to other geographies and use cases.”
The VNL Autonomous includes redundant steering, braking, communication, computation, power management, energy storage and vehicle motion management systems.
Chinese heavy vehicle manufacturer FAW Truck exports its trucks to 80 countries and regions around the world, and has now landed in the Australian market.
The JH6 Prime Mover has received approval under Australian Design Rules, and freatures a high end, bold and generous appearance.
Soon to be made available as a 6x4 prime mover, multiple
Mack has released its “gamechanging” new range of Euro 6 offerings for the Australian market.
A whole new range of Mack drivetrains has been revealed that includes an all-new range topping 780hp 17-litre MP11 engine and a stump pulling 3800Nm of torque.
The new Mack Trucks Euro 6 range is now available to order with the first vehicles expected to hit the road in early 2025.
Mack says the Super-Liner has already held the title of Australia’s
most powerful conventional truck for more than a decade, with this new model set to elevate its offering.
The arrival of the new MP8HE (high efficiency) engine platform will help evolve Mack’s powertrain, with the 2800Nm of torque increasing the output from Mack’s standard MP8 engine.
The fully integrated 70-inch walkthrough sleeper will also be available for order with Euro 6 Super-Liner and Titan products, with single and double bunks included.
configurations of the vehicle will be integrated with an eye towards excellent performance.
The JH6 is known for its fuel efficiency, light weight and low maintenance cost, forging a high cost performance truck with high efficiency, reliability, safety and comfortability.
The company has now reached more than 80 million unit sales worldwide.
has announced plans to globally manufacture hydrogen trucks in an effort to diversify its investment in zero emissions heavy vehicles.
global manufacturer says on-road tests with the hydrogen combustion engine trucks will begin in 2026, with Volvo planning to commercially launch the vehicle by the end of the decade.
move comes due to the ability that trucks running on green hydrogen have to decarbonise transport, with Volvo also citing the suitability of the technology over longer distances as a key advantage. develop the technology, Volvo has signed an agreement with
business, with the Corowa-based company farewelling the transport industry.
Initially founded in 1988 by brothers Greg and Ray Milthorpe, the two diesel mechanics used their collective experience at Corowa Truck and Trailer Repairs to pioneer
Greg Milthorpe says the operator managed to reach an impressive milestone.
“We’ve nurtured Milthorpe for about four decades now – from its modest inception, it has steadily expanded into a family-owned business, with my sons, Steve,
Rodney and Chris now integral parts
“However, as we embark on this new chapter, we eagerly anticipate embracing the joys of family life and relishing in newfound leisure.”
Ray’s recent retirement, coupled with Greg’s desire to follow suit, means the family business will gracefully exit the industry.
Meat and Livestock Australia has launched a new information resource for drivers and workers in the livestock transport industry, known as the MLA Transport Hub.
MLA consulted heavily with the Australian Livestock and Rural Transporters Association, operators and other relevant industry bodies to launch the service.
It says it will help to unify rules and guidelines across the industry to provide the best outcomes for the animals being transported.
“Transporting and handling livestock is a specialist task and one which the whole supply chain relies on to be performed safely, efficiently and professionally,” says ALRTA vice-president Athol Carter.
“Well planned and managed livestock transport delivers the best results for people and animals, higher profits and ensures the sustainability of the industry.”
MLA project manager Sharon Dundon says the information hub will be continually updated with new information for drivers and workers who work with animals, giving them transparency and a source of information for the industry.
“There’s nothing that exists that pools and brings all that information together,” she explains.
“This ranges from practical hands-on information to scientific information.
“A core part of the hub will be information around preparation for livestock for their intended journey and all the things you need to consider.
“We’ve been working with the Australian Livestock and Rural Transporters Association and TruckSafe, as well as operators that do livestock transport around what things they consider as best practice.”
UD Trucks is celebrating the 20th anniversary of its popular Quon model, first introduced in 2004.
As the successor to the renowned BigThumb model, UD says the Quon set a new industry benchmark through its integration advanced technologies and world-first innovations.
“Bringing the Quon to market 20 years ago was driven by UD Trucks’ Better Life purpose, enabling us to deliver a truck that’s better for people, our planet and for business,” says UD Trucks Australia vice president Philippa Wood.
“Quon has been at the forefront of addressing evolving challenges, setting new standards and delivering exceptional performance and success to our valued customers
across Australia – and many other markets worldwide.
Quon range to date and we will continue to go the extra mile and
The Australian Livestock and Rural Transporters Association and TruckSafe are developing a new Animal Welfare Accreditation program for the safe road transport of livestock. It will be developed in partnership with National Transport Insurance and will aim to support consigners, transporters and consignees meet their driver and animal welfare obligations.
Smith says the agreement has been reached after several months of consultation.
“This is necessary given the importance our members place on the safe and humane transportation of animals,” she says.
“It is an exciting time for ALRTA and its members, having developed the original TruckCare accreditation scheme that eventually formed part of
MAN Truck and Bus is taking an ambitious step forward in its truck production, announcing its intention to launch a series of hydrogen combustion powered trucks in 2025.
By 2025, this initially planned series of around 200 MAN hTGX units is expected to be delivered to Germany, the Netherlands, Norway, Iceland, and selected non-European countries.
The company says that this model will provide a zero-emissions option for transporting heavy freight across the construction, tank transport or logging sectors.
The initial axle configurations of the MAN hTGX, 6×2 and 6×4, are expected to allow for high payloads and maximum ranges of up to 600 kilometers.
The H45 hydrogen combustion
engine used in these trucks will have a power output of 383 kW or 520 hp. Refueling the vehicle with compressed hydrogen (CG H2) at 700 bar and a tank capacity of 56kg should take less than 15 minutes, MAN says.
The Mercedes-Benz eActros 600 has begun its gruelling journey across Europe, as Daimler Truck undergoes its ‘most extensive truck test run’ in the company’s history.
Two flagship electric eActros 600 are travelling across more than 20 European in a test of the capabilities of electric batteries for long haul trucking. Both models will be completing 13,000km each, towing 40 tons total.
Head of global testing at Mercedes-Benz Trucks Christof Weber says the company is looking to improve its knowledge of the wide range and routes and climates that a long haul electric truck will face.
“We have put various prototypes of the eActros 600 through their paces over the last few years,” he says.
“Whether in the North of Finland or the South of Spain, the vehicle has long proven what it can do. With series development, we are now on the finishing straight.
Daimler wants to prove that electric trucks can handle the demands of long haul trucking, which could not only be applied in Europe, but in overseas markets too.
Daimler Truck is rolling out the first electric trucks in its new RIZON Truck brand, sending out an order to several companies across California.
The all-electric US class 4 and 5 trucks ‘address a diverse range of customers’, Daimler says, as it looks to continue to develop its commitment to sustainable transport solutions.
While there are still more trucks on order, this batch of 20 e18L RIZON trucks will be delivered to LA Sanitation and Environment (seven trucks), Diamond Environmental (four trucks), Ecorecycling (three trucks), Velocity Truck Rental and Leasing (five trucks) and Goodwill Industries of San Diego County (one truck).
“I’m very excited the first RIZON trucks are now in operation,” said Andreas Deuschle, Global Head of RIZON Truck.
“Our all-new RIZON trucks inherited all this expertise which results in a very mature system: innovative eAxle concept, latest safety features, a wide variety of body applications, and a flexible battery concept.”
Daimler Truck Australia Pacific has opened a new parts warehouse to support its Mercedes-Benz, Fuso and Freightliner truck brands as well as parts division Alliance Truck Parts.
30,000 square metres in size, the facility is based in Truganina, west of the Melbourne CBD. It had been used previously as a shared facility with Mercedes-Benz passenger cars.
Daimler Truck Australia Pacific CEO and president Daniel Whitehead says that the new warehouse will give Daimler customers increased service and will also meet the company’s future sustainability needs and goals.
“This dedicated truck and bus parts warehouse is at the centre of our commitment to our customers across Australia and New Zealand,” he says.
“It was a great opportunity to specify a design that incorporated a raft of environmental elements ranging from double-glazed windows to an impressive solar power array.”
National logistics company Allied Express has enjoyed Isuzu’s offerings, which have helped its fleet offer the versatility it needs for a number of job.
Managing director Michelle McDowell says that while there isn’t necessarily a perfect delivery truck, Allied’s subcontractors seem to prefer the fleet of Isuzu trucks that the company can offer.
“Our fleet consists of a wide variety of trucks, because we do such a gauntlet of different delivery types,” she says.
“Reliability and presentation are very important for Allied Express as our customers put their trust in us to deliver the product on their behalf… it is important for all drivers to keep their vehicles well-presented and for them to be proud of their work.”
$17 million of funding is being put towards five new rest area projects in a joint effort from federal, state and local governments.
Rest areas will be located on the Barrier Highway in South Australia, Newell Highway and Sturt Highway in New South Wales, and in Pingelly, Western Australia.
“The federal government’s Heavy Vehicle Rest Area initiative aims to increase heavy vehicle user safety and productivity through vital new and upgraded rest areas across their journey,” says chair of the Heavy Vehicle
Rest Area Steering Committee Glenn Sterle.
“We want to keep our truck drivers and communities safe and these new and upgraded rest stops will help drivers reduce their fatigue as they keep goods moving across the country.”
These projects will include the construction of new rest areas with dedicated slip and turning lanes, shelters, landscaping, and connecting footpaths, as well as the upgrade of existing ones from light to heavy vehicle classification with all-weather pavement, solar lighting, and amenities.
Hino launched its new zero emissions truck brand, Tern, at the ACT Expo in Las Vegas as a part of a $3 billion partnership with zero emissions technology company Hexagon Purus.
They also unveiled the inaugural vehicle model in the RC8 battery electric Class 8 tractor.
Alemlube Automatic Lubrication Systems next level greasing allows you to:
• Eliminate manual greasing
• Stay on the road
• Deliver on time
• Spend more time doing your own thing
The semi-tractor uses Hexagon Purus’ years of zero-emissions drivetrain development for heavyduty trucks and represents a different option for fleets.
The new vehicles will be manufactured in Hexagon Purus’ new facility in Dallas, Texas, with the RC8 scheduled for serial production later this year.
The model is built on Hino’s XL Series 4×2 chassis and is equipped with Hexagon’s zero-emissions technology, including proprietary battery systems, auxiliary modules and power modules.
The vehicle uses a US assembled Hino chassis, an e-Axle from Dana and Panasonic Energy battery cells.
There are dozens of smart new road transport and distribution operations popping up around Australia and many are moving away from the traditional trucking model and finding new 21st century business models. PowerTorque visits one of them, Motus Transport in Sydney.
The way to develop a new
currently working, then talk to the end user, the customer, and look at the business from their point of view. This is what happened for Andy Harris and his wife Emily.
In 2016 the operation began with Andy hiring a van and Emily processing orders from home. The growth in the intervening years has seen the fleet grow to over 70 vehicles transporting craft beer and other beverages across a large area of NSW and SE Queensland. The business has two warehouses in Sydney and one in Brisbane, as well as warehouses in Canberra, Newcastle, Coffs Harbour and Byron Bay.
Andy says that Motus Transport’s aim is to act as an indispensable partner to customers and an extension of their business, by simplifying the process of transport and delivering great service. The Motus team are a close-knit team of diverse people, dedicated to this vision and share a love for good beer (beverages) and great people.
“We started really small, I was driving a truck myself and then one person said, ‘we’ve got a brew coming out, on this date, you need to have a warehouse’,”says Andy. “I just hired a truck, then went from there.”
The service Motus offers to the brewery is handling all the warehousing and distribution for craft brewers, as beer comes off the end of the production line. The trucks either pick up from the brewery or the brewery delivers it to the Motus warehouse.
It is then stored in a large cool room. It’s not just beer, it’s also sparkling water and and other beverages, delivered on their behalf. Trucks run all around Sydney, to Canberra, Newcastle, Coffs Harbour, Byron Bay and SE Queensland. In terms of storage, they have10,000 square metres in Sydney and another14,000 square metres in Brisbane.
“This year is a bit of a settle down and consolidate, and just make sure that we’re going to get everything right,” says Andy.
Motus means to move in Latin, and the logo includes a wing, which derives from Mercury’s helmet (Mercury was the Roman god of speed). The recently purchased Hino 300 Series hybrid trucks are named after Greek or Roman gods.
Distribution for the alcohol industry was not Andy’s first career choice.
“I said I would never do transport,” says Andy. “My dad owned a transport company here in Sydney. He owned that business and I’d worked in it when I was younger. It was a taxi truck business.
“Later, I went to uni and then I actually got into the alcohol industry, I left my family business in transport and then worked in the alcohol industry for 15 years. I was in sales and marketing and I was once a brand manager for Bundy, looking after key accounts. I met my wife on the first day in the industry she worked in safety, in her
uncle’s pub. Emily was managing the pub while at Uni, then worked in Safety for the like of Kennards Hire and Coke.
“I saw that in the alcohol industry, they’re all complaining to me about transport. I thought, it’s just got to be done better. Now, we’re kind of breathing fresh air into transport. We’re big on customer service, we’re big on our own staff, and the environment is something that you have to be good to. We want to make sure that we do the right thing and hybrids are the first step into that and it’s a relatively low risk. It’s not a massive capital outlay.
“When you’re in it, you can sort of pick where it can be improved. My real customer is pubs, clubs, restaurants. I tell the beer suppliers that we are an extension of their business and make sure that we do what their customers tell us. All of our drivers are a customer service person.
“You’re told when you’re going to deliver it, it’s got to be there at four
and if it’s not there at four, there’s a problem. It’s making sure that we work in with the venues and make sure that we’re doing our job, and if we are late, we tell them and say sorry. I think this industry has gone away from saying sorry, you know, yes, there is traffic and yes, there are other things and people do understand, you’ve just got to let them know.”
The business’ customers are mainly breweries, but they also include wineries or distributors of wine, or multiple beverages. There’s a lot of diversity in the industry, there are not big corporates like Coles or Woolworths influencing buyers. A business owner makes an individual decision on what they put on tap at their pub. They might have contracts with the big breweries, but they still support independent product.
Motus use the Carton Cloud system to run the distribution process, getting the idea from one of their customers, the Pirate Life brewery.
“We were working with them and they said that this software is great,” says Andy. “We found that Carton Cloud was very much tailored for us. It helped my wife get away from being on the phone all the time. I’d get home after doing deliveries and she’d be doing routing until 11 o’clock at night, before we got it.
“It helped with everything. A lot of transport companies only use about 60 per cent of the software and don’t use 100 per cent. Emily and her customer service team use 100 per cent of that software. It’s quite funny, Emily’s actually taught a lot of our competitors how to use that product. I don’t mind because I know that they’re never going to use it to the extent that we do. Technology is a great thing if you use it properly.”
In the past, Andy’s Dad’s transport business would supply handhelds to every single driver or inbuilt units. Now, drivers at Motus just use their own phone. The system will do invoicing every week which is auto generated. Every item in the warehouse can be barcode scanned, it can also bottle scan. Carton Cloud has evolved with Motus, after starting on
the Gold Coast in Australia. It is now in the US and Canada. Some of the bigger businesses Motus deal with are starting to use it for their own inventory.
We have a lot of younger staff and it helps that the hybrids look very good
then there’s a few semis (700 Series SS)
road, and we’ll start taking a lot more.
working on themselves at the moment.”
“My wife and I, we’re both 39/40, we’ve still got our first driver and he’s probably the oldest in our business at 54,” says Andy. “We do a bit of heavy lifting, the majority of the business, is younger. A lot of people talk about employing younger people.
“It’s just the way we treat them compared to other businesses. We work in the beverage industry. So when it comes down to it, it’s a fun industry to work in. We’re not delivering carpet, we’re not delivering cement, they actually like doing the job, they get to interact with venues,
The flexible and agile Volvo FM Electric. Lower sound and emissions. Excellent ergonomics and visibility. Designed for high-capacity grocery deliveries, container transports, refuse pickups and more within metropolitan areas. To simplify the transition to electromobility, the truck is offered together with solutions for charging, route and range planning and energy status.
Trucks. Driving Progress
pubs, clubs, restaurants.
“Sometimes some of the older drivers are stuck in their ways, but with young people, it’s really easy to train them our way, which we find quite refreshing.”
An issue in Sydney and Brisbane and in the bigger cities, is having enough room to park a fleet of this size, when industrial space is at a premium. So, if Motus drivers treat a vehicle like it is their own, the company will allow them to take it home. Semi trailers and the bigger trucks are parked at home base.
“We trust our drivers, and to be honest, I can probably name on the fingers of my hand when people have abused that,” says Andy. “We try as much as we can to work with them. If they live in the inner west of Sydney we try to have them finish relatively close to their home, which works for them. We implore drivers to talk to us, if they have to look after their kids, or they need to be at sports training or something, we try and work with them.
There’s also a lot of DC work for Motus, going into Coles, Woolworths, Australian Liquor Marketers (part of Metcash), Independent Liquor Group and Paramount liquor. The operation brings in liquor from it’s customers, and consolidates the loads for the required DCs. ALM sell to all the bottle shops and their consolidated loads are bigger than most.
The trucks all have compact small bodies, built to the Motus spec. The city trucks are lower roofed, with the height inside at 1.6 or 2.2 metres, so they can get into loading docks.The fleet have three body specs and they call them Mini Me, Medium Me and then Tautliner. Mini Me and Medium Me are the city trucks, pantechs. The truck bodies have signage on them for Motus’s customers on the van rear doors and Motus signage on the side.
“We try to keep our trucks for about four or five years, but we’ve had some massive growth,” says Andy. “We try to switch them out as soon as we can. There’s some trucks that haven’t done the kms because they’re only going
from here into the city and those we will keep longer. We just liaise with Hino and make sure they’re good. We’ve just had a few bodies redone, when they looked a bit tired after that length of time. We try to move them on and then get newer trucks. I don’t like having tired old trucks.
“For the next few years, we’ll work on our areas and build them out with other beverages, whether it be soft drink, or wine and spirits. We’ve got a bonded warehouse as well, there are opportunities. I see going further North in Queensland would probably be the first step. Wherever there’s an opportunity, we’ll just have
FAW JH6 PRIME MOVER meets your multifaceted needs. Achieve your smooth long-haul transportation.
FAW Truck products are exported to 80 Countries and Regions and has now landed to bring competitiveness into the Australian Market. It’s star product JH6 Prime Mover has a high end, bold and generous appearance. At the same time, multiple configurations of the vehicle are integrated to create the excellent performance. JH6 is known for its fuel efficiency, light weight and low maintenance cost, forging a high cost performance truck with high efficiency, reliability, safety and comfortability.
This year’s Rural Transport Rising Star, Luke Cannon, has come a long way in a few years from a livestock truck workshop, through truck driving, to handling the stressful role of organising loading and delivery for a busy livestock transport fleet like Fraser’s.
PowerTorque spoke to this year’s winner of the Rural Transport Rising Star Award, Luke Cannon, who was presented with his award at the combined Australian Livestock and RuraL Transporters Association and Livestock and Rural Transporters Association of Queensland conference, held in the Goods Shed, in Toowoomba Queensland.
“I’m born and bred in Warwick, Southeast Queensland, lived there my whole life,” says Luke. “At 19 years of age, I approached the Fraser family for a job in the workshop, at Frasers Livestock Transport. I started off in there for a few months. When I got a semi license, I started just helping them out where I could, running dog trailers about. My dad was a truck driver and he was in the workshop at Frasers, at the time.
“Eventually I thought I could stay away for a couple of nights and help out, jump from truck to truck and then eventually I got my own truck and I was driving full time. The workshop was a thing of the past, and then, after a few years, I finally worked my way up and got a brand new Kenworth T 659. That’s the ultimate for me, especially when you’re in your 20s.
“Then after about eight years of driving, a job opportunity came up in the office, so I went in there. I was always pretty handy on computers and with technology. I thought I could bring a few bright ideas to the office and asked if I could have a trial. I was working on the principle, that if it didn’t work out, I’d just go back to driving, which was no dramas.”
Since then Luke has stayed in the office. He started off helping out the operations managers, where needed, now he’s the sale yards logistics manager. His job is to take all the sale yard numbers each day and put together loads, taking in the various customer locations and preferences. Then he will allocate which truck does what load, generates and sends load plans and explains to the drivers how to load the livestock to suit the different destinations.
Not only do they need to have the right number of animals on the right truck, but also they’ve got to be loaded
the right weight distribution.
“Also some of the regular customers have got to take priority.” says Luke. “You want to treat everyone as equals, but it gets very hard there at times. Yes, it’s a big puzzle every day. You sit there in the mornings and wait for the sale yard numbers to come in and you’re all calm and collected, and they just hit you with big numbers.
“Then you’ve got to put it all together in the afternoon as quick as you can, so you can tell the drivers what’s happening and get them going, to give them the information. Then at night time there’s a lot of calls and there’s a lot of planning still going on, checking weights. Plus, there’s a lot of mornings where people can’t find cattle and can’t find paperwork. It’s a very stressful and demanding job, but it’s very rewarding, at the same time.
“You’re catering for drivers needs all the time. Drivers are restricted by their capabilities at times and you’ve got to allow for that. You have to think about cattle weights and who’s coming off first. It’s a very demanding job at times.”
Luke has got to work in a team with the other members of the operations group, who are organising the feedlot livestock tasks. These are booked in earlier, but have also got to happen at the right time with the right truck in the right location. For those dealing with the sale yards, the final decision is up
Frasers business and is still a vital cog in the organisation, still making up the bulk of the business.
“The fellow I work with mainly, is named Steve, he’s in his 40s. He’s drove for longer than I could imagine but he’s been in there about 10 years,” says Luke. “I work closely with Ross and Warwick Fraser, they oversee everything and just keep an eye on things. Other people just help us out where they can and when they can do.”
Having that period of driving experience beforehand means Luke has the skills to know what cattle should weigh, and if a problem situation arises, he has had the experience of handling it himself and knowing what to do, who to ring.
“Honestly, when I first walked into the workshop, I didn’t know where I was going to go,” says Luke. “I do like to be always moving forward and trying to keep building and get better, I just want to build on what I’ve got. I love to move forward and strive for better. You can always come back to what you’re doing, to come back to feeling comfortable.
“In high school, I never dreamed that I’d be doing what I’m doing now. Never even dreamed I’d get a new truck and be doing Western cattle work and road trains or anything like that, but the possibilities are endless.”
This year’s Australian Livestock and Rural Transporters Association Conference took place in Toowoomba, as a jointly hosted event with the Livestock and Rural Transporters Association of Queensland.
This year’s ALRTA conference took place in the Goods Shed event venue in Toowoomba, in a region which is home to the largest cattle feedlots in the southern hemisphere, with 617,000 cattle on feed in the local region and 45 per cent of the
“It’s an interesting time for transport and regional transport, at the moment,” said Rachel Smith, Executive Director of the ALRTA, at the event. “We’ve got a very interesting federal government that perhaps doesn’t necessarily look beyond the metropolitan borders.
“This is the situation we’re going to have to play to over the next 12 months, leading into the federal election. We are concentrating on the contribution that rural transport makes to regional economies and jobs, and stressing the need to adequately fund roads to provide safe workplaces for everyone in the rural transport sector.”
This national conference was the first opportunity for Mat Munro, the CEO of the Australian Trucking Association, to return to national conference of the ALRTA of which he was Executive Director for over ten years.
“It’s really nice to be back and good to see a lot of familiar faces and be amongst you today,” opened Mat. “The ATA is working on plenty of big ticket items, as the peak body representing 10 different member organisations. This is really broad mandate, but the first one I would mention is the industrial relations reforms.
“I was with ALRTA when we tore the Road Safety Remuneration Tribunal down the first time and, now, we’ve got something like it back. It’s a little bit different, but it’s also a little bit the same. It carries some of the same risks. We’ve worked really closely with our member organisations, it was a tricky issue for us, because across our 10 member organisations, we had five that were supportive of it and five that really didn’t want it to come back in any form at all.
“We worked with our members and with the government to try to find a way to bring this to function in a way that would actually work. The legislation has passed and we asked government for a whole range of failsafes, so that it can’t do what it did last time. If it gets it wrong, we
can stop it. Rather than, what we had to do last time, drive the trucks up the Parliament House and protest on the lawns to get rid of it.
“I’m hoping we’ve got plenty of other mechanisms to deal with issues this time around. We’ve got automatic understandings for industry associations be part of the consultations. We’ve got very long lead times before anything actually comes into effect, so we can analyse it and see where it’s actually going to have problems.”
The new rules have removed the Heavy Vehicle National Law and Workplace Health and Safety laws from the law’s remit to avoid any overlap in those spaces. If there are issues, the industry can reconstitute the Fair Work Commission panel to have a look at it. If all else fails, there’s now a role for the minister as well.
“If we had some of these those things the first time around, we might have been able to deal with the harm that the orders were causing, rather than striking out the whole legislation and tribunal,” said Mat. “There are things that the tribunal can now do, which will be a benefit.
“In payment terms, for example, we don’t have laws in other spaces that can really deal with those payment terms, waiting times and unfair contracts. There are things that we could do that would be beneficial for this industry, but we have to be really mindful of some of the things that happened last time, where it set minimum rates for one part of the industry and, basically, destroyed that part of the industry.
Eyes wide open, but there’s some opportunities here. We think, we’ve got the balance right this time around.
“The ATA is also looking at the sustainability issue, the low carbon transition and government has set pretty ambitious targets, like 43 per cent by 2030, and net zero by 2050. We can’t meet those targets on our own, we can contribute, but we can’t get there. Our best guess at this point is we might be able to go to between 12 and 15 per cent. We are just not going to turn the fleet over fast enough to meet those targets.”
The ALRTA is an organisation which works with politicians of all stripes, and continues to work to improve their understanding of rural transport’s specific issues. Most recently, the ALRTA has lobbied for changes to the industrial reform to take rural trucking into account
“We actually got concessions through working with David Pocock, and he’s a Teal, because we went and had very sensible conversations with him about the potential impacts of the legislation and the flow-through effects to Australian consumers, who are his constituents,” said Rachel. “There’s, opportunities to work with the government on issues such as rural road funding, ALRTA has been talking to the Australian Local Government Association about revamping the Rural Road Alliance.
“It’s highlighting that Australia is one national economy, we don’t necessarily have state borders or council borders
on the issues. How do we help the government solve some of those problems? Transport, fuel and others, we all have a role to play, because everyone’s hurting in the pocket right now. Whether it’s a business or a consumer.”
The ongoing shortage of resources to local government to achieve the result needed to maintain, let alone develop, our current rural road infrastructure, continues to be a major issue. The problem has been exacerbated by a number of weather events which put those resources under even more pressure.
Another issue which is exercising the dynamics of the relationship between the rural livestock operators, the local councils and the state authorities is effluent. All of the cattle in the feedlots and elsewhere in the vast area to the West of Toowoomba have to be brought towards the coast and get processed in abattoirs, creating environmental issues around the topic of effluent from the animals flowing from trucks onto the roads and roadsides.
Livestock industry lobbying for initiatives to enable the dumping of effluent from the trailers hauling cattle into facilities able to handle the effluent, have had little success. Local government and state government have made positive noises about addressing the issue, but very little of note has come of it. The responsibility for developing a solution to the issue is being passed back and forth between different levels of government. As a result very little progress has been made towards a practical solution.
“Local government can’t afford to do anything, except to advocate and we’ve done that quite strongly,” said Carol Taylor, a Councillor on the Toowoomba Regional Council. “Our group sent a letter to the federal minister and we got a strange reply saying the responsibility lay with the State Authorities for truck wash-down and also for effluent disposal facilities, and that’s where the responsibility lies.
“We need to advocate to the State Governments to find sites and we need to work together, both the livestock transport industry and local government.”
Navigating Contracts and Onboarding in the Trucking World is explained by the team at Clear Employment Relations Advice Team
If you’ve never had a legal headache, count yourself lucky. You never want to have one. In the fast-paced world of trucking, the importance of solid employment contracts and efficient onboarding processes is as crucial as keeping your rigs in top gear. Whether you’re managing a fleet of long-haul truckers or a team of local drivers, ensuring that your employment practices are watertight will save you time, money, and legal headaches down the road. Buckle up as we take a deep dive into the common contract pitfalls and the best practices for onboarding employees, aimed at equipping employers with the knowledge you need to keep wheels turning smoothly.
Common Contract Pitfalls
1. Ambiguity in Terms and Conditions: One of the most frequent mistakes is vague language. Terms like “reasonable notice” or “as required” can lead to disputes. Clearly define working hours, overtime expectations, job responsibilities, and termination conditions. Clear contracts mean no surprises.
2. Failure to Update Contracts: Employment laws and industry standards change faster than a trucker can finish a meat pie. Regularly reviewing and updating contracts is like keeping your truck serviced—it ensures compliance with the latest legal requirements and best practices. Outdated contracts are like dodgy brakes—they can lead to nasty legal prangs and misunderstandings. Keep those contracts fresh and roadworthy!
3. Misclassification of Workers: Misclassifying employees as independent contractors or casual workers can have serious repercussions. Ensure that the contract accurately reflects the nature of the employment relationship. Employees classified incorrectly can lead to liabilities for unpaid superannuation, leave entitlements, and even penalties from regulatory bodies like the Fair
Work Ombudsman. Get it right to avoid costly detours.
4. Inadequate Leave Policies: Trucking work often involves long hours and gruelling schedules. Make sure your contracts outline leave entitlements, including annual, sick, and long service leave. Don’t forget to build in notice and evidence requirements into your employee handbook to ensure you can manage those difficult staff.
5. Inadequate Overtime Policies: Trucking often requires flexibility and long hours. Make sure your contracts clearly state how overtime will be calculated and compensated. Do you just pay an all-inclusive rate? You better have an offset clause in there or you may get a nasty surprise – without this, it doesn’t count as overtime pay. Failure to comply with the Fair Work Act regarding overtime pay can result in significant financial penalties and strained employee relations.
So what do you need to issue your employees at the time of onboarding?
1. A contract relevant to their employment type (i.e. full time, part time, casual)
2. A copy of your employee handbook, which should outline your policies and procedures
3. A detailed job description
4. A copy of the Fair Work Information Statement – you must issue this by law – and make sure it’s the updated version!
5. A copy of the Casual Employee Information Statement (casual employees only)
6. A form requesting their personal particulars (name, date of birth, emergency contact details, driver’s licence details, bank account details and more) and health questionnaire
7. Tax File Number Declaration Form
8. Superannuation Standard Choice Form
9. Contracts, handbooks and job descriptions are business specific and you should chat to a
professional about these to ensure your business is protected. You can download a free resource pack with some helpful items here:
The strength of your workforce is the backbone of your business. By avoiding common contract pitfalls and implementing effective onboarding processes, you lay the groundwork for a stable and productive work environment. Remember, clarity and preparation are your best allies. Investing time in these areas will pay dividends in employee satisfaction, retention, and overall business success. So, keep the rubber on the road and your contracts airtight! Questions? Reach out to advice@clear-er.com.au
THE STORY OF THE TRUCK OF THE YEAR AUSTRALASIA 2024
Winner of the highly-prestigious Truck of The Year Australasia (ToYA) award for 2024, the X-Series is the most-tested Western Star ever. The X-Series boasts our legendary Star durability, features a powerful integrated driveline, an advanced safety package, and superior comfort – even in the most rugged applications.
The winner of the Truck of the Year Australasia 2024, the Western Star X-Series was a long time in the making. It’s here now and PowerTorque has looked into the origin story of this ground breaking range of trucks for the Australasian market.
TStar X-Series began back in 2014/2015, when the team at Penske Australia & New Zealand (formerly Penske Commercial Vehicles) first started looking at a model range to take the brand through the 2020s.
This is a story of bringing new levels of safety and efficiency to the brand, without compromising the qualities the brand had built on over the last 40 years, as the new trucks passed through the design process. The requirements included meeting the latest regulations which were expected to be mandated, as well meeting the expectations of the trucking industry in the coming decade.
Also included in the process were deliberations needed in starting work on any new truck, designing and integrating trucks for as many applications as possible and enabling ever more efficient logistics. It was also important to include the latest and greatest technology and design being developed for the Western Star brand by Daimler Truck in North America in
for the Australasian market.
At that time, when the design process began the date for the next round of exhaust emission regulations to be implemented had not been finalised, but the team also new it was inevitable. As it happens the design process was able to get trucks able to meet the ADR 80/04 limits well ahead of the mandated date for the introduction of November 1 2025.
There was clearly a need for a new engine platform and after treatment to meet the ADR as well as taking Western Star into the fuel usage levels being asked for by the trucking industry at this time. Any new driveline would also have to meet the durability expected in Australasian operations.
“Overall, we launched the X-Series with the goal of having the strongest and most durable Western Star truck to date,” says Kurt Dein, Head of Western Star Trucks at Penske Australia.
“Looking back, we had launched the Constellation from Western Star back in 1998 and had gone through three
days of C15, S60 & Signature ADR80-01 engines through to current ADR8003 which saw the introduction of the Detroit DD platform back in January 2011.
“By that point we had exhausted the architecture and packaging to reach the point where the Australasian market, and the global market was going for the next round of emissions. The next Detroit platform under the Daimler portfolio would include safety systems and we just didn’t have the architecture to run those systems and things like the multifunction steering wheel capabilities, and so forth. We could see where the fleet volume and demand was going, looking for improved emission platform whilst maintaining a very compelling TCO offer.
“The Western Star engineering team came out here to Australasia, and we created that product concept, made a roadmap, and a product definition. We needed to identify what segments we were playing well in, and not so well in. What do we
need from a driver’s fit, from a safety fit and from a fuel packaging fit point of view? Then there was bumperto-back-of-cab (BBC), because 2013/2014 had been the era of truck and dogs, when they went from 52 to 57.5 tonne GCM.
“I was lucky enough to be part of that conversation with key customers, when I was part of a dealership. It was asking, what’s the market after today, and what’s the market need for the future? What key milestones do we need to achieve? If you look at Western Star, we’ve always had a very strong truck, but a heavy truck. We’ve always been a very strong build. The frame rail has been key. We’ve had a steel cabin, we’ve had a big solid brass core cooling package and big stainless steel air cleaners and we’ve never lost a truck because the frame snapped.
“But when it comes to safety, innovation and efficiency, how do you make that lighter? How do you make it stronger? Can you make it last? It was really looking at the frame and working from the frame up on X-Series. It was about achieving the strongest frame rail that Daimler has ever put into one of its products.”
The engineering team worked to improve the cooling package performance in a few key ways. They optimised the radiator packaging and placement to handle the increased heat from lower emissions components. The radiator needed to remain being fitted relatively high for protection and also achieving the high cooling requirement needed.
The team in Australasia worked on extensive testing and simulations, alongside the Western Star team in Portland in the US, to ensure the cooling system could handle the demands of a 220 tonne GCM truck. When working on the cooling package for the 49X, the introduction of the ‘Power Hood’ ensured high airflow and required size of radiator was achieved. When it came to the 48X, the cab needed to be lifted to achieve the same cooling package of the 49X and house the DD16 under such a short BBC configuration. During development, testing of the
cooling package performance in extreme environments was vital, in conditions like the Australian outback to ensure durability.
Overall durability was paramount, with the team noting past issues with turbo failures and overheating that other brands had experienced.
Truck dimensions are also an important factor in suitable design with bumper to back-of-cab fit and space to improve airflow and heat dissipation for the engine and emissions components taken into consideration. It wasn’t just about lighter and stronger, it also had to meet wheelbase and packaging requirements. Square fuel tanks were also a necessity, so
the frame in the right locations to support the tank package and ground clearance.
Western Star has always had the bonnet mounted off the chassis rail ensuring stability in the bonnet and enhancing the durability in the bonnet. The bonnet on the X-Series was to be made of resin to take the weight out of it, but also make it stronger.
“In North America the Western Star is specifically designed and targeted for the vocational segment,” says Kurt. “The conditions of the average vocational market truck in the US is like, ‘welcome to Australia’, and that segment was absolutely achieving, they were mounting equipment off the
logging applications and those heavy mining applications over there. They’re really custom built over there, they don’t have 1000 truck fleet orders of that cookie cutter truck. X Series, predominantly in the US, in the vocational segment, built in Portland, Oregon, and that’s where ours are built.”
The CANbus now fitted in the Western Star brings the brand right up to date, in terms of electronic architecture. It offers a new level of sophistication, the system is programmable and will enable body builders to interface effectively with the truck. It also means the large bank of switches can be utilised for many of the independent body control functions without the need for the body builder to cut and shut anything in the wiring harness. The solution is a simple plug-in interface.
“We can program the functionality in this system, it’s dealer supported and we can even have the chassis rail to suit the body builder requirements in Australia,” says Kurt. “Going forward, it’s exciting what we can offer in that piece.”
Sophisticated electronics and design, alongside the right power and torque figures, fuel consumption and durability was also going to be
Australasia, it’s about getting the requirements in early and making sure that the teams which are designing the driveline for a global market are taking the Australasian requirements into account,” says Bob Gowans, Detroit Business Manager at Penske Australia.
“We feed those requirements in early, seven or eight years before we see the first real trucks. That means that our specifications are on the slate, alongside the Canadian, Mexican and North American requirements, and taken into account. On the engine side, it’s been known for a while that, at some point, the Australian emissions regs would get tightened up. Although we didn’t really know when, it was pretty much a shoo-in that it was not going to be something bespoke in Australia and it would follow the usual route for exhaust emissions legislation.
“On the engine side, the platform since 2007 has been designed to take into account exactly where we’re going emissions-wise in the long term and it was designed with that in mind. We made the block stiff enough to cope with high compression pressures and made the cooling system capable of removing the waste heat that you end up with in certain operating modes.”
“In the US there are three versions of DD13, there is a low revving fuel saving version, an extreme fuel efficiency engine and a fuel efficient
needed for, what in the US they’d call,
This means the X-Series here can get the range of ratings needed out of the 13 litre to be able to perform in trucks from rigids all the way up to B-double operation with a mechanically identical engine, with the same injectors, turbo and other components across the engine regardless of rating.
“In the US the DD16 is not seen as a normal line haul engine,” says Bob. “It’s used for what the US regards as extreme applications, heavy logging, heavy haul, moving large pieces of machinery around. That’s what it’s used for over there. Over here it’s an absolutely normal engine to use and it puts you right up there with the most fuel efficient engines on the market, that can cope with those weights.
“It’s only with the introduction of X-Series that it’s available in the Western Star and that engine is designed to give really good usable amounts of torque and power. The feedback we’ve had from customers that the DD15 is great on fuel and it’s reliable. However, when you move to the DD16, which is a very closely related engine, you’ve still got the fuel economy in a newer design. It’s still got the reliability we’re not over stressing the engine. We’ve got more power out by adding almost another litre of displacement to the engine.”
@ 1,800 RPM
1,850-2 ,050
lb-ft @ 975RPM
Extreme duty and heavy hauling for your biggest jobs
Detroit’s most powerful truck engine ever, the DD16 boasts up to 600 horsepower and 2,050 lb-ft of torque. The big bore workhorse provides efficient and dependable power and performance without compromise.
Advanced combustion and aftertreatment technology exceed future emissions requirements whilst retaining exceptional fuel efficiency and uptime.
This power, performance, and efficiency are backed by the most comprehensive warranty and extended coverage packages, ensuring the highest level of support for our customers.
When you buy a Detroit product, you’re buying billions of miles of engineering excellence. Tried and true, Detroit engines are built to ride the roughest roads.
With Detroit, there’s no compromise.
The ESOC875E electronic commercial vehicle oil change system, developed by ESOC in the USA, is transforming the commercial vehicle maintenance landscape in the technological sense.
This system not only reduces labour time and costs significantly but also moves towards greater efficiency and sustainability in commercial vehicle servicing.
Designed to complete oil changes within 10 to 15 minutes, the ESOC875E allows technicians to allocate their time more effectively, marking a pivotal advancement in workshop productivity and environmental stewardship.
Crucially, the system’s fully electronic and metered oil dispensing feature ensures precise control over the oil change process, further enhancing its efficiency and reducing waste.
One of the most appealing things of the ESOC875E’s appeal is its reduction in labour time and costs. Capable of completing oil changes for trucks and commercial vehicles in 10 to 15 minutes, it frees up technicians to perform other tasks, enhancing workshop productivity.
This efficiency is not only about speed but it represents a commitment to ESOC’s mission of developing ‘Green fluid exchange technologies.’
These technologies are designed not only for preventative maintenance of both heavy and light-duty engines but also to minimise truck downtime and ensure the procedures are as quick and easy for the technician as possible.
The universal attributes of the
ESOC875E system is one of its key strengths. With support for multiple truck brand fittings, it has compatibility with a wide range of trucks and commercial vehicles. This versatility ensures that workshops can use the system on a variety of vehicles.
From a technical standpoint, the ESOC875E can exchange approximately 38 litres of oil in 10 to 15 minutes. This is a significant advancement for commercial vehicle servicing workshops that are constantly seeking ways to achieve real cost savings and improvements in time-saving equipment.
The system’s innovative features, such as automatic oil sampling and patented spill-free quick-connect fittings, utilise the latest technology to speed up oil extraction and refilling processes, thereby increasing speed and productivity.
From purging waste oil and refilling with new oil in approximately 15 minutes, requiring 100psi compressed air, to its onboard fluid management system and USB for data transfer and saving, the system is designed for efficiency and ease of use. It also features an onboard computer that records vital information such as vehicle ID, mileage, amount of oil added, and technician ID, ensuring thorough and accurate maintenance records.
The operating instructions
highlight the user-friendly nature of the system. From draining the waste oil to filling the engine with new oil, the process is streamlined and straightforward, reflecting a design that prioritises ease of use without compromising on functionality.
The ESOC875E represents a significant forward leap in commercial vehicle maintenance technology reducing labour time and costs, offering wide compatibility, and incorporating advanced features that ensure speed, efficiency, and environmental responsibility.
It stands out as a perfect addition to any truck or commercial vehicle workshop, changing how maintenance is performed, and offering a more efficient, sustainable, and productive future.
· Protect equipment and boost productivity.
· Covers a diverse range of needs, from trucks to extractors.
· Clear communication and capacity management for efficient operations.
· Global standards with local expertise across Australia and New Zealand.
· Minimise wear and enhance efficiency.
Wood and log hauling is specialised work, and requires safety solutions that may not be otherwise seen in other areas of the trucking world, Alex Catalano investigates.
Nestled out in the middle of Victoria’s picturesque Gippsland region, ANC Forestry is a logging and transport business that operates across all of Victoria, up to New South Wales and even in Tasmania. Its headquarters are just a short five-minute drive out of the main drag of Morwell, and houses its comfy office space, a sizeable workshop where mechanics work away on the trucks and equipment
and a yard filled with resting vehicles and timber as far as the eye can see.
Run by managing director Daryl Hutton, ANC has been in action for 16 years, having grown from a fleet of just five trucks to now 35 along with 60 staff.
It first started in harvesting wood in steep country with cable logging on contracts before moving onto more hauling work, as opposed to harvesting.
“Native logging has been closed down in Victoria, so we’ve had to diversify into carting for other people and products,” Daryl explains.
“We’ve also diversified to rock trucks. We’ve got four rock trucks and trailers, and walking floors. We’re starting now on our next processes, on building other configurations that can cart different product as well.
“We try to innovate and keep
being proactive moving forward.”
Those big logging and hauling jobs call for powerful vehicles, which ANC is in no shortage of.
Walking through the workshop and the yard, it’s hard not to marvel at the sheer size and scale of the Kenworthheavy fleet – especially when they’re loaded as high as they are.
“I’ve only brought new Kenworths for the last 15 odd years,” Daryl says.
“We’ve acquired Volvos and other trucks by acquiring other fleets, but I haven’t bought them new. Kenworth is the truck of choice for logging. It’s tough and robust.
“They have become very expensive. The rates in forestry haven’t increased to keep up with that. Things have to change.”
As challenges in the forestry game continue to arise, ANC has had to continue to diversify its business.
The rock trucks are one part of it, giving the business options in the types of jobs it can take on.
“We’re in difficult times of transitioning out of native forestry into other haulage opportunities. We’re going to be fine, and we’ll make it, but we’ve got to truck smarter,” Daryl says.
“Transport is competitive, and so to keep up with prices, to where things need to be, you can’t just pass the costs on, you have to keeping moving on.
Daryl leans heavily on his prior experience in logging haulage in New Zealand, where he worked for 15 years before making the move over to Australia.
There are different issues which arise across the ditch compared to here, he says. Kiwi operators have to worry more about their road tax, which has to be paid upfront.
They’re also generally unable to be as efficient as logging businesses here, which are able to carry greater
five axle dog trailer still only carts 58 tonnes, whereas we’re at 67.5.
“Our axle loadings are greater, so the trucks are more than capable of carrying it. New Zealand’s log hauling fleet is 90 per cent truck and dog.
“Their terrain is pretty tough and their main roads are tough. Very windy and so many opportunities for a driver to get it wrong.”
Daryl has recently gone through the
Out here, standard is just the starting point. We believe in pushing the limits. For over 60 years, Mack Trucks have outpowered, outlasted and outperformed to earn their best-in-class reputation. With new upgrades to horsepower, fuel-efficiency, driver comfort and safety, Mack is setting the standard once again.
the workshop installing it, his own mechanics are now trained on how to do so, with one truck currently going through the process.
“In our twin steer with the five axle dog trailer, it’s a PBS vehicle which is fitted with PRIMAAX air suspension on the rear of the truck, and that was for payload height,” Daryl explains.
“We ran it initially without Base, but we’ve now put Base Air in it. I took it loaded to Mansfield one day, and as I was driving along the long straight I noticed the Base Air works so quickly that you’re not constantly turning the wheel to compensate for the camber changes in the road.
“In a log truck with a high payload, if the road leans slightly to the left, the truck’s going to lean over. It reacts so quickly you don’t need to move. You’re holding the wheel dead straight. That was when I became a true believer that Base Air makes a difference.
“The fact is, that it’s taken the wag out of the dog of a five axle dog trailer, which is quite long, it just sits rigidly behind you now.”
Michael van Tilburg is one of ANC’s drivers, doing around eight to 10 trips
up and back to the local quarry at Hazelwood, carting rocks in his Volvo FMX, configured as a truck and dog.
We had the chance to jump in the truck with ‘Mick’ as he completed one of those trips, and the stability of the trailers was immediately noticeable.
“Even when I’m throwing the truck around the roundabouts, the trailer just sits there,” he says.
“I’ve been in the Volvo officially since the second week of January. The Base Air in it is working all the time but you can’t hear it. It’s pumping air here and there. You don’t see it on the air gauge either when it’s controlling air.”
Warwick Blines has been driving for ANC for seven years, almost always in one of the Kenworths carting logs.
On this day he was fully loaded with a massive stack of pine, locally near Strathford. He’ll run to the mill and back, and head out as far as Melbourne on occasion.
His truck has now been fitted with the Base Air suspension system, which he sees as a big upgrade.
“Every time I saw Daryl after he put the Base Air on I told him how good it
was,” Warwick says.
“Fair dinkum, it felt like a different truck. Just unbelievable. First of all it stays flat. The truck doesn’t move. My sticker says ‘straighten out the road’, it does.
“You don’t get that awful feeling going around corners. Some roads are off camber, and I’m very low tolerance to that. I won’t speed. But if the cab tips over, you get that feeling. It settled the trailer down. I try loaded on a flat road, just turning the steering wheel the dog would swing out on the other side of the road then swing back then come straight.
“When they put Base Air on, the trailer swings out and when you turn back it just stops behind the truck. When it’s empty, it feels like a race car because it stays flat.”
Daryl stresses that ANC prides itself on the safety that it offers its drivers on the job.
In 2015, the business was recognised with a WorkSafe Victoria Award for Safer Logging Systems after developing a restraint system solution alongside a group of other foresting
and trucking companies.
When carting such specialised material as logs, these innovative systems have to be in place to keep everyone safe in the workplace.
“Our local area is unique for slippery logs at certain times of the year. We had an issue with log movement in transit,” Daryl says.
“So we got together to fix the problem by changing the restraint systems by using double purchase systems and the air winches which were available at the time.
“It’s doubled our restraint and it’s mitigated the logs falling off. We haven’t had loads shifting, in however many hundreds of
thousands of loads since.
“We made chain hangers that are spring loaded onto the side so we can hang the chains and the loaders can chuck them over for the driver. The driver doesn’t have to be worried about shoulder injuries.
“The flipside of that means we’ve got guys in their 70s still working for us. There’s no manual handling.
“We had one guy retire on 77, and he had carted logs for 60 years. It was the only product he carted for his whole life.”
Similarly, Daryl believes the Base Air systems offer his drivers considerable safety benefits first and foremost.
“As a fleet owner, it’s another tool that I can provide to get the drivers home safer,” he says.
“We do everything, log trucks are fitted with every safety device you can think of, but the industry still has the odd rollovers. That has been mitigated by EBS on trailers, but there are still times when people get it completely wrong.
“You want to give them the best fighting chance that’s available. For me I find that Base Air ticks one of those boxes.”
It’s a perennial question on many and varied topics, but the question, does size matter? is also relevant in the truck world. There’s cab size and engine size and many other things to consider, but for Tim Giles, or any driver, cab and engine size do make a difference.
20 years is a long time in the world of trucks and trucking.
It is also the time between my very first drive of a MercedesBenz Actros with a MegaSpace cab and my most recent experience with the latest version of the Mercedes-Benz Actros GigaSpace truck.
It’s rather easy to say that the difference between the two is pretty much chalk and cheese. Probably the most important difference between that truck 20 years ago and the one which PowerTorque magazine is testing now, is the fact that this truck is definitely fit for purpose, whereas there were a lot of question marks about the truck which was tested in 2003.
It’s not a good idea to dwell on many details of that MegaSpace, which was brought to Australia for
the 2003 Brisbane Truck Show, apart from mentioning that it was very tall. It had quite a big powerful engine and it had been designed for the major motorways of Europe. As a result, running it around the rough, badly maintained highways of Queensland was a bit of a queasy experience with such a tall cab swinging from side to side as well as forwards and backwards.
The engine was of course the Mercedes-Benz V8 engine which was a great performer, but it drove through a so-called semi automatic transmission which left a lot to be desired and certainly did not come into its own on the climb up Cunninghams Gap towards Warwick.
Thinking back on that test drive, it was a completely different experience
in contrast with spending some time with the GigaSpace truck which was brought over to the 2023 Brisbane Show. The contrast couldn’t have been greater, with this latest truck being a fit-for-purpose design which could suit many tasks in the Australian transport industry, and do a good job
One of the first things anyone would notice walking up to this truck is the sheer height of it. This is a tall truck, which may have a long climb up into the cabin, but it has that feeling of spaciousness once inside the flat floored cabin.
The other size we were looking at is all about that other major component to truck driver satisfaction, engine power. In this case we are dealing with the latest 16L produced by Daimler for Mercedes, the OM 473 six cylinder
in line diesel engine, which has been developed from the global engine of platform developed by the Daimler organisation in the 2000s to go into all of its heavy duty vehicles, across three continents.
Here we are dealing with an engine which provides the driver with 630 hp under the right foot and 3000 Nm (2213 M) of torque to get the job done. This is a well proven engine, which has seen the Mercedes Benz market share rise due, mainly, to its fuel consumption figures and economic performance.
The difference between that first experience 20 years ago and this second experience is another major component which has transformed the truck offering from the whole Daimler
organisation, globally, and that is the Power Shift AMT. In this particular case it’s the 12 speed power shift running through a 1:3.583 rear axle ratio which gives us 1436rpm at 100 km/h out on the highway.
Where the transmission in that 2003 truck was plodding and not very reactive, this latest iteration of the AMT in the Mercedes-Benz is smooth, reactive, easy to use and reliable. The development of AMTs, as a whole, in the intervening 20 years between these two test drives has seen transmissions become much less of an issue. Where, in the past, we would need to discuss them thoroughly during these test drives, now, the population of new truck AMTs has reached a standard where, quite often, the driver doesn’t have to think about the transmission
because they can trust it to do the job without their interference, most of the time.
Cab suspension has come a long way in the intervening 20 years since that first experience. They are much more sophisticated and much more able to handle different road conditions in different situations. It’s no longer a one-size-fits all design aimed to avoid making the German truck driver on the autobahn spill their coffee, but make the driver on the Warrego Highway slightly seasick. Daimler now thinks of itself as a global truck manufacturer and designs components like cab suspensions to suit the many and varied applications into which its trucks are placed.
These sort of cabins are now accessible for operators in Australia. That’s not to say they all function well in all tasks, because the sheer physics and mathematics around such a tall cabin with such a small footprint is hard to overcome. The dynamics are always going to make cab sway more prevalent than on a conventional, truck with a lower cab fitted behind and below the engine.
On this particular drive we took the GigaSpace 630 across from Melbourne and down into Adelaide. The road between the two capitals is not bad, but it’s not that good either and the truck coped easily with the lump and bumps with which it was presented.
For Australian truck drivers a flat floor is not a big deal, but space is always a big deal. The cabin is fantastically tall, but it’s not fantastically deep, therefore you don’t get that one metre wide bunk.
Another revelation on this drive was the MirrorCam, which Daimler introduced a few years ago. It has had a mixed reception, but we are told that the latest version is a step up from its predecessor. To the casual observer, the actual screens, mounted on the A pillars and the outside mounted cameras look the same as they did before.
Like all of the latest developments, it’s clear the vast majority of the investment to improve the system would have been in the software. The stalks which the cameras sit on are actually shorter, and the camera actually sits closer to the cabin than it did before. Daimler claim this means the view that you get on the screen is more like the one you would get on the mirror.
Driving through rain out on the highway was no problem at all, even when looking at vehicles overtaking or being overtaken. It’s surprising how quickly you get used to the fact that you’re looking at a screen and not a mirror. Also, it does have some markers on the screen image which the driver can actually change themselves. One can be placed at the point at the back of the last trailer, enabling the driver to gauge where a passing vehicle is. On the nearside, there is a redline which tells the driver
how far the front of a vehicle they are overtaking is from the MirrorCam. This makes life easy, telling the driver when it is okay to move across after overtaking.
As it is possible to move these lines on the screen, you could place something on the ground in view just past the rear of the trailer, then move the line to that position. This enables the driver to adjust for different trailer lengths. This should then increase the level of trust the driver can have in the system.
Once is Adelaide, it was dark and the busy traffic on Portrush Road was clearly visible in the MirrorCam screens. This iteration seems to be able to remove the glare which has been an issue. However, there was no opportunity to try and reverse onto a dock with a bright flood light to see how the system copes with that perennial problem.
The roof height inside the GigaSpace cabin does create a sensation of space, even though the length and breadth measurements on the cabin are the same as all Actros cabs. There’s plenty of room above the windscreen and it’s got cupboards directly above windscreen height and the one in the middle has got a microwave fitted in it. That’s two big cabinets and then one with the microwave.
This particular model has a double bunk. The fold down upper bunk is smaller than the lower one, but looks big enough for an average driver. On the passenger side, there’s a small fold down desk/table directly in front of the passenger seat. On first sight, it looks a
bit flimsy, but in fact, it holds up quite firmly and there’s no ‘bounce’ when typing on my laptop.
Underneath, the main bunk has room for two fridges or a fridge or freezer. This one’s got a fridge on one side and a big drawer next to it. You can lift the bed and get access into the side lockers. The side lockers are the standard European size single locker, but I’m 176cm tall and when I was looking to see if there was a bar for the jack, to test the trailer tyres I couldn’t reach into the back of the cabinet, because the cab height means the locker is mounted that much higher.
The dash is the familiar Benz design, which has remained pretty much the same, with the odd tweaks here and there added over the years. The main difference in these more modern trucks is the growing size of the screen facing the driver on the central binnacle. The screen is even larger, directly in front of the driver with a typical array of digital instruments.
This is a 2020s truck, so the keys just have to be inside the cabin for the engine starter to work. There’s a digital dash and a touchscreen to the driver’s left to interface with the entertainment and information system.
The full panoply of safety systems are available and using them does make life a little easier. The adaptive cruise control keeps a safe distance to the vehicles ahead. The only thing the driver really needs to do is keep an eye on the actual speed. If the vehicles in front slow down, the truck slows with them. Then it’s time to intervene, take over control and move up to overtake the slowing vehicles, then back again to a comfortable cruise.
The truck also has an active steering control with an indication on the screen of where the system will try and hold the truck, in relation to the white lines on the road. The default position is centrally in the lane. However, most truck drivers will prefer to be closer to the fog line than to the central white line.
It is possible to adjust the system to place the truck in your preferred position. For myself, I aim to have the rear trailer wheels about 300mm from the fog line. A bit of adjustment on the screen got the truck in the right place. Making this adjustment stops a lot of the little adjustments happening, which the system will try to make if the driver is steering away from that central line
It’s surprising how quickly you get used to the fact that you’re looking at a screen and not a mirror.
subconsciously.
If the truck wants to be on a different line to that preferred by the driver, the constant minor adjustments can be intrusive and, often, the reaction is simply to turn the active steering off. Adjusting it to suit driver preference leads to a much less irritating driving experience, but the controller needs some careful ‘stroking’ to get the positioning just right.
This is clearly a very modern truck with all of the gizmos, which are becoming ubiquitous. It’s also roomy spatially, but some would be disappointed with the bunk width. For such a high cabin, the visibility is
good. The bottom of the windows in the doors are around knee level and a well placed real mirror covers that blindspot directly in front of the truck.
The MirrorCam, on this trip, was effective and enhances visibility rather than detracting from it, with the caveat that reversing onto a dock at night was not part of the journey.
Pulling a loaded B-double over the Melbourne to Adelaide run with a 630 hp engine and smart AMT is one of those runs which this truck was designed for. The cab suspension is effective in damping down sway without compromising comfort and there are plenty of electronic toys to play with as the journey plays out
A new hydrogen waste truck shows just how the needs of heavy vehicle systems are changing and evolving.
The adoption of ‘new energy’ powered trucks, whether they be electric, hydrogen, hydrotreated vegetable oil or renewable diesel, is fostering in a changing landscape for manufacturers of everything that goes into a truck.
This includes Hendrickson, who create suspension solutions for a range of heavy vehicles, including most recently a new hydrogen waste truck in partnership with HDrive.
PowerTorque recently had the opportunity to tour Hendrickson’s Australia Pacific head office in Dandenong, out in Melbourne’s south-east, where we spoke to Andrew Martin, Vice President of International Operations.
The partnership with HDrive was built off the two companies similar ventures in China, which saw Andrew come into contact with CEO Ben Kiddle.
It is just one of the ways that Hendrickson is branching out into the realm of New Energy Optimised solutions, or NEO as it’s known across its product line.
The HDrive truck currently sports a PRIMAAX European configuration, with Hendrickson looking to supply other models of the suspension line including the Global Comfort Air NEO and PARASTEER NEO.
Andrew explains that developing a suspension for hydrogen vehicles comes with new challenges, including dealing with increased weight due to the additional load that a hydrogen fuel cell or battery adds on.
“Our NEO variants of our suspension are all highly optimised for new energy applications,” he says.
“You could pick any one of our suspensions, and the NEO version is tweaked to suit the uniqueness of the
vehicle.
“This vehicle is a collaboration with their factory in China and ours in China. Our team in this market do the same thing from an application engineering and optimisation engineering perspective.
“We’ll going back to with a clean sheet of paper and ask ‘what can we do, what can we engineer?’ knowing what the unique operational environment and market is, what the
conditions and fleet operations areis.
“Then there’s a mini-design process and to see how close to the pin our existing product is. We then close that gap with the local engineering to bring it on target.
“That could be structural changes, a shift in the suspension’s ride and handling or damping characteristics. There’s a lot of market knowledge and legislative framework knowledge that we bring. While we bring hardware, we also bring intellectual capability.”
One of Hendrickson’s tasks for the near future is creating suspension solutions for trucks that are continuing to change to the needs of the market.
Calls for changes to the Performance Based Standards (PBS) framework may usher in new requirements for suspension and similar systems, which Andrew knows they will have to be conscious of.
But with its advanced simulation tools, Hendrickson is able to look at how any changes to current suspension models or completely new ones will work before they even begin entering the production process.
This is in addition to the comprehensive testing that takes place in its Melbourne facility and abroad.
“The speed of the market change is one factor. The other is more around the legislative framework and the rate of change in innovation,” Andrew says.
“PBS in particular, the rate of
adoption and change of PBS and what it means.
“As you experiment with the number of axles, performance of a suspension, the handling characteristics, that has an enormous impact of the viability of an idea or the harpooning of it.
“We’re able to with our toolset and skillset, to help customers challenge the boundaries and push them.
“The volume and speed of the ideas and their implementation is extraordinary. I’ve been doing this for 28 years and I’ve never seen such a fast-paced environment.”
Other recent changes in the Australian trucking industry, such as the increase on width limits from 2.5 to 2.55 metres which came into effect in September 2023, also influence how suspension has to be developed.
Hendrickson works with its customers as they begin to change the metrics of the heavy vehicles they can develop, building custom suspension for them.
“Changes and increases to truck sizes are mostly about customers understanding,” Andrew says.
“That’s where the simulation tools become really powerful. We can float an idea or they can. ,Initially some of these ideas may seem a little and they can think it’s crazy but we can say ‘let me show you’.
“Only a couple of weeks ago a customer had an idea, they thought it was innovative and highly productive, and our view was it can
be, but it isn’t right now.
“They were convinced within seconds of seeing our data. When we walked them through the analytics and the report that summarised how it played out, it was like a switch flicked.
“It’s a great relationship to have and one that’s hopefully founded on trust and technical and commercial competence. It’s how we like to hold ourselves to our own standards.
“In that sense, our suspension design parameters around conventional and new energy are different. The amount of drive torque or breaking and regenerative torque have an impact on suspension and performance.
“We need that knowledge, awareness and understanding of those systems. From a purely engineering view, it’s not that complicated.
“But as the world and technology evolvesevolves, we’re very active in keeping up with whatever those opportunities are.”
Removing weight from the HDrive waste truck design is one of the next steps in Hendrickson’s partnership with the company.
While they will continue to change evolve the platform, it is up to Hendrickson to then create suspension solutions that will work to what the new designs need, addressing the business needs of the truck at the same time.
“One of the things we’re really passionate about and driven in by is the constant reflection that this is a commercial vehicle and it needs to make someone money,” Andrew says.
“With a new energy vehicle, tear tare weight is either more payload or more batteries or a hydrogen fuel system. The other way to look at it is less weight means less fuel burn which is better for the environment regardless.
“Constantly pushing that weight reduction is a huge piece of what we do. It’s a centrepiece you might say. We always look at the entire cost of ownership pictureto the fleet.
“That includes all the productivity, up time, maintenance cost and opportunity cost that wear and tear can drive.”
For over 50 years, Penske has kept fleets and businesses moving forward. From uptown to across the continent and any direction you need, our truck leasing and commercial rental solutions have you covered. Because when your business is on the line, you have everything to lose but even more to gain.
The National Heavy Vehicle Regulator has been active in New South Wales for over two years now, so PowerTorque spent the day at the Mount White Checking Station to see how the transition has changed the interface between the trucking community and its regulator
It was back in August 2022 that we saw the transition of key regulatory functions from Transport for NSW to the National Heavy Vehicle Regulator (NHVR). Australia’s biggest state, in trucking terms, was now being regulated by the same organisation which has that responsibility in South Australia, Tasmania, Victoria, and now, in Queensland.
The rollout of NHVR responsibility faced its biggest task in integrating the massive Transport for NSW agency into its organisation. NSW is a big pill to swallow, but swallow it, it has, without any crises appearing over that first two years. The process in the lead up to the integration was a long and convoluted one, but the preparatory
work clearly eased the process.
The Mount White Safety Stations, both north and south bound on the Pacific Highway, about 50km north of Sydney, are always busy, as trucks have to pull off the highway and pass over the weigh-in-motion (WIM) system. If the axle masses detected are suspect, the traffic light system requests them to pull onto the weighbridge. If nothing comes up, the trucks are directed back out onto the highway.
These locations are the main interface between those working on the road in the trucking industry, and the regulators tasked with ensuring they are doing the right thing. These locations have been a source of friction
between drivers and regulators, but the hope is that the takeover of these locations by the NHVR, who have proved in other states to be able to reduce the tension between the trucking population and the regulators, will have the same effect here.
Having, myself, experienced the interface as a driver, being called in and booked for an over mass axle, it was interesting and a little daunting to experience the scenario from the other side of the glass. Most drivers approach the site with a little trepidation and simply being called into the site may create delays.
The station is normally manned on both sides of the highway, with two men on each side. The team spend their time focusing on the weighbridge and the screening lane in the lead up to the point where the light signals tell the driver to return to the highway or drive onto the weighbridge. They are analysing the traffic as it’s coming through, and dealing with the people coming onto the bridge.
Some of the staff are also involved in mobile patrolling as well, but not so much on the freeway. This team’s remit covers the Central Coast region. One or two mobile crews go out on the road every week for a couple of days. They rotate around, the team also have an inspection pit at West Gosford through which they will rotate a week at a time.
The checking station runs 24 hours a day and on an average day the weighbridge will see 30 or more vehicle.
“That may not seem a lot, but when you do an inspection on one of these trucks and then you’ve got to go through things with the driver and his stuff, then you got to get around the truck, and finally, you go and test this and that,” says one of the team. “It can be half an hour on one truck. It can also take longer. We might be targeting brakes as well, so we’ve got a brake testing machine and we could do, what we call, level two inspection which is a much more detailed inspection.”
NatRoad is the largest Australian road freight transport association supporting trucking businesses.
When you join NatRoad, you get discounts on fuel and tyres, expert advice on HR issues, workplace compliance support, insurance benefits, discounted roadside assistance, and more.
An officer sitting in the control booth or at the desk next to the weighbridge can be watching the various screens with different feeds from the local cameras and has controls allowing them to actually manually direct trucks in.
If a truck looks a bit interesting, maybe there’s something not quite right, they can bring it in. If there’s something they want to look at, they can override the signal which would normally send the truck back out onto the highway, and bring it into the weighbridge. Otherwise, it’s fully automatic, the WIM in the road detects the truck may be overweight and the truck comes onto the weighbridge to confirm whether there is an over loading issue.
On a daily basis there will be consistently over 3,000 trucks passing through the screening lane on each station, northbound and southbound, during the teams’ eight hour day shift. The afternoon and night shift have less traffic coming through, giving an overall 24 hour truck count around 4,500 trucks.
The teams are pulling in 30 out of the 3,000 trucks coming through screening, which equates to a one per cent possibility of being pulled in for some form of check or inspection. The
system improves the odds of finding issues through the dynamic scales in the screening lane, plus the judgement of experienced officers who try to pick out possible non-conformances.
It is the more precise targeting possible with modern technology, like rego plate recognition and a national data base consolidated by the NHVR, as well as the Safe-T-Cam data on where trucks were and when which makes the decision to check a truck even more effective.
“There is still a fair bit to be said for the manual override, and using the naked eye to pull a truck in, even with the technology,” says one of the team. “If we were wanting to target fatigue, for example, they will use the naked eye to look for what they’ve been trained to do, and they’ll be able to have a best guess to pick a vehicle was most likely to have a fatigue related issue, based on the type of vehicle or
if it’s an unfamiliar vehicle.
“Plus, if we have intel on different companies and we see the name of the company on the side of the truck we can bring it in. If we see loads that look a bit funny or if it looks a bit ugly or sticking out on the side or whatever, you can say, we’ll have a look at that.”
The cameras are placed well before the point at which the truck will be diverted back onto the highway. This gives the team the time to have a good look at any truck from a number of angles.
On that screening lane the system does an automatic registration check, which will flag if any defects or any other issues are connected with the particular registration plate. The checks are carried out and any problem alerts are flagged to the roadside team quickly. It’s only a few hundred metres between the point at which the truck enters the screening lane and when it will be sent back out onto the road with an all-clear message of ‘return to the freeway’ on the overhead message board.
Every time there’s an interaction with a truck, if a notice is issued, if there’s an offence history on the vehicle, it’s fed into the database. When the camera checks a rego plate, it goes through the database and the algorithms assess the risk rating of that truck in various areas: fatigue, mass, maintenance, all those sorts of things.
The system then assesses whether the risk rating meets the criteria for the truck to be pulled in for some form of check. The other parameters at play in the decision to bring it in or send it on its way is how busy the station is and how big the team working that shift are. The busier it gets the higher the risk threshold for a truck to be ‘intercepted’. If something’s not right,
PowerTorque is a bi-monthly magazine that has shaken up the Australian road transport magazine sector with a format of sharp news stories and bold feature articles on the diverse character of the Australian trucking market. It presents the people and products of the Australian road transport industry in a style and format that is modern, informative and entertaining. With a circulation that covers the full spectrum of the trucking community, PowerTorque is the leader in a highly competitive industry.
if it can’t pick up a rego plate or it gets confused, its default is to bring the truck in for a check.
The NHVR will also put an alert on certain vehicles for some particular if they want to have a look at it. The amount of data coming into the system
grows every year and is coming from all of the states involved in the NHVR, plus some data from those not participating, namely Western Australia and the Northern Territory. Safe-T-Cam enables the team to track a truck’s movements, checks at other checking stations are recorded. The NHVR also run a confidential reporting line. This level of data is beginning to make the targeting of those doing the wrong thing easier for the NHVR.
The flip side of this is that drivers working for reputable companies and those doing the right thing are spending less time being looked over in checking stations and are generally receiving a lower level of hassle on the highway from regulators.
The WIM screening weight is an estimate and the first task once the truck arrives on the weighbridge is to confirm the estimated masses as an accurate reading. The crew reckon the WIM gets it right 50 per cent of the time, and it’s not right for the other half. The job is to then apply the right sanction for the overload.
If the truck has been brought in by the operator watching the screening lane, the team will have a look around and chat to the driver. Checks are done if anything doesn’t look right. If there is anything non-compliant the appropriate action is taken.
One of the most notable things about my visit to this checking station was how calm and quiet it was. Of course, the NHVR team at this checking station understand they have a journalist in their midst and have to be on their best behaviour. But even when I was behind the glass and not visible to the drivers and not recognisable as someone who was observing the interactions, the attitude of the drivers was always calm and always reasonable.
Anyone from the trucking community who has spent any time at regular checkpoints in the past will know that the interactions between drivers and those regulating them would often get very heated. Many drivers would already be looking for trouble as they pulled onto the weighbridge and this attitude often lead to friction and conflict. This situation also meant that the roadside officers were also always on their guard for trouble and could give back as much as they got.
On the evidence of this day at a roadside checking station in New South Wales, which had a reputation of being the most contentious state for truck drivers, the introduction of the NHVR and its takeover of roadside enforcement appears to have taken the heat out of the interface between the truck driver, the trucking operator and those whose job it is to regulate and ensure compliance with the rules.
Genuine parts promotion for your legacy engine.
Peace of mind guaranteed. Genuine parts keep your legacy engine running strong for your ISX/Gen II/EGR on-highway engines.
(excluding X15)
Scan the QR code to find out more about this promotion.
NHVR Chief Operations Officer Paul Salvati addresses the newest iteration of the National Roadworthiness Survey.
In late 2014, the National Heavy Vehicle Regulator (NHVR) established the National Roadworthiness program, to drive safety and efficiency improvements to Australia’s heavy vehicle fleet.
This program aims to find ways to reduce the safety, economic, and environmental impacts of unroadworthy heavy vehicles.
Through this program, the NHVR developed the National Roadworthiness Survey (NRS), which allows our organisation to monitor the makeup of the nation’s heavy vehicle fleet and gain an understanding into levels of compliance and areas that pose a risk to road safety.
We are able to collect the information needed to determine where both the NHVR and industry are making improvements in vehicle safety, and where we should turn our focus to.
The first iteration of the survey was carried out in 2016, under the National Roadworthiness Baseline Survey (NRBS). This saw authorised officers inspecting 7,130 vehicles across participating states.
The results of the checks carried out as part of NRBS allowed the NHVR to gain a clearer picture of the national state of heavy vehicle roadworthiness.
After the NRBS, the NHVR continued to monitor the fleet by conducting the NRS 2021. Authorised officers from the NHVR and partner agencies conducted the random mechanical inspections of 8,339 vehicles between May and July in every state. It was a huge effort by all involved.
During the survey, each heavy vehicle received a comprehensive visual and mechanical inspection in-line with the National Heavy Vehicle Inspection Manual (NHVIM).
NRS 2021 gave the NHVR important
insight into how the fleet had changed since the NRBS, and the results highlighted progress. The rate of nonconformities had dropped from 48 per cent of units inspected in 2016, to 31 percent in 2021.
The hard work of industry in adopting improved safety practices, were certainly key contributors in driving the downward trend.
However, there is always room for improvement. The NHVR is determined to ensure Australia has one of the safest heavy vehicle fleets across the globe.
I’m therefore pleased to share that the NHVR will conduct the NRS again this year, for an approximate 12-week period commencing in July across all states and territories.
Much like the previous surveys, NRS 2024 will involve a series of detailed inspections to ascertain the mechanical condition of the national fleet and shape future initiatives to enhance road safety across Australia’s heavy vehicle industry.
Authorised officers will undertake random mechanical inspections of approximately 8,500 trucks, buses, and other special purpose vehicles, This will include a detailed visual inspection and mechanical component testing.
It’s important that drivers and operators factor adequate time into their scheduling to accommodate inspections times, which will average around 45-60 minutes, depending on the vehicle type and if there are defects identified.
These mandatory inspections will occur at roadside inspection sites and depots across the country.
We appreciate the survey may cause some disruption for drivers and operators whose vehicles are stopped and understand the importance of
keeping the heavy vehicle supply chain moving.
Where possible, officers will ensure minimal disruption occurs and will carry out these inspections as efficiently as they can. Once a vehicle has been inspected, it will not be inspected again in this year’s NRS.
While this survey is a research program, if a vehicle is found to be non-compliant, then a defect notice or other enforcement action may be taken in line with the NHVR’s normal practice.
I encourage industry to prepare for the NRS by reading the NHVR Daily Safety Checklist and give yourself peace of mind that the vehicle is safe and ready for the journey.
The results from NRS 2024 will be compared to both the 2016 NRBS and subsequent NRS 2021. This next iteration of the survey will help build stronger partnerships and knowledge sharing between jurisdictions, the NHVR and industry via the analysis and public release of the survey findings.
The NHVR recognises that industry works to tight schedules, and I would like to thank all businesses and individuals who will be impacted by the survey for their cooperation with our on-road officers.
Through initiatives such as the NRS, the NHVR is able to drive a safer industry, and we look forward to continuing to work closely with drivers and operators during this time, to ensure their vehicles movements are safe and efficient.
Transport ministers had agreed to reform the Heavy Vehicle National Law to increase the trucking industry’s productivity and simplify the fatigue rules.
As part of the industry’s lobbying for the reforms, ATA Chair Mark Parry met earlier in June with federal Infrastructure and Transport Minister Catherine King. The ATA’s member associations put the case to state ministers.
“The industry’s productivity, safety, sustainability and ability to attract staff depends on ministers getting this right,” Mark said before the meeting.
ATA CEO Mathew Munro said the ATA and its member associations had done everything they could to remind ministers of the importance of the reforms.
“At a time when the Australian economy is barely growing and is going backwards per person, and the cost of living is front of mind for every Australian, we need to do everything we can to improve the productivity of our supply chains,” Mathew says.
“We have worked as a team to remind state and territory ministers of the importance of the reforms, and the importance of sticking to their agreement.”
Mark also said the ministers must agree to press on with the reforms to the Heavy Vehicle National Law.
“The reforms were put together by former NSW Roads and Maritime Services CEO Ken Kanofski. He consulted widely with governments and industry representatives, and reached a compromise that had broad support.
“The ATA and our members had put forward our own, more ambitious, proposal. We agreed to the Kanofski reforms to save the reform process and get results.
“The agreed reforms would
increase the productivity of the trucking industry, which has stagnated since the 1990s. Productivity is the key to increasing wages without inflation, as well as continuing the path towards lower emissions intensity.
“The reforms would increase the productivity of trucks with heavy cargoes by up to five per cent. Trucks could be a metre longer and 30 centimetres higher, so operators would not need as many special permits.
“The truck driver fatigue rules are a maze of random requirements that drivers must meet perfectly. The reforms would simplify their work diaries, make enforcement fairer and reduce penalties to reasonable levels.
“Ministers agreed to all these reforms. They said so in writing.
“But now we understand that their departments can’t agree on the details. Some states are even denying that their ministers reached an agreement at all, despite their
“The industry was prepared to compromise to get a result; we expect ministers and their departments to do the same.
“In addition, ministers must agree on a structured process for continuing the law reform process in manageable chunks, as well as a process for agreeing to minor or technical changes.
“The industry’s productivity, safety, sustainability and ability to attract staff depends on ministers getting this right.”
The Heavy Vehicle National Law applies across Australia except in Western Australia and the Northern Territory.
The UD Quon may be our greatest modern achievement.
From its 2004 introduction with the world’s first ‘Selective Catalytic Reduction System’. To its reinvigoration in 2017, with Euro 6 compliant technology. To today, with the reimagined Enhanced Quon, that continues to break boundaries with greater safety, productivity, comfort and sustainability.
We continue to go the Extra Mile to ensure our flagship Quon is better for business, better for people, and better for the planet.
There’s a reason the UD Quon is the truck Australia trusts.
To find out more, contact your UD Trucks dealer on 1300 BUY A UD or visit udtrucks.com/australia
NatRoad CEO Warren Clark says the NSW Independent Toll Review leaves plenty to be desired.
Past inquiries into heavy vehicle tolling have repeatedly highlighted the unjustified nature of the current three times truck toll multiplier. In 2015, the Victorian Auditor General found no objective assessment of alternative funding approaches, and agencies were unable to justify the tolling of goods vehicles. The 2017 NSW Parliamentary inquiry into road tolling recommended publishing evidence supporting the multiplier, yet seven years later, such evidence remains elusive. In 2019, an industry-commissioned report, including input from NatRoad, showed a lack of operational savings for trucking businesses using toll roads, undermining arguments in favour of the multiplier.
And just last year, we called for the multiplier to be slashed in NSW.
Despite these findings and recommendations, the interim report of the NSW Independent Toll Review has not adequately addressed the central issue. Instead, it recommends further modelling in an attempt to find a justification for a policy that has never stood up to scrutiny. The Review’s failure to confront this issue reflects a broader problem in NSW’s approach to tolling, which prioritises infrastructure financing over transport planning and public policy goals.
reduction. There is also a strong case for independent regulation of infrastructure user charges to ensure fairness.
NatRoad’s recent submission to the Review emphasises several key recommendations aimed at creating a fairer tolling system for heavy vehicles. We argue the current three times truck toll multiplier is unjustified and disconnected from commercial realities. The assumption these higher tolls can be passed onto customers is misguided. Additionally, lower tolls should be implemented for cleaner, lower-emission vehicles to support public policy goals on emissions
Our recommendations to the NSW Government include replacing the three times truck toll multiplier with a two times multiplier and expanding the M5 East and M8 truck rebate for existing concessions. We also advocate for variable lower toll rates to incentivise off-peak journeys, as well as discounts for multiple toll journeys, and exemptions for zeroemission heavy vehicles. Furthermore, we call for the establishment of an independent regulator to oversee new and varied tolling concessions and pricing arrangements.
While we agree with some findings of the review, such as the need for independent toll setting and off-peak
pricing, we believe that any reform package that fails to reduce the three times truck toll multiplier will not alleviate the undue burden on NSW small businesses and supply chains. Meaningful reform is essential for a fair and sustainable transport system.
NatRoad remains committed to advocating for the interests of the trucking sector, and we will continue to push for changes that promotes fairness and efficiency in heavy vehicle tolling, both in NSW and nationally.
The all-new 100% electric Fuso eCanter leads its class with advanced safety features as standard. It’s the only electric truck with both Advanced Emergency Braking System (AEBS) and Active Side Guard Assist (ASGA) to detect, brake and stop* for cyclists, moving pedestrians, and cars when the truck is driving or making a left turn.
*Operating parameters and conditions apply as specified in the Fuso Owner’s Manual. Fuso and eCanter are registered trademarks of Mitsubishi Fuso Truck and Bus Corporation.
Descending from a long line of shearers and sheep farmers, Mark Williams is a primary producer and shearer based outside of Goulbourn in New South Wales.
Like most of the Williams family, including wife Sally and daughter Piper, Mark confesses to being a bit sheep mad—which is put to good use on the family farm.
“The day starts about six o’clock in the morning, and just goes from there, often late into the night if it’s birthing season or if the weather is frosty and we need to shed the sheep and lambs in from the cold and safe from predators,” said Mark Williams.
“Some weeks I will be on location,
camped out and shearing, then the week after I will be back home on my own farm.”
Mark previously made use of utes to tow their trailer-mounted sheep crates, but with the farm only getting busier, they no longer offered the desired payload for transporting sheep in safety and comfort.
A vehicle upgrade became a top priority for this family determined to provide the necessary care and attention to their flocks.
Isuzu Trucks being an established brand name with the local farming industry, Mark knew which brand he wanted to support his own operation.
“When I was a young kid, livestock trucks would go off in the morning, so whenever I could I’d spend the day sitting up in the trucks with the smell of sheep.
“I knew even then that I wanted my own Isuzu truck one day.”
This long-held dream came true as he talked trucks with Truck Sales Consultant Richard Pineros from Blacklocks Isuzu in Wodonga.
With Richard’s assistance, Mark settled on an NQR 87-190 Crew Cab model with two-pedal Automated Manual Transmission (AMT) and a custom sheep crate fitted to the tray.
This workhorse of a truck does the hard yards transporting sheep and tackles a multitude of other tasks for
12,200 kg GCM. And with the weight of the sheep now sitting on the tray, the Williams also had capacity to tow their custom-built trailer if needed.
The truck is powered by Isuzu’s 4-cylinder 16 valve 4HK1-TCC engine, producing140 kW @ 2,600 rpm and torque of 513 Nm @ 1,600 - 2,600 rpm, packing plenty of punch for handling
day’s work.
“Out of all my vehicles it’s my favourite one to drive,” said Mark. “I just love getting up behind the wheel.”
“The NQR is an amazing workhorse with great capability for a customer like Mark, who requires a vehicle for multiple purposes,” said Richard Pineros from Blacklocks Isuzu.
“He wanted a truck that could take on any job around the farm, like moving livestock between paddocks and transporting feed, as well as being able to tow his trailers or take the vehicle on location when shearing.
“He also wanted the ease of an automatic truck without having to compromise on power or towing capacity which the whole family could drive, so the AMT model was the best fit, suiting their needs perfectly,” said Richard.
Mark added his thoughts on Isuzu’s driver-friendly AMT transmission. “I was dubious at the time because I generally drive a manual, but Richard told us that AMT was the way to go... looking back, I’m glad we took his advice, it’s been fantastic.”
Despite the five-hour drive to the
vehicle for me to drive which allows me to take the day however I please,” Mark said.
After this positive experience with Isuzu, Mark is eyeing off a bigger truck for future farming endeavours, saying the family has expansion of the business in mind.
“In the farming game, there are certain bits of gear that just work, and when you have a brand you love, you just stick with it,” Mark said.
“In the future I would love a bigger F Series Isuzu truck.”
Mark’s daughter Piper has followed in the family footsteps, starting her own business as a shearer and pregnancy scanning sheep and cattle.
She’s also recently secured a medium-rigid truck licence to drive the Williams’ new Isuzu truck—all achievements that her parents are proud of.
“My wife Sally gets involved in the business, and I couldn’t do what I do without her,” said Mark.
“Our daughter Piper has also started her own business, building a name for herself—we are both very proud of her.”
Volvo’s engineers have managed to squeeze out 780hp from its new 17-litre engine, which is just enough for the FH16 to knock arch-rival Scania off the top spot to become Europe’s most powerful production truck, PowerTorque’s European Correspondent, Will Shiers, reports.
You can be sure that this new 780hp power rating, released by Volvo Trucks in Europe, led to some soul-searching in Gothenburg. After all, the truck maker is vocal on its carbon reduction targets and is busy plugging its full range of electric trucks. Put simply, does taking the diesel horsepower bragging rights from its competitor really fit with its green narrative?
To many it was a surprise that Volvo had been able to channel enough money away from its zerotailpipe-emission budget to invest in a new 17 litre diesel engine platform. But then, as Tobias Bergman, director of press tests told me on a recent driving event in Thessaloniki, Greece, combustion engines form one-third of Volvo Truck’s three-path strategy.
“We are deep into electrification and the transition over to green
energy,” said Tobias. “We will need battery electric trucks, and likely fuel cell electric too. But it’s very important that we must not forget the combustion engine. Not all transport assignments can move to electric tomorrow, and for these unique situations we will still need a combustion engine.”
With its new Aero cab, Volvo is the latest truck manufacturer to take advantage of the 2020 changes to European regulations on masses and dimensions, which permit longer cabs in the name of improved aerodynamics and reduced CO2.
Available on all models of FH and FH16 in Europe, it features a 240mm protrusion at the front. This has allowed Volvo to round-off the cab’s corners, which are areas prone to air flow separation. Surfaces have been
cleaned, and gaps have been filled, all resulting in a far more slippery shape.
Adding to the enhanced aerodynamics is the Camera Monitoring System (CMS) mirror replacement system. The cameras are mounted on 375mm arms, which are less obstructive to airflow than mirrors.
Together, these changes mean the Aero cab produces 11 per cent less drag than the original FH cab (which remains in production), equating to an improvement in fuel economy of up to five per cent.
In addition to the aerodynamic enhancements, Volvo has also taken the opportunity to give the cab a new look. It has lowered the grille, freeing up a panel beneath the windscreen, which is ideal for displaying an operator’s livery.
Like with many things in today’s world, the price has increased, but perhaps not by as much as you might expect. While I was unable to get a figure for the Australian market, I’m told that the Aero cab will add around £4,500 ($8,500) to the price in the UK, the indications currently are that the Aero cab will appear in Australia on electric trucks only.
The FH16 Aero looks very different from the outside, but I get the impression the R&D budget ran dry by the time the designers turned their attention to the interior. Sitting in the cab trying to work out what’s new is a bit like one of those spot the difference competitions. With a bit of help from the demo driver in the passenger seat I was able to identify a couple of additional audio buttons on the steering wheel, and there are now six USB ports instead of four. The audio system has been enhanced (although still doesn’t include Apple CarPlay) and the central 23cm information screen now features an improved user interface.
A-pillars.
My test truck featured the new optional black interior, which does away with the familiar splash of coral (orange), and gives the truck a more sophisticated, grown-up feel. Together with the leather and soft-touch plastics, it lives up to the truck’s flagship status.
While this particular truck had the
extension at the rear of the cab.
The new six cylinder D17 engine is offered in three horsepower ratings, 600hp, 700hp and 780hp. I heard a rumour that the top rating was supposed to be 800hp, but that there were issues getting the
I-Shift transmission to cope with the additional power and torque.
Turning the new key fob (pushbutton starting should arrive in 2025) and 17 litres sprang into life. It was a refreshing change for me to hear a combustion engine on a press trip these days! Thessaloniki’s rush-hour traffic was bad, and I was thankful for the excellent visibility awarded by the sloping side windows.
I have long since admired the FH’s slim mirrors, which result in minimal blind spots on the approach to roundabouts and junctions. Thanks to CMS, things have improved yet again. The screen attached to the driver’s A-pillar is just 30.5cm tall, enhancing visibility further still, and there’s a 38cm screen on the passenger side. CMS felt perfectly natural to use, and I barely gave the system a second thought on the drive.
ADVANTAGES
Australia’s most popular heavy-duty axle
Available in Linehaul (Pumpless) or Vocational (Pumped) configurations
Built tough to suit Australian conditions
I left the city and headed down the coast, so the traffic thinned out.
Now the sensible thing to have done would have been to spend the next few hours using the new and improved I-See function, which takes full lateral control of the vehicle. It uses map data to read the road ahead, determining the truck’s perfect speed. It even recognises
running at just 36 tonnes, and with 22hp per tonne, I intended to enjoy myself. Ignoring everything I had ever been told about fuel-efficient driving I stamped the gas pedal to floor and start grinning ear-to-ear! I even found myself slowing down on the approach to hills, purely so I could accelerate hard on the inclines. My fun was temporarily ruined
disapproving look I get from the wife whenever I pour myself another beer. But unlike her, this was easily turned off and ignored.
While the new FH16’s feisty performance didn’t come as a surprise, what I wasn’t expecting was an obvious improvement to I-Shift. Volvo has clearly tweaked the software to cope with 3,800Nm of torque, and it’s even more refined than usual.
Despite my new reckless driving style, the FH16 took everything in its stride. The Volvo Dynamic Steering coped admirably with some rough Greek road surfaces, and potholes were tackled with unerring grace.
Towards the end of the journey, I decided it was time to act my age, so engaged I-See and let the truck take control. I also had a play with Pilot Assist, which helped to steer the vehicle. It has been developed from Lane Keeping Assist, which used to alert you if the truck strayed out of its lane. Only now it has been adapted to automatically keep you within the lane lines.
Volvo stresses that it’s a driver support system, and is in no way
• 60% less ash than conventional API CK-4
• Extends DPF maintenance period
• Maximises fuel economy
• Prolongs oil change interval
designed to take control away from the driver, who needs to remain in the seat with hands on the steering wheel at all times. For this reason, sensors in the steering wheel continually monitor for human interaction, and the system reacts accordingly if it detects a lack of input.
After 45 seconds of inaction, and plenty of audible warnings, it applies the brakes and brings the truck to a controlled stop. And now for the really clever part, fearing a medical emergency it then automatically illuminates the interior lights and unlocks the cab doors in the hope that a passing motorist will come to the driver’s assistance.
As you’d expect from a safetyorientated marque like Volvo, there are numerous other potential lifesaving aids, such as Side Collision Avoidance, which uses radar sensors at the side of the truck to detect pedestrians, cyclists, and other vehicles.
If any Just Stop Oil protesters had witnessed my heavy right foot in Greece, they would likely have
considered it their duty to glue themselves to my windscreen. Yes, I had some fun with Europe’s most powerful truck, but that clearly isn’t
what the FH16 is designed for.
At the start of this story Bergman said electric trucks aren’t suited to all applications, and that’s exactly where the FH16 comes into its own. Perhaps the perfect example of one of those ‘unique situations’ is Australian road trains, to which the 780hp FH16 is perfectly suited. It’s a similar story in Scandinavia, and some sensible European countries (not the UK), where FH16s are used to pull 60-tonne 25.25m combinations. Sweden has recently pushed the sustainability barrier one step further, introducing a 34.5m 74-tonne combination. It will be a long time until such vehicles will be powered by zero-tailpipeemission drivelines. Until then big combustion engines have a significant role to play, and Volvo’s decision to keep running in the horsepower race is in my view fully vindicated. Your move Scania…
When Volvo launched its Camera Monitoring System (CMS), it acknowledged that it wasn’t the first to market, but stressed that this was because it wanted to ensure that the system worked well. In addition to all the familiar features, such as trailer tracking, night-time surveillance, and reference lines to help gauge distances, Volvo has also introduced an infra-red Night Mode. Although I didn’t get the chance to use it myself, Volvo says it provides classleading vision in low-light conditions.
It certainly looks impressive in the pictures I was shown at the launch event. I am told that CMS is also unlikely to flicker in response to car LED headlamps, which is a common problem with some rival systems.
With the end of financial year upon us, find out how you can easily claim your fuel tax credits.
KPMG Australia and global telematics technology company Geotab have announced a new alliance that enables KPMG’s clients to access Geotab technology, thereby expanding KPMG’s comprehensive fleet solution offering and allow KMPG Australia and Geotab help to claim fuel tax credits.
A key example is KPMG’s FTC Automator, which analyses vast amounts of data at speed and scale, and harnesses proprietary geospatial analytics to process this data, before feeding it into the tax engine to produce Fuel Tax Credit (FTC) entitlement calculations.
The alliance coincides with a favourable ATO Product Ruling that ensures certainty over the tax implications of using the FTC Automator. Product rulings are important as they provide taxpayers with protection against penalty should the ATO subsequently dispute a claim made using the technology.
The technology helps organisations calculate their entitlements for credits on fuel excise, which apply to fuel used in plant, equipment, heavy vehicles and light vehicles (when not used on non-public roads). (PR 2024/1 | Legal database (ato.gov.au))
“This is a direct response to market demand for a product that has undergone ATO review and testing ahead of its release of a formal, publicly available ruling,” says David P Sofrà, KPMG Australia’s National Leader for Workforce and Innovation, and Tax and Legal’s Chief Technology Officer.
“The ATO Product Ruling sets out the Fuel Tax Credit consequences for KPMG Australia clients using Geotab to calculate their FTC entitlement using KPMG’s proprietary FTC Automator solution.
“Our ability to provide businesses
Make your tax time stress-free.
with access to Geotab’s market-leading technology means not only are we able to support our clients with a holistic, end-to-end fleet technology solution that fulfils their needs, we also have a high degree of confidence in the quality, accuracy and frequency of the
“This is a direct response to market demand for a product that has undergone ATO review and testing ahead of its release of a formal, publicly available ruling”
data we are able to ingest into the FTC Automator.”
The FTC Automator is also able to surface important insights on safety, carbon emissions, fleet optimisation, as well as how viable it is for some, or all, of an organisation’s fleet to be electrified.
“Our clients are increasingly
In Australia, transport contributes 19% of the country’s total carbon emissions. By 2030, it is estimated that the transportation sector will become the country’s largest source of emissions. Driven by this concern, many organisations are starting to adopt Electric Vehicles (EVs).
In 2023, Australia has seen a 120.5% increase in the sale of EVs as compared to a year ago. For fleet managers, transitioning an entire fleet is a gradual and complicated process. From ensuring that the new EV fleet reduces its carbon footprint to maintaining operational objectives in a cost-effective manner, here’s how telematics can contribute to a seamless transition process.
Telematics assists fleet operators navigate the complex transition by providing data and industry-leading support. As the transition usually occurs in batches, organisations run on a mixed fleet strategy before they turn fully electric. With Geotab’s data-driven telematics and comprehensive reports, operators can learn how to effectively manage their mixed fleet while operating the new EVs.
Telematics provides fleet operators with improved visibility over all vehicles on a single platform, easing the transition process. Geotab provides heavy equipment fleet managers with both integrated and hardwired options to manage their vehicles. Ruggedized telematics solutions like the GO Device combines traditional fleet management tools with industry-leading data analytics to provide rich, actionable insights.
Telematics takes the guesswork out of the transition process, provides transparency over emissions, fuel consumption and maintenance costs for existing ICE vehicles. Geotab’s Electric Vehicle Suitability Assessment (EVSA) report gathers data about a fleet and compares it with the manufacturers data for EVs in each country, empowering fleet owners to make informed decisions.
After making the switch, remote monitoring and diagnostics capabilities allow access real-time data, enabling prompt and effective vehicle maintenance. Telematics also optimise range management, addressing the common concern of range anxiety and promoting greater confidence in EV usage.
As the climate crisis builds, the need for cleaner forms of transport becomes more prevalent. Telematics will support the expansion of EVs by giving fleet managers the transparency they need to make the change successfully, and by helping governments assess their infrastructure needs.
Learn how to optimise your fleet with Geotab, the leading global telematics provider: www.geotab.com/au/
Nobody wakes up each morning and hopes to spend the day filling out and filing paperwork. Relying on paper and manual processes limits your ability to become more efficient, have better safety outcomes and boost your bottom line.
As Phil Jarratt, managing director of Port of Brisbane-based Jarratt Transport Solutions, recently noted, it’s not 1978, and now’s the time to embrace new ways of doing things.
This includes going paperless. If you’re wondering where to start, perhaps the most effective place to begin is by replacing paperbased fatigue diaries with an Electronic Work Diary (EWD).
EWDs are a powerful tool for both fleet managers and drivers, letting drivers know when they need to take a rest break ahead of time, allowing them to plan ahead for the journey. For fleet managers, EWDs give a real-time view of their mandated breaks and help to understand working hours available to better schedule work safely.
If your company is audited, the evidence you and your drivers have been doing the right thing is at your fingertips as everything is available electronically. No more combing through filing cabinets or directing admin staff to manually process a paper-based document.
Keeping drivers informed about jobs, policy changes, and other company information is a nightmare in a paper world. Documents get lost, not everyone has access, the documents easily get outdated, and managers have no insight into whether the right person has read and understood what they need to.
Teletrac Navman’s EasyDocs, which seamlessly integrates with the TN360 fleet management platform, lets you send documents between base and drivers even without a network connection. You’re also informed when a driver accepts they’ve read the document and old versions can be set to expire and be deleted from the system.
This eases administrative burdens and frees office staff to focus on tasks that make a difference to the business instead of doing mundane, repetitive jobs. Digital documents also reduce errors and eliminate the need for cumbersome filing and record-keeping.
Before digitisation, maintenance and servicing was something a fleet
operator did to a schedule, not when it needed to happen. Trucks would come off the road because it wasn’t easy to predict when a worn item needed replacing or the vehicle needed preventative maintenance. As any operator knows, unplanned downtime means increased costs and lower profitability.
By ditching paper and going digital with a digital Inspections app, fleet managers can understand when servicing and repair must be done ahead of time. Trucks can be scheduled to come off the road conveniently, avoiding breakdowns and improving safety outcomes for drivers and other road users.
With Teletrac Navman’s TN360 fleet management platform, operators have the power of data at their fingertips. It provides a real-time view of their fleets, driver behaviour, and truck maintenance schedules.
Paper is so 1978. Now is the time to improve productivity, efficiency and profitability by going paperless and digital. Start your journey into digitising your fleet management.
Our digital fleet management solutions are designed to ease the administrative burden on your team, while improving your driver’s workflow. From digital documents right through to electronic forms, TN360’s suite of apps can help you and your business transform the way it works. Now that’s choice.
Adding a safety management system to your fleet can have major benefits aside from just meeting legal and regulatory standards.
Safety on the road is paramount, particularly in the heavy vehicle industry where the stakes are high.
As fleet managers, ensuring the safety of your drivers and compliance with Australian laws is not just a regulatory necessity but a moral obligation.
The Heavy Vehicle National Law (HVNL) mandates stringent safety measures, making the implementation of a Safety Management System (SMS) a critical aspect of operations.
It’s important to understand the essentials of SMS for transport operators – Hubfleet has provided practical tips for setting one up, and highlight the benefits of using an all-inone digital solution like Hubfleet.
A Safety Management System (SMS) is a structured approach to managing safety, including the necessary organisational structures, accountabilities, policies, and procedures.
For transport operators, an SMS helps identify, assess, and control risks associated with heavy vehicle operations, ensuring that all safety
aspects are managed proactively and effectively.
Under the HVNL, all heavy vehicle operators in Australia are required to implement and maintain effective safety management systems. These regulations are designed to mitigate the risks associated with heavy vehicle transport, including driver fatigue, vehicle maintenance, and load management.
Compliance with these laws not only helps avoid legal repercussions but also enhances overall operational efficiency and safety.
1. Conduct a Comprehensive Risk Assessment: Begin by identifying all potential hazards associated with your operations. This includes analysing routes, vehicle conditions, and driver behaviours. A thorough risk assessment allows you to prioritise safety measures and allocate resources effectively.
2. Develop Clear Policies and Procedures: Establish clear, concise policies and procedures that address identified risks. These
should cover all aspects of your operation, from vehicle maintenance schedules and driver training programs to emergency response plans. Ensure these policies are documented and easily accessible to all staff members.
3. Implement Regular Training Programs: Continuous education and training are vital. Drivers and other personnel should be regularly trained on safety protocols, fatigue management, and emergency procedures. Training programs should be updated periodically to reflect new regulations and industry best practices.
4. Utilise Technology for Monitoring and Compliance: Leverage technology to monitor compliance with safety standards. Telematics systems can track vehicle performance and driver behaviour, providing real-time data that can be used to identify and rectify issues promptly.
5. Engage Employees in Safety Culture: Foster a culture of safety within your organization by involving employees in the development and implementation of the SMS. Encourage open communication and feedback,
making safety a collective responsibility.
6. Regularly Review and Improve:
An SMS is not a one-time setup but an ongoing process. Regularly review and update your system to adapt to new risks, technological advancements, and changes in regulations. Continuous improvement ensures that your safety measures remain effective and relevant.
In today’s digital age, managing an effective SMS can be streamlined through advanced technology. Hubfleet offers an all-in-one digital solution that simplifies the complexities of safety management, providing numerous benefits for transport operators.
1. Centralised Data Management: Hubfleet’s platform consolidates all safety-related data into a single system. This includes driver Electronic Work Diary (EWD)
records, vehicle maintenance logs, compliance reports, and risk/ hazard assessments. Centralised data management ensures that information is easily accessible and manageable.
2. Real-Time Monitoring and Alerts: With Hubfleet, fleet managers can monitor vehicle performance and driver behaviour in real-time. The system provides instant alerts for any deviations from safety protocols, allowing for immediate corrective actions. This proactive approach helps prevent accidents and ensure compliance.
3. Automated Compliance Reporting: Hubfleet automates the generation of compliance reports, saving time and reducing the risk of human error. The system ensures that all regulatory requirements are met, and documentation is up-todate, facilitating easier audits and inspections.
4. Enhanced Communication: The platform supports effective communication between
management and drivers. Policies and procedures can be delivered digitally, ensuring that all personnel are up-to-date with the latest safety practices. Feedback mechanisms also enable continuous improvement.
5. Cost Efficiency: By automating and streamlining safety management processes, Hubfleet reduces administrative burdens and operational costs. Efficient management of safety measures translates to fewer accidents, lower insurance premiums, and improved overall profitability.
Implementing a robust SMS is essential for transport operators aiming to enhance safety and comply with Australian heavy vehicle laws. By following practical steps and leveraging digital solutions like Hubfleet, fleet managers can create a safer, more efficient, and compliant operation.
Get in touch with Hubfleet for more information on starting your digital safety management system.
In the trucking and heavy vehicle industries, productivity can make or break a business.
In a country as industrious as ours, drivers travel thousands of kilometres every day of the year across cities and states. This need to keep moving is why a fully automatic Allison transmission is the preferred choice of many local businesses.
Fleet owners and operators understand that when it comes to reliability, productivity and ease of operation, no other transmission comes close to Allison.
As a result, Allison is Australia’s number one choice for fully automatic transmissions in medium duty and light heavy duty truck sales.
According to Robert Cavagnino, Australian Sales Manager for Allison Transmission, the sustained success and popularity of Allison in Australia comes down to its longstanding reputation of quality products and its close relationships with leading OEMs. Allison is able to cater for both the local environment and individual customers’ bespoke needs.
As Robert says, “To keep our transport industry running smoothly - literally - you need reliable, highperforming and easily serviced transmissions. From logistics fleets to emergency fire vehicles and hire equipment, there’s an Allison that can make your job easier.
“We know commercial vehicles are not one-size-fits-all. Our customers have different applications, different duty cycles and unique demands.”
An Allison transmission can help you do more work in less time, which is the name of the game in transport and distribution.
They provide superior startability, faster acceleration, higher average speed, more kilometres per day and as result of all that, increased productivity.
“With greater reliability comes
greater productivity,” Robert says.
“We know that our customers rely on our transmissions to ensure their vehicles spend less time being maintained, and more time making their business profitable.
“They cost less in the long run due to their unique design which requires less maintenance. This leads to an Allison being more economical to run and costing less over the vehicle’s lifetime.
“For example, since Allison fully automatics use a torque converter instead of a dry clutch, wear and tear and subsequent maintenance and servicing are greatly reduced.
“Of course, every transmission, no matter how well designed and built, will require some level of servicing. And for that, Allison has an extensive network of 57 authorised distributors and dealers across Australia and New Zealand.”
Better manoeuvrability is another huge advantage of an Allison. When driving uphill or downhill with a heavy load, Continuous Power Technology allows Allison fully automatic transmissions
to deliver uninterrupted engine power to the wheels for improved overall manoeuvrability.
The smooth shifting provided by Allison fully automatic transmissions eliminates jarring gear changes and creates a much smoother and more seamless ride for both driver and cargo.
For younger or inexperienced fleet drivers – many of whom aren’t used to driving a manual transmission – an Allison will make their job easier while also protecting your vehicle asset from unintended, potentially expensive, wear and tear.
Starting with a fully automatic also provides greater flexibility to hire people into roles based on other skills – such customer service or sales – rather than their ability to drive a manual. This increases the employment talent pool significantly in an already tight market.
“When you add it all up, you’ll realise that Australia has a lot to gain from fully automatic Allison transmissions – a better driver experience, productivity gains and, ultimately cost savings,” Robert concludes.
Once you’ve tried Allison transmissions, you’ll never shift.
Allison Transmission is the choice of the transport industry for fully automatic transmissions. Fleet owners and operators understand that when it comes to reliability, productivity and ease of operation, no-one comes close. What’s more, our national distribution and dealer network is here to provide all the support and maintenance you’ll need. That’s why Allison is Australia’s number one choice for fully automatic transmissions in medium duty and light heavy duty truck sales.
Trailer air disc brakes are designed to withstand harsh conditions like heat, dust, and water spray. However, if water enters an air disc brake calliper, it will eventually fail. Let’s explore what technicians can do during service to prevent this.
First, it’s crucial to understand the calliper components that protect the piston, adjuster lever, and self-adjusting mechanism.
These components include the piston boot and guide pin boots, brake chamber, adjuster boot, and adjuster plug. They must be in good condition and properly installed to function correctly.
If water gets into the calliper, it will cause ongoing damage to the internal mechanism until the brakes fail.
Subheading//Piston boot
The self-adjusting mechanism needs to be completely free from contaminants like dust and corrosion to work effectively. This is only possible if the piston boot is undamaged.
If a torn boot is discovered during service, inspect the piston for signs of dust or moisture. If there is any doubt at all, replace the entire calliper to ensure proper operation in service.
The brake calliper adjuster is sealed against water and dust in two ways: a boot around the adjuster and an adjuster plug.
The adjuster boot needs to be clean and in good condition. The yellow adjuster plugs are removed for pad replacement and are often not replaced, which leaves the adjuster boot unprotected to deal with dirt and grime on its own.
Mud, dust, and regular movement will wear away the sealing face of the adjuster boot. This is why the adjuster plug must always be reinstalled after service.
An often overlooked source of water in brake callipers is from the brake chamber. Problems can arise from
either an incorrect mounted chamber or from repeated driving through flood waters.
Before installing a brake chamber, ensure the seal and sealing face are in good condition and apply a thin layer of grease on the seal.
Uneven tightening can cause the calliper to cock over and not sit flush, while under or over torquing can cause distortion or movement that will allow for water leaks.
Even a correctly mounted brake chamber can allow water ingress if the vehicle is repeatedly driven through flood waters.
Flood waters contain grit and grime that can accumulate on the piston rod, which will cause accelerated wear of the piston rod seal. It may be best to replace chambers that have been covered in flood waters.
Calliper guide pin bushes wear out, guide pin boots can be torn by debris, and guide pin caps can be punctured by stones and rocks. Inspect guide pin boots and caps for punctures or deterioration. Guide pin bushes should not have more than 2mm of free play. Replacing worn guide bushes minimises calliper movement and uneven pad wear.
By carefully inspecting and repairing these Hendrickson trailer air disc brake components, technicians play a key role in ensuring trailers remain operational and safe despite occasional adverse operating conditions.
THE HINO 700 SERIES - SUPERIOR TECHNOLOGY AND DRIVER COMFORT.
Work conditions play a vital role in attracting the right people, that’s why the Hino 700 Series has been designed around the needs of the driver. Quite simply it offers high levels of driver comfort with everything you need at your fingertips. Starting with the next-generation driver’s seat, wraparound dash, steering wheel controls and either an automated manual or automatic transmission for a smoother and easier driving experience. The 700 Series also provides a safer experience with an enhanced Hino SmartSafe package, which aids in safeguarding your drivers, the community and your business. The Hino 700 Series - built with the driver in mind. Find out more at hino.com.au